A Holistic Approach to CCI is a Deterministic Approach
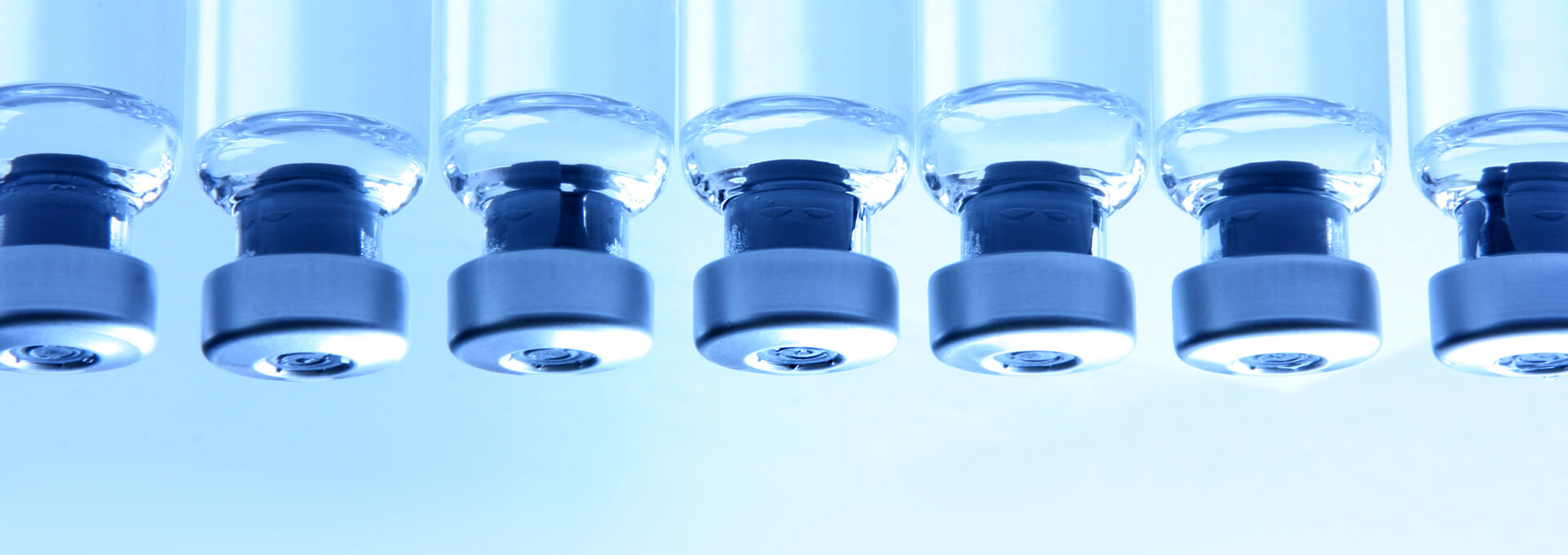
[Editor’s Note: From instructions by the author, this article was taken down July 16, 2024, and updated July 29 by the author.]
Sterile pharmaceutical products need to undergo container closure integrity (CCI) testing at various points in the development and product life cycle to assure product safety.
Mitigating CCI risk involves many dynamic factors and competing objectives. The industry is constantly balancing different considerations to optimize CCI risk management. New container formats and delivery systems are introducing new critical considerations. Regulatory guidance related to CCI is shifting and broadening in scope. A new holistic view of CCI broadens accountability through space and time, assessing container performance and product safety up until the point of use. Three factors - advancing technologies, regulatory guidance and industry frameworks – form the modern context for CCI.
Framing the Issue
The holistic approach establishes an understanding of the dynamic attributes of CCI, aiming to eliminate product risk with a focus on the upstream design process. It is based on the idea that CCI testing should be part of a complete quality strategy that considers the whole product lifecycle. The holistic view of CCI and regulatory frameworks are aligned: understand all the risk factors that affect product quality and address them scientifically. In the product life cycle's design and component selection phase, the risk management framework can offer more tangible opportunities. While design and process risk can be engineered to reduce risk, continuous risk management within the fill-finish realm is a different universe (see Figure 1). Risk management concepts and frameworks that may be readily applied to the design phase may not have a practical or effective implementation in fill-finish.

Quality issues can be divided into two categories: those that are systematic for which design improvements can be engineered in, and those that require routine monitoring downstream. Systematic flaws are assignable and provide an opportunity for engineered improvement. Identifying and removing known quality issues that follow a pattern is the most economical and effective approach for patient safety. The quality established in the design phase matters significantly more than in later phases because small design issues will project into production with higher frequency and severity. Eliminating risk upstream is optimal but does not address ongoing quality risk management. While the holistic view aims to assure improved quality through space and time, the holistic view must also address in-process control strategy within the modern context of CCI.
The fill-finish equipment and process are highly engineered and impacted by critical quality attributes (CQAs). The general categories for fill-finish CQAs are environment, equipment, components, materials, process and personnel. Some CQAs do not affect a product by themselves, but impact can increase risk together. Each of these factors has an opportunity to introduce variance into the manufacturing process. For all quality issues that do not follow a systematic occurrence nor have easily assignable solutions, some regime of routine testing of the final product is fundamental to ensuring quality. Reducing the influence of these continuous risks requires routine monitoring. Ongoing testing at key stages of the product lifecycle will confirm that the product meets the quality standards of both design and ongoing production.
Deterministic Strategies
The approach must be accurate, frequent enough and practical to support the fill-finish operation with effective risk management associated with CCI. Managing CCI risk can be a challenging endeavor for any fill-finish line. The measure must be accurate because CCI is a discrete attribute with a very high impact on patient safety; the measurement must be right. The test frequency must be enough to capture drift, stack-up tolerance and general adverse events. The method must be practical in implementation and should avoid additional costs or burdens. Deterministic CCI test methods provide an optimal solution for a correct holistic approach to CCI.
Accuracy
Integrity is not a variable attribute; it either meets or does not meet the required container performance. Every package format has a Maximum Allowable Leakage Limit (MALL) below which the leak rate is too small to impact the product. Defects above the MALL should be detected, and the risk effectively managed. The process that is deployed must be capable of reliably detecting defects down to those critical sensitivities. Appropriate scientific practice for such high-risk attributes with discrete outcomes would be to focus first and foremost on the accuracy of the scientific measurement. Deterministic methods have controlled and predictable inputs with measured results. At a basic level, deterministic test methods offer a better way to physically evaluate samples than probabilistic counterparts.
Frequency
Once an accurate and effective CCI method has been deployed, improving the frequency of CCI testing is the net priority. The relevant
regulatory guidances for CCI are USP General Chapter <1207>: Container Closure Integrity Testing and EU GMP and Annex 1: Manufacture of Sterile Medicinal Products, which encourage a thorough understanding of the risk and application
of scientifically justified sampling plans. Addressing CCI by prioritizing test frequency will not capture the quality issues that impact patient safety. On the contrary, once an accurate measurement process has been established, providing that measure
as frequently as possible does support patient safety. A deterministic CCI test method with a scientifically justified sampling plan for each phase of the container lifecycle provides the most optimal path for quality assurance.
Risk can be defined by assessing the likelihood of an event, how serious it would be if it does happen and how well it can be detected if it happens. An effective sampling plan reduces risk to acceptable levels in the most efficient way possible. In other words, an effective sampling plan balances the right level of confidence needed to mitigate risk with the least disruption. Testing 100% can eliminate quality issues, but it is inefficient and only works for specific situations. For each population, there is an optimal quantity to test to provide quality assurance for that population. Finding the right sampling plans requires understanding the risk.
Since the fill-finish process will require some kind of batch release and 100% inspection is not a practical means to assure quality, using statistical process control tools for CCI testing may be optimal. There are different statistical methods to set forth the right sample plan. The test method and resulting data may also impact sampling plans. Quantitative data sourced from a deterministic test method will always carry greater confidence than attribute-based methods, achieving similar confidence with smaller sample sets. Sample size and frequency must be backed by a sound scientific assessment of risk and provide an elevated level of confidence in CCI.
Practicality
Deterministic methods offer many practical advantages to improve patient safety. Deterministic methods offer controlled inputs and measured outputs on a quantitative continuum. Quantitative measures allow for calibration, control, significance and regression calculations, and more advanced inferences. The quality of data and level of analysis afforded by data on a quantitative continuum strongly favor deterministic CCI methods. Probabilistic methods require testing significantly more samples to achieve similar confidence levels. Deterministic methods are generally non-destructive, so samples are preserved for further analysis. A non-destructive test method allows for the frequency of CCI testing to be deployed without consideration of destroyed samples. Preserved samples from a non-destructive test and supporting data can be used to get as much information as possible to improve upstream quality. Both attributes of deterministic test solutions make them ideal for pursuing holistic CCI.
Conclusion
CCI testing is a vital quality attribute for sterile pharmaceutical products, and it requires a careful and systematic approach that considers the product, container and life cycle, as well as the regulatory and industry expectations and requirements. The holistic approach faces some limitations in practice that can only be mitigated through added downstream quality sample testing. The most effective sampling plan for CCI testing in a pharmaceutical production environment is based on scientific principles and regulatory guidance, providing the optimal balance between product quality, product safety and performance over the product life cycle.
We exist in a world in which quality issues are inevitable. Material drift, stack-up tolerance and outside influences cause variation regardless of how well a contamination control strategy is designed. Design alone cannot guarantee quality; it can only create the conditions for it, and it depends on all inputs to work. To deliver the best quality product a holistic strategy, one that considers both the design process and a control strategy, is needed. Final batch-release testing is necessary, and it is only a matter of when and how much to test. To achieve the desired outcome for a holistic approach to CCI, the right technologies and frameworks need to be aligned. The concept of a holistic strategy is powerful and effective, and it must address the dynamics of risk at each phase of a product lifecycle.