A Not-So-Sweet Smell: Part I A Review of Contamination Concerns for Wooden Pallets
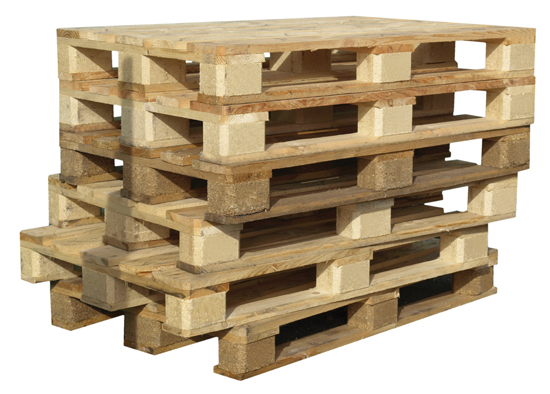
[Editor's Note: Read Part II here.]
The humble wooden pallet continues to play a vital role in the pharmaceutical industry. Production materials and consumables transported to a production facility are often received and stored on wooden pallets before they are sampled, tested and transferred onto metal or molded plastic pallets for use in production areas. In addition, finished products leaving the production facility are often transferred back on to wooden pallets in the warehouse for shipping and distribution.
With an estimated 1–2 billion wooden pallets currently in circulation in the United States alone (1), wooden pallets remain an intrinsic part of pharmaceutical supply chain management. But wooden pallets possess several innate chemical and physical characteristics that may present potential challenges within the pharmaceutical warehouse. These undesirable characteristics include the possibility of splintering and shedding particles. Additionally, as wooden fibers are inherently absorptive, liquids can affect the wood, potentially resulting in the growth of microorganisms, such as fungi. This article provides an overview of the potential compliance issues associated with the use of wooden pallets in the warehouse, some of the best practices for their management and the associated controls that should be considered as part of GMP/GDP.
Different Standards Available
U.S. FDA cGMP regulation 21 CFR 211.56(c) requires written procedures for sanitation designed to prevent the contamination of equipment, components, drug product containers, closures, packaging, labelling materials and drug products. A similar recommendation for manufacturers of APIs is also described in the internationally harmonized guidance for industry, ICH Q7: Good Manufacturing Practice for Active Pharmaceutical Ingredients (section 4.72)(2). An effective pallet management program should therefore be considered essential to minimize potential contamination of warehouse materials that could be affected by chemical taints or contamination.
It also helps to look at standards not just specific to pharma. International stan- dards, such those set by ASTM and the International Standard for Phytosanitary Measures (ISPM), have been established for regulating the movement of timber through international trade, aimed at preventing the global spread of timber pests (3,4). ISPM standard for wooden packaging (ISPM 15) has been adopted by several countries, including the United States and the European Union, to prevent the international transport and spread of pests when shipping wooden materials greater than six millimeters in thickness between countries. Pallets heat-treated with conventional steam or a dry kiln heat chamber (typically observed with pallets used within pharmaceutical warehouses) should be heated to a minimum core temperature of 56 °C (132.8 °F) for at least 30 continuous minutes throughout the entire profile of the wood, including the core (4). Pallets treated by this method bear a Heat Treated (HT) stamp as part of the pallet marking. Wooden pallets may also be treated using methylene bromide (MB) fumigation following a specific temperature/time-based schedule. Although fumigation is an effective method, the use of MB as an acceptable treatment, according to ISPM 15, is no longer permitted in many countries. Heat treatment of pallets is intended to control invasive species and not bacteria and fungi; therefore, moisture content should be considered an important pallet specification.
Fungicide and Funny Odor Concerns
When fresh wood is used to construct pallets, the moisture content may vary between 20 and 60 %. A maximum surface moisture content of 20 % for heat-treated pallets was proposed as early as 1946 as necessary to prevent mold growth (5), and a residual moisture content of 20 % or less is generally considered the industry standard for kiln-dried pallets (1). In warehouse environments with suitable airflow, the moisture content is likely reduced significantly, but in reduced-airflow environments, the moisture content of new pallets may result in potential mold growth, particularly when stored outside or in wet, damp or humid conditions, such as near warehouse doors.
Pallets may also contain wood that has been treated with the fungicides 2,4,6 tribromophenol (TBP) or 2,4,6 trichlorophenol (TCP), both of which have a phenolic smell(1). TBP is used as a wood preservative in some parts of the world, including Central and South America, Eastern Europe and Northern Asia, and is commonly used in hot, humid climates to control mold growth on freshly cut wood (1). The use of halogenated phenolic compounds to preserve wood is becoming increasingly rare, as this practice is either discouraged or prohibited by most countries since the chemicals may be converted to 2,4,6, tribromoanisole (TBA) and 2,4,6, trichloroanisole (TCA), both of which have an unpleasant earthy, musty and moldy aroma (6). TBP treatment of wood, however, continues in some regions that supply wood to the United States and other countries (1).
Another risk involves material transported on wooden pallets in nondedicated shipments. This may result in contamination from untreated pallets in the same vehicle or transporter. Through naturally occurring processes (methylation by ubiquitous fungi) (7), the fungicides TBP and TCP adsorb onto materials stored near the TBA source. Due to their volatility, low levels of halogenated anisole compounds can adversely affect a large quantity of product in a single contamination incident (8).
Many pharmaceutical products have been recalled due to moldy odors, with fungicide-treated wooden pallets identified as a likely cause of product contamination (1). Although nausea has been reported by consumers sensing a musty or moldy odor, adverse event investigations thus far have not shown any conclusive relationship between TBA and gastrointestinal events. And, toxicological studies associated with TBA have shown no mutagenicity or systemic toxicology in rodents (1). The impact of TBA odors appears to be associated with a behavioral reaction of the consumer rather than a patient safety risk.
Due to the high volatility of the compounds TBA and TCA, contamination via migration and penetration into nonpolar materials such as plastics is another possibility. The odors attributable to the presence of a halogenated anisole compound can be detected by consumers even when the compound is present at parts per trillion (ppt) levels, with the human odor threshold for TBA as low as 0.2 ppt (1). Numerous drug product recalls have been associated with TBA taints that have been shown to permeate plastic drug product containers. Regulatory agencies are concerned that patients sensing an unusual odor, one not intrinsic to the product, will increase the likelihood of patients not taking a medication (1).
[Editor’s Note: II of this article will offer some tools for evaluating wooden pallets.]
References
- Sawant, A., et al. PDA Technical Report No. 55: Detection and Mitigation of 2,4,6-Tribromoanisole and 2,4,6-Tribromoanisole Taints and Odors in the Pharmaceutical and Consumer Healthcare Industries. Bethesda: PDA, 2012.
- ICH Harmonized Tripartite Guideline, Good Manufacturing Practice Guide for Active Pharmaceutical Ingredients. Step 4 version, 10 November 2000
- ASTM D6253-16, Standard Practice forTreatment and / or Marking of Wood Packaging Materials, ASTM International, West Conshohocken, PA, 2016
- ISPM 15, International Standards for Phytosanitary Measures, Guidelines for regulating Wooden Packaging Material in International Trade. Secretariat of the International Plant Convention, Food & Agriculture Organisation of the United Nations, Adopted 2013, published Jan 2016
- Cartwright, K. St. G., and Findlay, W. P. K. Decay of Timber and its Prevention. 1st ed. London: HMSO, 1946.
- Whitfield, F.B., Hill, J.L., and Shaw. K.J. “2,4,6-Tribromoanisole: a Potential Cause of Mustiness in Packaged Food”. Journal of Agricultural and Food Chemistry 45 (1997): 889–893.
- Yao, J. D. C., and Moellering, Jr., R.C. 2007. “Antibacterial Agents.” Manual of Clinical Microbiology. 9th ed. Washington D.C., ASM.
- GMP Advisor: The GMP Questions and Answer Guide. ECA Academy, Germany v. 1.0, 2014