4 Ways to Manage Your Supply Chain and Mitigate Drug Shortages
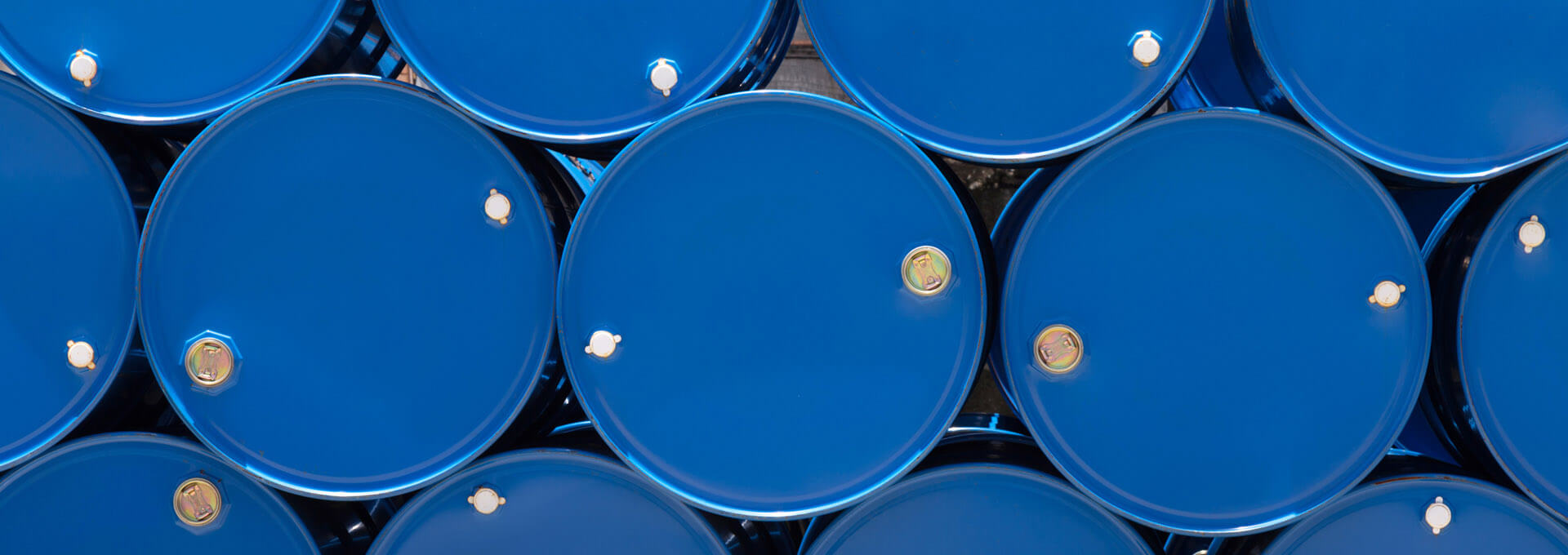
Drug shortages, a topic which roared into headlines in 2011, remains an important concern for the pharmaceutical industry.
The number of new shortages in the United States peaked at 267 in 2011. In response to this crisis and other supply chain concerns, global regulators released several guidances addressing the issue, including the 2011 EU Falsified Medicine Directive, the 2012 U.S. Food and Drug Administration (FDA) Safety and Innovation Act and the 2013 U.S. Drug Quality and Security Act.
While the incidence of drug shortages has generally declined since then, a recent uptick— unrelated to COVID-19—has surfaced in the United States and Europe (1,2). As a result, this continues to be an area of intense focus for the biopharma industry, their suppliers, regulatory agencies and, of course, patients. A 2019 FDA report that detailed potential solutions to the issue of drug shortages cited logistical challenges as one of the causes of the issue (3). With rapid growth, biopharmaceutical manufacturers are increasing their capacity throughout the globe and leveraging contract manufacturing sites. Thus, supply chains have become longer and more complex – making it more challenging to mitigate supply chain risks.
Given the central role of supply chains, more effective management can help minimize the risk of drug shortages. While risk is inevitable and increasing in today’s climate, it all comes down to proactively identifying and managing that risk. And suppliers must be more actively engaged in mitigating the risk of supply disruptions, enhancing visibility and traceability, and enabling process predictability and control. Here are four strategies for ensuring effective supply chain management between manufacturers and suppliers.
1. Share Information and Anticipate Demand
To help secure the supply of life-savings drugs, the relationship between biopharmaceutical manufacturers and key suppliers must evolve into a trusted and transparent strategic partnership. Information, data and ideas need to flow freely throughout a patient-centric supply chain.
Biopharmaceutical manufacturers should engage suppliers in their supply chain risk mitigation process, from both supply and product quality perspectives. This can be accomplished, in part, by sharing basic information with suppliers about the chemicals and consumables specified in manufacturing processes, batch requirements and production schedules. If bills-of-material are used to manufacture a drug on the WHO List of Essential Medicines or a drug for cancer, for example, the chemicals and consumables could be deemed critical by the supplier and result in more robust risk mitigation. This knowledge could influence the supplier’s supply-chain activities, such as forecasting, safety stock inventory planning and dual-sourcing, capacity planning and evaluating high-risk geo-political areas. It may also help the supplier prioritize and allocate activities in the unfortunate event of capacity constraints.
Similarly, sharing information related to critical process parameters and unit operation results could improve quality control and reduce raw material variability. This, in turn, can enhance process characterization and control and enable a more mature quality management system. Ultimately, the action of sharing information can support biopharmaceutical manufacturers in their pursuit of a competitive quality rating.
Generally, suppliers understand that demand will never be 100% accurate or predictable. Yet, if manufacturers were willing to share strategic information affecting their demand-planning — planned inventory strategy changes, terminal buys of pre-change material and such risk mitigation activities as dual-sourcing and large capacity investments, as well as the confidence levels related to their demands — the impact on the overall supply experience and key performance metrics would invariably be positive.
2. Build Relationships
The benefits of a partnership interchange between manufacturer and supplier, where direct and frequent exchanges take place at a strategic, rather than operational and transactional, level can be significant. This dialogue is most effective when manufacturers are willing to share information about their molecules and raw materials and their intended use as well as detailed batch requirements. If the supplier understands the bill of materials, it can identify what the expectation will be on demands. In this situation, proactive and transparent communication allows the collective team to course-correct before a minor incident becomes a major issue. At the end of the day, the goal is to deliver materials to the customer and medicine to the patient. If a supplier does not have the infrastructure in place to handle significant changes in demand, it could open a door to idle biopharmaceutical manufacturing capacity, potential drug shortages and financial losses.
Biopharmaceutical manufacturers should also be prepared to accept an increase in change notifications as suppliers expand their own supply networks, increase capacity and qualify secondary sources. Manufacturers also should prepare to accelerate the acceptance of changes. At the same time, suppliers should follow a robust change management process in alignment with industry best practice guidances. They should provide comprehensive data packages to support customers in accelerating the acceptance of these changes, including acceptance of finished goods from new plants or with second sources of raw materials.
3. Ensure Business Continuity
Perhaps the most important element of supply chain risk management is a robust business continuity strategy, one that seeks to identify, assess, quantify and develop risk mitigation measures.
As part of a business continuity planning process, several dimensions across the supply chain should be examined: raw materials, capacity vs. demand, IT infrastructure and distribution network. A heat map of probability and impact can be used to identify the greatest risks and potential actions to mitigate those risks. In some cases, the solution might be investing in new equipment or a new production facility, ; the adoption and qualification of dual raw material sources or suppliers. Biopharmaceutical manufacturers should map their suppliers; manufacturing sites to know where single-use components and raw materials are actually manufactured. This activity would enable biopharmaceutical manufacturers to take proactive steps in the event of a hurricane, such as prepositioning inventory to avoid stock outs.
4. Apply Consumerization
The principles of consumerization, leveraged successfully in other industries, can also be used to improve the biopharmaceutical supply chain and customer experience in terms of procurement, quality, regulation, operations and logistics. PriceWaterhouseCoopers defines consumerization as “the acknowledgement of the growing role of consumers and the need to develop strategies and market offerings that fulfill their needs and preferences and fully engage them in an end-to-end customer experience” (4).
In a world where consumerization has gone from a trend to an expectation, it pays to draw inspiration from Amazon, Domino’s, Uber and Netflix. These companies in mature industries attribute a good part of their success to providing consumers with a user-friendly digital experiences to differentiate themselves. Their goal is maintaining product quality and supply reliability while simultaneously making it easier for consumers to do business with them.
The principles of consumerization outlined above can be leveraged to improve biopharma industry supply chains and include:
- Real-time visibility of order and shipment information
- Availability and transparency of data to qualify products being ordered and used
- Electronic transfer of product quality information, such as certificates of analysis, certificates of quality and genealogies
- Use of web-based tools to map suppliers and anticipate possible stockouts due to natural disasters and pandemics
Conclusion
Everyone can agree that one drug shortage is one too many and, as an industry, we need to direct our attention to reducing this number to zero. Suppliers to the biopharmaceutical industry are implementing strategies to ensure that their supply chains are more robust and resilient, but they cannot do it alone. Closer collaboration with the industry, along with increased trust among stakeholders and shared information about critical raw material needs — both now and forecasted for the future — will certainly help. In addition, the accelerated adoption and implementation of digital technologies, enabling and facilitating the exchange of data between suppliers and biopharmaceutical manufacturers, will transform how we do business together.
Clearly, everyone in the supply chain needs to work together to solve one of the toughest challenges in life sciences. The accelerated implementation of innovative supply chain strategies will be a major step towards mitigating the risk and number of drug shortages.
References
- Malacos, K. “What Factors Are Contributing to Drug Shortages?” Pharmacy Times (May 20, 2019)
https://www.pharmacytimes.com/publications/issue/2019/may2019/what-factors-are-contributing-to-drug-shortages - Deutsch, J. “Europe comes up short on drug supplies.” Politico (July 10, 2019) https://www.politico.eu/article/europe-still-coming-up-short-on-drug-supplies/
- “Drug Shortages: Root Causes and Potential Solutions.” U.S. FDA, 2019 https://www.fda.gov/media/131130/download
- “Consumerization.” PriceWaterhous https://www.strategyand.pwc.com/gx/en/industries/health/consumerization.html