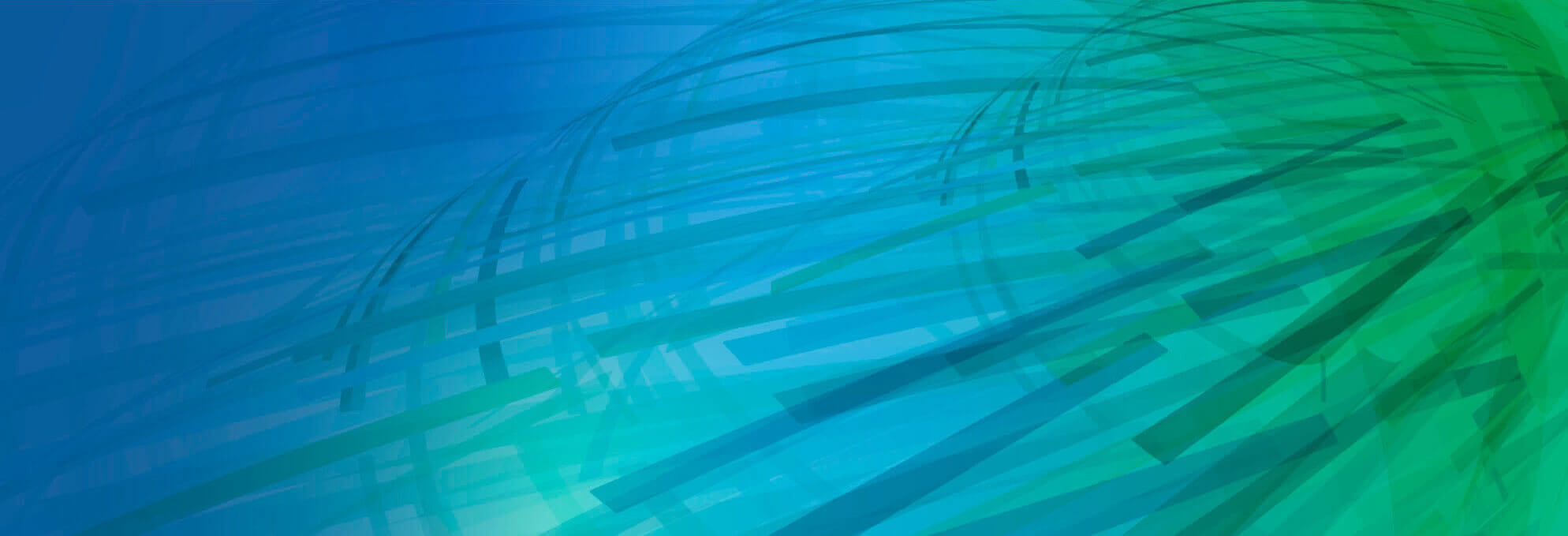
PDA Manage Your Aseptic Filling Line Training Course
Become a Sponsor and/or Exhibitor
Registration Options
Individual Registration
Group Registration
This training course provides a comprehensive understanding of aseptic filling, beginning with EU GMP Annex 1 and regulatory requirements. It explores barrier types, highlighting their limitations, and covers material transfer within the Barrier System and Filling Line. Emphasis is placed on the significance of first air and its consideration in different contexts.
Participants learn to differentiate primary packaging containers and associated filling line technology through visual aids. The course delves into various filling technologies, comparing single-use systems and conventional alternatives.
Indirect product contact parts are explained and distinguished using visual materials, followed by principles and execution of an environmental risk analysis for viable and total particle monitoring. Regulatory requirements for sterile filtration are detailed, including filter integrity testing such as PUPSIT.
Hands-on training involves e.g., the installation of the filling path with closed doors and a barrier glove system. Participants gain practical experience in unwrapping and installing indirect product contact parts, understanding the sequence for open-door and closed-door interventions. The training covers first air requirements, handling settle plates, and active viable monitoring, including opening, positioning, and discharging from the barrier. Participants also learn the proper handling of sterile connection devices and the filtration process, including wetting, flushing, and filter integrity testing. This comprehensive course ensures participants are well-equipped with both theoretical knowledge and practical skills for aseptic filling processes.
Learning Objectives
Lecture 1: Annex 1 Requirements on Aseptic Processing
- What is important to consider about aseptic Filling according to Annex 1
- Which Barrier Technologies exist and what is important to consider
- How to select the right material transfer in the Grade A Zone?
Exercise 1: Set-Up Filling Path
- Practice the installation of complete a SUS filling path
- Develop an understanding of the criticality of the handling
Lecture 2: First Air
- What is important to consider about First Air
- How does First Air Design look like
- What should be avoided about First Air
Exercise 2: Set-Up Indirect Product Contact Parts
- Practice the installation of all indirect product contact pats
- Develop an understanding of the criticality of the handling
- Get a feeling for dimensions and weights of parts during set-up
Lecture 3: General Filling Line Design
- Compare the different filling path possibilities
- Classify indirect or direct contact parts and locations on filling lines
- Categorize different filling technologies
Exercise 3: Filling Set-Up Monitoring Handling
- Practice the handling and set-up of settle plates
- Practice the handling of contact plates
- Practice the handling of swabs
Lecture 4: Environmental Monitoring Risk Analysis
- Examine the regulatory requirements to EMRA
- Develop an understanding of the execution of an EMRA based on examples
- Execute a high-level EMRA based on the lecture
Program Highlights
The joint networking event is kindly sponsored by groninger!
Highlighted Trainers
Key Presenters
Agenda
Discover What's Happening Each Day
Tuesday, 02 September 2025
9:00
Welcome and Introduction
9:15
Lecture 1: Annex 1 Requirements on Aseptic Processing
- Annex 1 and requirements for aseptic filling
- Filling Line Set Up
- What types of Barriers are available and what are their limitation?
- Surface Decontamination
- Gloves
- Material Transfer overview in the Barrier System and Filling Line
- Cleaning requirements and cross-contamination prevention
10:15
Lecture 2: First Air
- Explanation of first air
- Where is first air important to consider
- Examples of first air design
- How to prevent to interrupt first air
10:35
Coffee Break
11:00
Lecture 3: General Filling Line Design
- General differentiation of primary packaging containers and corresponding filling line technology support by visual materials
- Description of different filling technologies with a focus on single use systems vs. conventional filling systems incl. a pro and con overview
- Explanation and distinguishing of indirect product contact parts based on visual materials.
- Understand the sequence of unwrapping the equipment
- General reference to current regulatory guidance documents
12:00
Lunch Break
13:00
Exercise 1: Set-Up of the Indirect Product Contact Parts
- Short filling line walk through to identify points of interest from the theoretical training session incl. a short machine run to understand the process
- Installation of indirect parts as open-door intervention for bigger parts and closed-door interventions for smaller parts using barrier glove system
- Perform sequenced unwrapping with barrier glove system
- Experience first air requirements
15:00
Coffee Break
15:30
Exercise 2: Set-Up of the Filling Path (PP & RPP)
- Hands on explanation of the filling system peristaltic pump and rotary piston pump
- Hands on explanation of a SUS filling kit from needle to surge bag
- Installation of the filling path with closed doors and barrier glove system
- Hands on explanation and differentiation of the function of the indirect product contact parts
- Understand hands on the different wrappings of the indirect parts incl. the sequence of unwrapping.
- Installation of indirect parts as open-door intervention for bigger parts and closed-door interventions for smaller parts using barrier glove system
- Perform sequenced unwrapping with barrier glove system
- Experience first air requirements
17:00
Q&A and Questionnaire
17:40
End of Training Course Day 1 & Networking Event
Wednesday, 03 September 2025
8:30
Lecture 4: Environmental Monitoring Risk Analysis
- Presentation of the environmental risk analysis (EMRA) from the training machine
- Understanding of the principles and execution of an EMRA for passive/active viable and total particle
- Understand the principles of requirements to surface sampling and swapping incl. reference to respective surfaces
- References to current regulatory guidance documents
- Execution of an own high level EMRA
9:30
Exercise 3: Filling Line Set-Up Monitoring Handling
- Handling of settle plates and active viable monitoring incl. opening of wrapping, positioning, opening, and closing as well as discharging it from the barrier
- Handling of contact plates incl. application on parts of the filling line. Closing of contact plates and discharging it from the barrier.
- Handling of swabs incl. application on parts of the filling line. Closing of the swab tube and discharge from the barrier
10:10
Coffee Break
10:40
Exercise 3 (cont.): Filling Line Set-up Monitoring Handling
- Handling of settle plates and active viable monitoring incl. opening of wrapping, positioning, opening, and closing as well as discharging it from the barrier
- Handling of contact plates incl. application on parts of the filling line. Closing of contact plates and discharging it from the barrier.
- Handling of swabs incl. application on parts of the filling line. Closing of the swab tube and discharge from the barrier
11:20
Lecture 5: Sterile Filtration
- Regulatory requirements for sterile filtration: Annex 1 is the baseline
- Filter validation to ensure bacterial retention, to evaluate adsorption and leachables, to ensure compatibility
- Filter integrity test: PUPSIT or risk assessment, bubble point or diffusion?
- Filtration process considerations: is redundant filtration a must?
- Keep it closed: the filter as part of a closed single-use system
12:30
Lunch Break
13:30
Exercise 4: Set-Up of Sterile Filtration
- Best design practice: build your filtration set -> two groups
- Handling of sterile connection device to connect to the filling operation
- Handling of filtration process: wetting, flushing, filter integrity testing
15:00
Coffee Break
15:30
Wrap-Up & Questionnaire
16:20
End of Training Course
Promotions and Press
Request Press Pass
Submit Your InformationLocation and Travel
Venue Details and Accommodations
PLEASE READ PDA is not affiliated or contracted with any outside hotel contracting company. If someone other than PDA or the PDA chosen hotel contacts you suggesting that they represent any PDA event, they do not. It is PDA's recommendation that you book your hotel directly through the official PDA chosen hotel that is listed on our web site.
groninger & co. gmbh
Sulzbrunnenstraße 1Crailsheim, Germany 74564 Germany
PDA recommends the reservation at the following hotels
Meiser Design Hotel
Neue Allee 4
91550 Dinkelsbühl
Germany
The hotel is located 25 minutes by car from the training course venue. A complimentary transfer service will be available from the recommended hotel. To arrange for this service, please contact us at programs-europe@pda.org.
Stadthotel Crailsheim
Worthingtonstrasse 39
74564 Crailsheim
Germany
The hotel is located 5 minutes by car from the training course venue. Please note that no transfer service will be provided from this hotel. Participants are responsible for arranging their own transportation to the facility.
Registration
Pricing Options
Standard Registration
Member Price
€2,200Non-Member
€2,200
ALL PRICES IN EURO (EUR), EXCLUDING VAT.
WAYS TO REGISTER: 1. Online Registration 2. registration-europe@pda.org
PDA MEMBERS: Please remember to log in before registering If you come from a Governmental or Health Authority Institution or from an Academic Organization, please contact registration-europe@pda.org before registering.
If you need to apply for a visa to enter the event country, PDA Europe must be informed of this fact at least 4 weeks before the start of the event.
Sponsor information will be available soon
We're currently finalizing our list of sponsors and will share the details shortly.
Become a Sponsor and/or Exhibitor
Amplify Your Presence and Reach Your Customers!
Become a Sponsor
Elevate your brand and maximize your exposure by becoming a sponsor at the PDA Manage Your Aseptic Filling Line Training Course! Connect with industry leaders, showcase your products and services, and establish your company as a key player in the field.
Request InformationBecome an Exhibitor
Boost your brand and visibility by becoming an exhibitor at the PDA Manage Your Aseptic Filling Line Training Course! Connect with industry influencers, showcase your products and services, and position your company as a key player in the field.
Request InformationHave a question or need assistance?
Send us a message, and our team will get back to you shortly. We're here to help!