A Not-So-Sweet Smell: Part II Strategies for Preventing Contamination of Wooden Pallets
[Editor’s Note: Read Part I here.]
Part I of this article reviewed the available literature on wooden pallets. How can companies use this information to address concerns around wooden pallets?
For one, it is important that pallet manufacturers identify the source of their wood materials. In addition, pallet manufacturers should avoid using any chemical treatment that can induce “anisole taint” or have the potential to contaminate products stored in the warehouse. Drug products, components or packaging materials should not be stored near wood or wood-derived storage materials unless there is assurance that the wood material has not been treated with a halogenated phenolic preservative. Manufacturers should be vigilant for the characteristic odor of offending compounds, so they can intervene before product is potentially contaminated or further distributed.
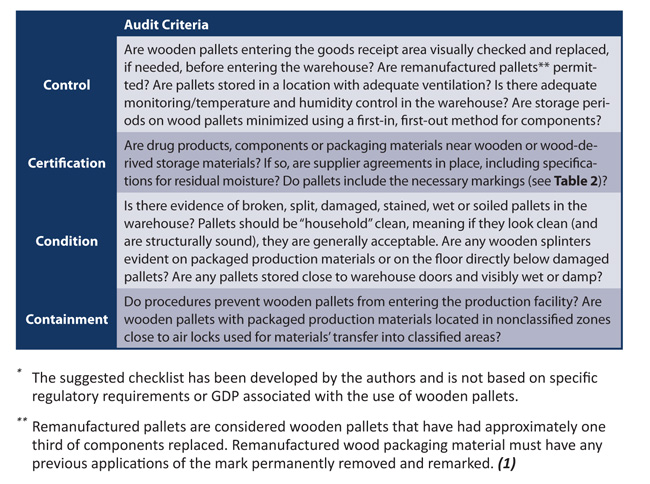
Pallet treatments are not intended to provide ongoing protection from contaminating pests or fungi (1). Management of wooden pallets should be considered as part of a supplier audit program, particularly if drug products, packaging or critical materials entering production areas are transferred into the warehouse and stored on the pallets received directly from the supplier(2). Although methods to detect such contaminating compounds exist (e.g., gas chromatography and mass spectrometry, GC-MS), analytical methods may be impractical for periodic screening; regulators generally expect that manufacturers prevent contamination from wooden pallets through adherence to CGMPs (1). Audit agenda items associated with pallet management are presented in Table 1. It may also be worthwhile to include elements of wooden pallet management as part of an internal audit program(3). Table 2 provides a guide of certain international pallet markings. A comprehensive risk identification matrix associated with wooden pallets can be found in PDA Technical Report No. 55: Detection and Mitigation of 2,4,6-Tribromoanisole and 2,4,6-Tribromoanisole Taints and Odors in the Pharmaceutical and Consumer Healthcare Industries.
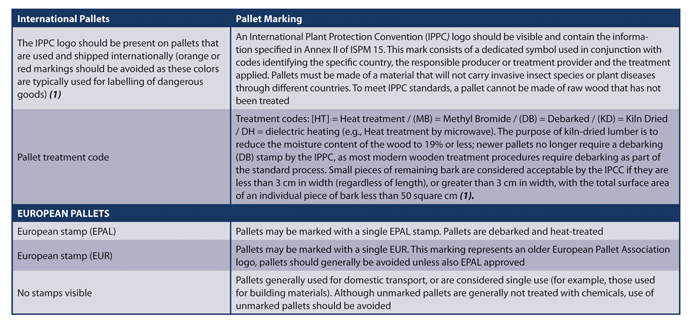
Wooden pallet management in the warehouse begins with good housekeeping, i.e., storing pallets to control the moisture content of wood so it is not conducive to fungal growth. This means storing pallets dry with adequate airflow. Pallets should be odor-free, structurally sound and lack debris and foreign substances. Pallet suppliers should be part of a site supplier management program with agreed and documented pallet specifications (4). With appropriate controls in place, the use of heat-treated wooden pallets obtained from a certified supplier may generally be considered low risk. Wooden pallets remain a source of microbial growth with potential risk of contamination on the surfaces of outer packaging of materials transferred into classified production areas.
The risk of product and facility contamination from wooden pallets is often considered low as outer packaging and cardboard is usually removed, quantities of production chemicals and raw materials are usually dispensed into new containers and many items are repackaged and sterilized before entering production areas. In addition, other GMP systems and controls in place minimize the risk of contamination from the warehouse, such as environmental and personnel monitoring, facility cleaning, HVAC systems controlling airflows and pressure differentials, but there is still a regulatory expectation that manufacturers prevent contamination through adherence to cGMPs and the management of wooden pallets should be included as part of a pharmaceutical manufacturers’ GMP/GDP quality system (5). With appropriate controls in place, a manufacturer can minimize the risk to products and avoid the not-so-sweet smell of wooden pallets within the pharmaceutical warehouse.
References
- ISPM 15, International Standards for Phytosanitary Measures, Guidelines for regulating Wooden Packaging Material in International Trade. Secretariat of the International Plant Convention, Food & Agriculture Organisation of the United Nations, Adopted 2013, published Jan 2016.
- Whitfield, F.B., Hill, J.L., and Shaw, K.J. “2,4,6-Tribromoanisole: A Potential Cause of Mustiness in Packaged Food.” Journal of Agricultural and Food Chemistry 25 (1997): 889–893.
- Montalvo, M. Effective Implementation of Audit Programs. Bethesda, MD: PDA/DHI, 2017.
- Stumpff, J. “FDA Expectations for Supplier Management.” Pharmaceutical Technology 37 (2013)
- “Questions and Answers on Current Good Manufacturing Practices—Buildings and Facilities.” FDA.gov. Dec. 21, 2015 https://www.fda.gov/Drugs/GuidanceComplianceRegulatoryInformation/Guidances/ucm192869.htm#5 (accessed June 7, 2018)