A Toolbox for an Effective Technology Transfer
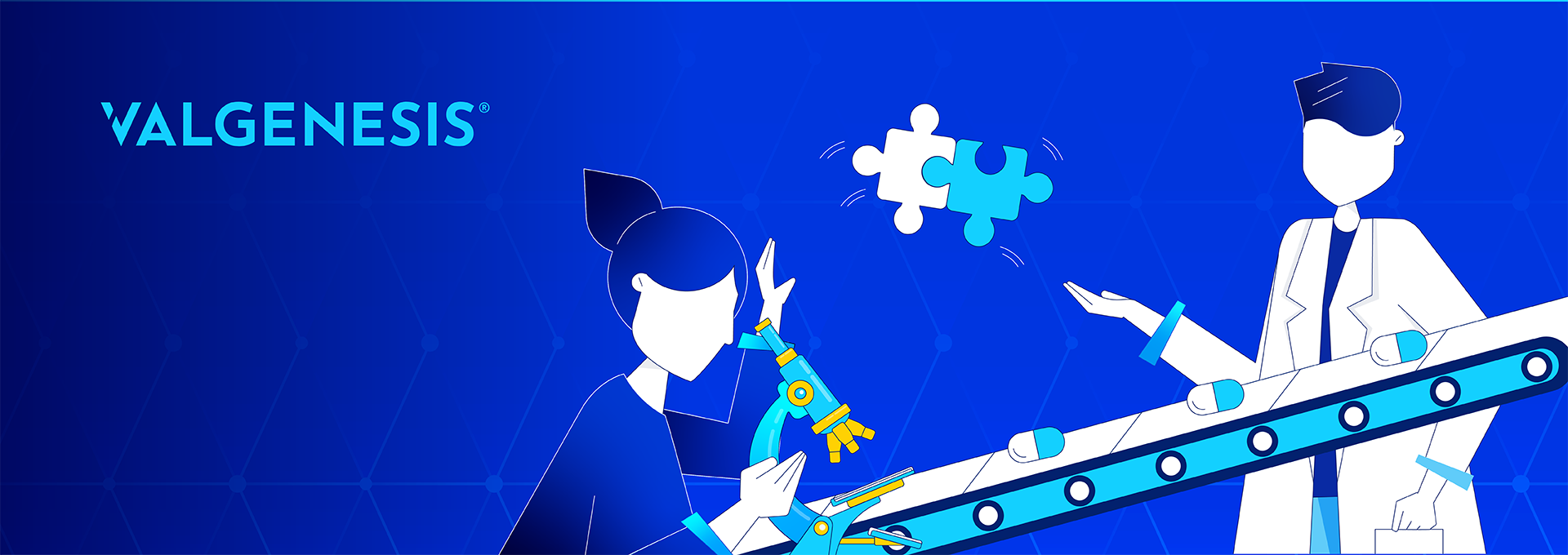
The pharmaceutical industry is undergoing a transformation driven by Pharma 4.0, the next phase of digital innovation. By integrating cutting-edge digital tools and methodologies with advanced technologies, pharmaceutical and biopharmaceutical companies are not only improving efficiency and competitiveness but also embracing a holistic, data-driven approach that is at the core of Pharma 4.0. This synergy underscores the transformative potential of digital innovation in driving the future of pharmaceutical manufacturing.
The Pillars of the Pharma 4.0 Landscape
Pharma 4.0, introduced by the International Society for Pharmaceutical Engineering (ISPE) in 2017, builds on Industry 4.0 principles to modernize pharmaceutical manufacturing. This approach describes the integration of advanced digital technologies in the pharmaceutical industry, such as Artificial Intelligence (AI), the internet of things (IoT), and big data analytics using smart machines. It epitomizes the use of technology to optimize manufacturing processes through digitalization, leading to new levels of connectivity, flexibility, efficiency, and productivity. Pharma 4.0 simplifies compliance, achieves cost savings, reduces downtime and waste, and fosters innovation (1–5).
Pharma 4.0 consists of nine key pillars, encompassing three main areas: technology, digitalization and skills (see Figure 1) (16):
- Technology
- Big Data Analytics: Automation and digitalization generate vast amounts of data during manufacturing processes in Pharma 4.0. To handle this data influx, increased storage capacities are necessary. Big data analytics processes and analyzes these large amounts of data to extract insights that can optimize the manufacturing process.
- Industrial Internet of Things (IoT): The IoT refers to devices equipped with sensors, software, and other technologies that connect and exchange data with other devices. These IoT devices monitor and control various aspects of the manufacturing process, such as temperature, humidity, and pressure, among many others.
- Autonomous Systems: Robotics and automation enhance the manufacturing process by minimizing the need for human intervention. This leads to fewer errors and greater efficiency in production.
- Digitalization
- Cloud-Based Computing and Storage: Cloud computing and storage allow pharmaceutical companies to store and manage various data types. It is the foundation of advanced technologies such as AI, machine learning (ML), and IoT. In Pharma 4.0, cloud storage is usually secured with cybersecurity measures to prevent unauthorized access or breaches.
- Artificial Intelligence and Machine Learning: AI algorithms analyze data from IoT devices and other sources to detect patterns and trends. These findings are employed to enhance manufacturing processes and elevate the quality of the final product.
- Cybersecurity: The integration of standard communication protocols and enhanced connectivity with Industry 4.0 has increased the imperative to protect critical data from cybersecurity risks. Consequently, it has become indispensable to ensure reliable and secure communications and management channels.
- Skills
- Horizontal and Vertical Integration: Currently, most IT systems lack full integration, causing limited connectivity between organizations, customers, and suppliers. However, Industry 4.0 allows for the development of cross-organization, universal data integration networks leading to automated value chains.
- Augmented Reality: Augmented-reality-based systems, still in their early stages, offer diverse functionalities, such as delivering repair instructions via mobile devices. In the future, these systems will provide real-time information, enhancing decision-making processes and optimizing work procedures.
- Advanced Manufacturing: With the implementation of Industry 4.0 technologies, advanced manufacturing techniques such as 3D printing are useful for manufacturing small batches of customized products, leading to enhanced performance or lightweight designs.
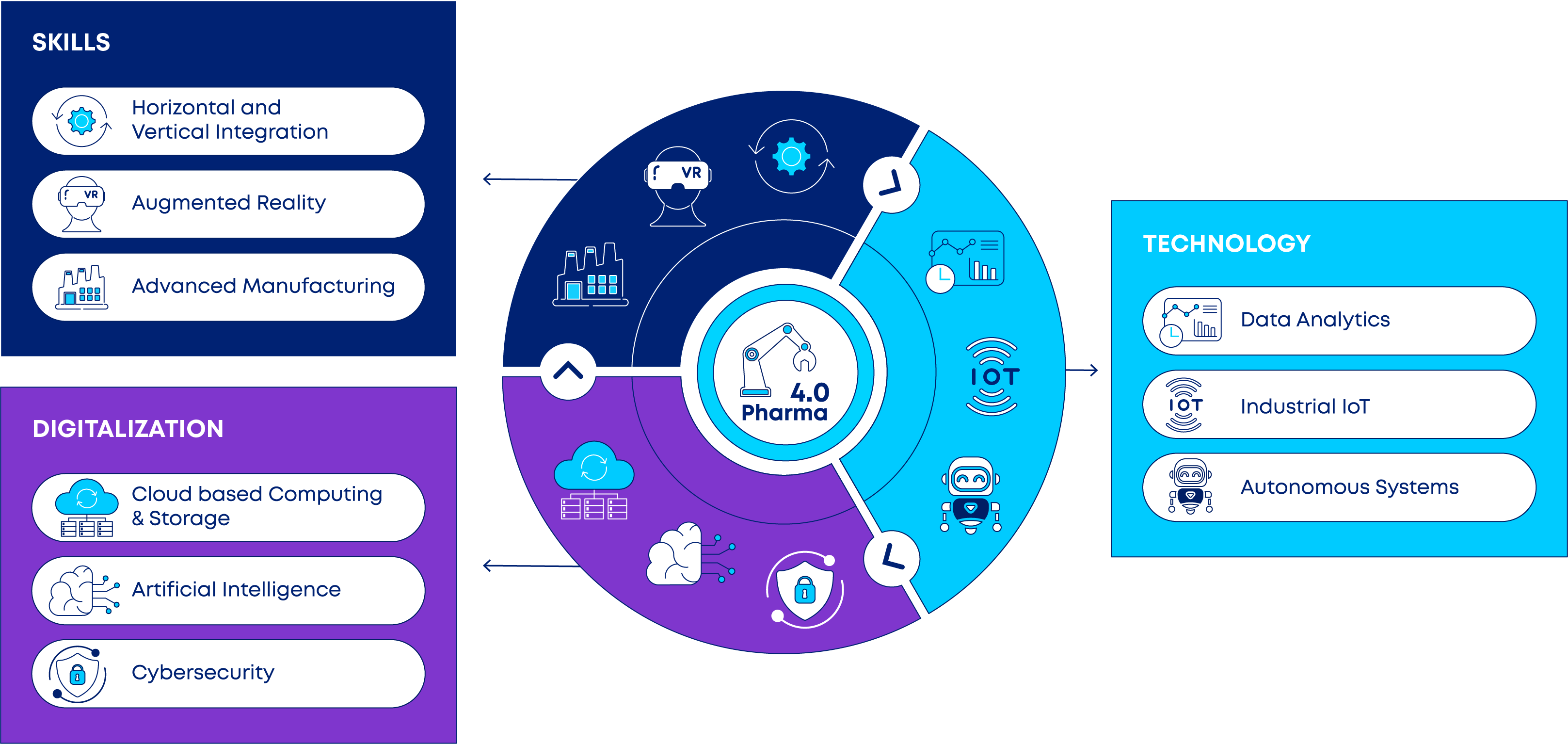
Each pillar represents a digital technology that manufacturers should adopt to improve their manufacturing processes. The combined application of these technologies enables companies to implement smart production and optimize their operations, thereby enhancing consistent product quality and faster time-to-market for new medicines (1,2).
The move towards Pharma 4.0 can be seen in ISPE’s GAMP 5 2nd edition, which was updated in 2022 to reflect the increased adoption of software and automation tools. The updated edition now includes a specific appendix on the use of AI and ML, offering a path for advanced process control to be used in pharmaceutical manufacturing (7,8).
Ultimately, Pharma 4.0 enables the pharmaceutical industry to be more agile and adaptable to constantly evolving market demands, supporting companies in responding to changes in demand and manufacturing disruptions while improving patient safety (2,3,5,7).
Technology Transfer – Synergy with Digital Tools
The implementation of digital tools in the pharmaceutical industry presents opportunities to optimize manufacturing processes, including process design, control, smart monitoring, and maintenance, thereby ensuring the consistent and accurate execution of transferred processes. Moreover, AI-driven data integration, knowledge management, and risk assessment streamline the transfer process and accelerate learning at the receiving site, minimizing risks and ensuring compliance with regulatory requirements during technology transfer.
In successful Pharma 4.0 implementations, new techniques, platforms, and technologies are leveraged into digital toolboxes that enhance existing mathematical algorithms through AI and ML, process monitoring, and optimization tools. Among the many benefits of leveraging these toolboxes into a technology transfer process roadmap, let us consider the following (see Figure 2)(7):
- Process Design and Scale-up
Digital tools, leveraging ML algorithms developed from process development data, swiftly uncover optimal processing parameters for scale-up processes, thereby reducing development time and minimizing waste (9). - Enhanced Knowledge Management
A critical aspect of technology transfer involves data migration, which can present substantial challenges. While the concept of transferring data may seem straightforward, issues such as connection failures can result in data loss and retrieval difficulties. Moreover, existing data often remains unused and proves difficult to transfer due to a lack of structure, connectivity, and context, creating a bottleneck in the technology transfer process. To mitigate risks, it is advisable to migrate data incrementally (10).
During technology transfer, several challenges arise (10):
- Data Collection Completion: The initial stages of product development involve numerous trials and errors, generating a substantial influx of data. Stakeholders must meticulously record relevant data from these stages and employ proper methodologies and guidance to manage vast amounts of data effectively. Without adequate recording systems in place, data may remain underutilized, leading to statistically unsound analyses and missed insights.
- Data Accuracy and Integrity: Beyond data completeness, it is essential to ensure the accuracy and integrity of recorded data. This involves implementing robust recording methods, verifying data during the recording process, and selecting appropriate recording tools, whether digital or manual.
- Structuring and Retrieving Data: Organizing data into coherent structures is pivotal for enabling stakeholders to locate and access the required information accurately. In industries like pharmaceuticals and biotechnology, where data structures can be intricate, experts play a crucial role in planning data collection and organization strategies to ensure meaningful and logical arrangements.
In the era of big data, maintaining data integrity is paramount. Within a digital toolbox, AI algorithms are adept at detecting anomalies, ensuring data accuracy, and preventing tampering. Machine learning models can analyze vast datasets, identifying patterns that might elude human inspection. This strengthens data integrity throughout the pharmaceutical product lifecycle.
- AI-Enabled Risk-Based Approaches
Digital tools have the potential to revolutionize quality risk management (QRM) within the ICH Q9(R1) framework.
The ability of AI to process complex data quickly and accurately makes it an ideal tool for real-time risk assessment, decision-making, and mitigation. By proactively identifying potential risks in large datasets, AI can detect patterns, identify correlations and relationships, and improve the accuracy of risk assessments (11).
Automated risk assessments streamline risk assessment procedures and foster a systematic, proactive approach to risk management. Real-time monitoring continuously tracks critical quality parameters, with AI analyzing data to uncover risks that may be difficult to detect using traditional methods (11).
- Advanced Control Strategy
Digital tools can also be employed to develop advanced process controls that predict manufacturing process trajectories using real-time sensor data combined with AI methods. These controls, known as soft sensors, offer an effective alternative to traditional hardware sensors for gathering, monitoring, and regulating crucial process variables.
This data-driven, AI-enabled approach offers a novel and more efficient way to obtain accurate readings throughout the entire processing chain without requiring costly hardware installations. By optimizing process control, it enhances efficiency and reduces waste.
Several pharmaceutical manufacturers have already implemented these methods, integrating an understanding of the underlying chemical, physical, and biological transformations occurring in the manufacturing process with AI-driven techniques (9).
- Blockchain Technology
Blockchain is seen as a key driver in improving drug safety, reducing counterfeiting and fraud, enhancing supply chain efficiency, and ensuring regulatory compliance. It relies on veracity, transparency, independence, and security to ensure certified, publicly accessible, and cryptographically protected transactions (2).
Employing blockchain to store data collected from sensors on IoT devices serves multiple purposes, such as facilitating more efficient real-time decision-making and enabling the creation of predictive models based on environmental hazards encountered throughout the cold chain cycle. These models reinforce the pharmaceutical cold chain by assessing and mitigating potential risks even before they arise (12).
- Trend detection
As part of the digital toolbox, AI plays a crucial role in identifying and analyzing clusters of problem areas, facilitating their prioritization for continuous improvement (9).
One of AI’s significant advantages lies in its ability to pinpoint trends associated with manufacturing deviations, fostering a comprehensive understanding of the underlying root causes. For instance, AI models and expert systems can predict optimal values for complex variables under investigation to optimize formulations or processes (9).
Digital tools are key players in scrutinizing deviation reports, enabling more accurate and efficient data analysis , even when extensive textual content is involved. Consequently, digital tools allow businesses to proactively adapt their strategies and stay ahead of the competition (13,14).
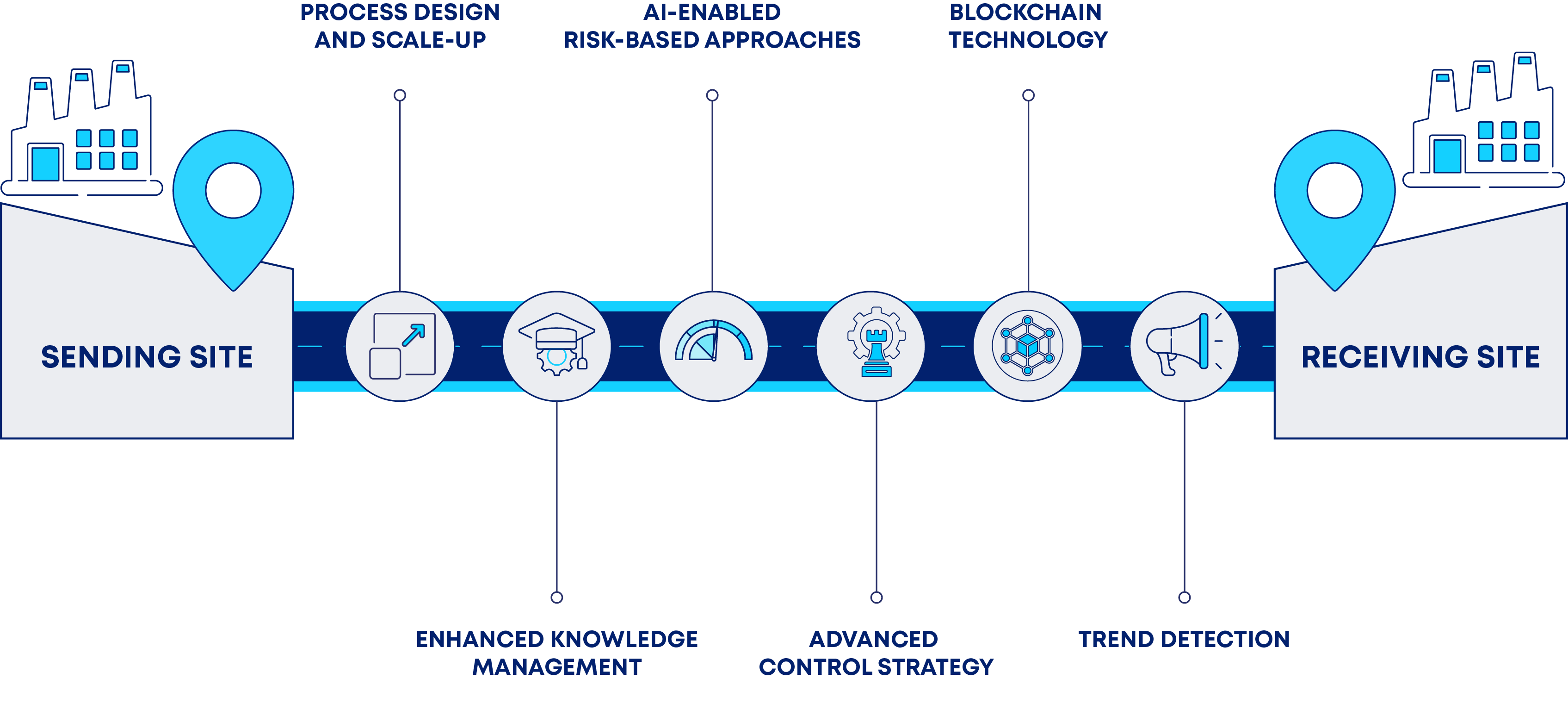
Key Considerations for Application of Digital Tools in the Technology Transfer Process
Major players in the life sciences and pharmaceutical industries have begun investing in and dedicating resources to incorporating digital tools, AI, and ML algorithms into their initiatives. However, reaching the highest levels of manufacturing performance and quality requires a paradigm shift in mindset, significant investment in new technologies and infrastructure, in-demand skills within the organization, adoption of specialized IT frameworks integrated with legacy systems, and the development of innovative corporate strategies (2,15).
With the potential to reduce costs, drive innovation in treatments, and enhance patient outcomes, digital tools represent the future of the pharmaceutical industry, and their implementation is already feasible.
Those who initiate their digital transformation journey now will gain a competitive edge, as standards, strategies, use cases, and ecosystems are still evolving. However, while new technologies offer promising prospects, prioritizing user experience during implementation is crucial.
In regulated sectors, such as drug development, manufacturing, and distribution, every digital data point undergoes auditing by various regulatory bodies, presenting a significant challenge. Therefore, use cases must be meticulously defined, verified, validated, and completely transparent (2).
Here are three initial steps to embark on digital transformation:
- Identify and empower advocates within your organization for digital transformation to explore potential applications and foster enthusiasm across teams.
- Cultivate relationships within the emerging digital toolbox ecosystem by establishing partnerships with like-minded research labs, academic institutions, technology providers, application developers, and startups.
- Prioritize use cases for small-scale Proof of Value (PoV) investments based on their potential to deliver value through business and process insights. When prioritizing, consider therapeutic focus areas, business strategy, customer value propositions, and future growth plans. Continuously monitor the performance of these PoV initiatives and scale up those that demonstrate effectiveness.
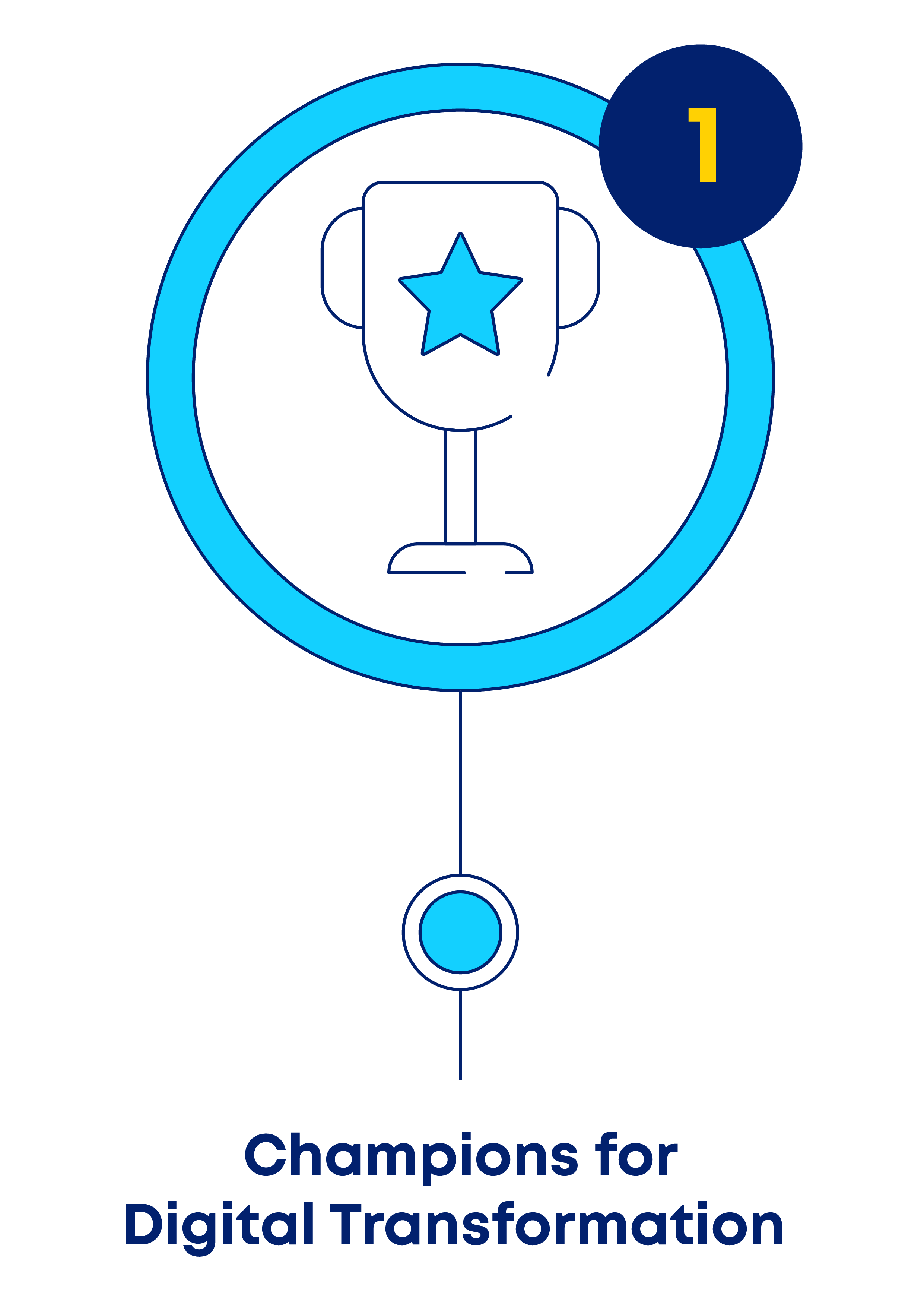

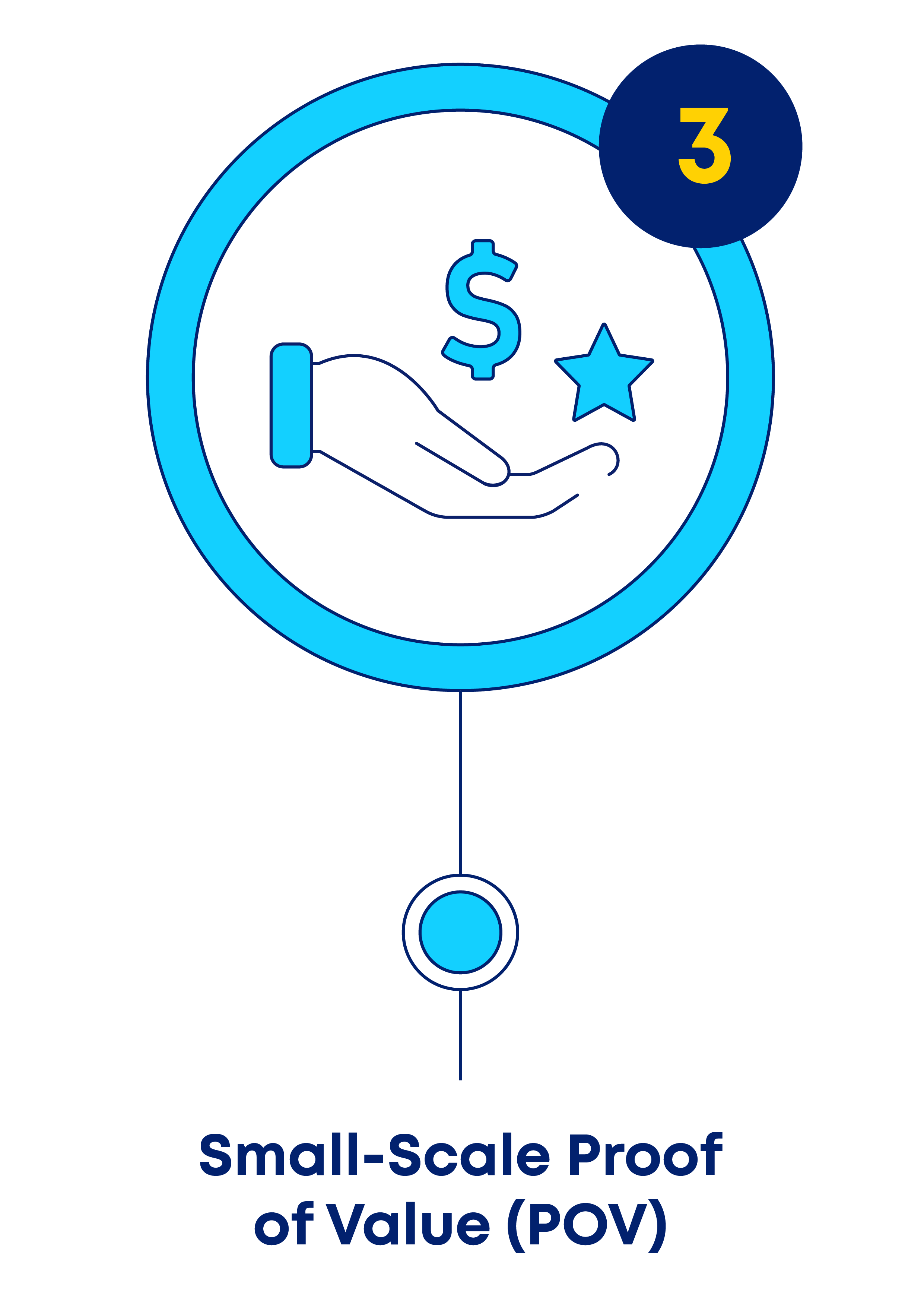
The shift to a Pharma 4.0 operating model within your organization’s digital strategy is paramount. Moving forward, every business opportunity should be evaluated through an analytics-driven lens. Embracing this cultural and mindset shift will cultivate a data-driven organization capable of swiftly recognizing, validating, and capitalizing on opportunities (15).
Main Takeaways and Final Remarks
The integration of digital toolboxes in technology transfer processes within the Pharma 4.0 initiative enables automated digitalization and validation, ensuring compliance with ICH Q10 PQS guidelines. This comprehensive approach leverages knowledge and quality risk management to reduce risk levels and time to market while improving quality standards. By promoting interconnectivity and breaking down silos, it allows for better management of complex supply chain challenges.
Pharma 4.0 optimizes manufacturing by eliminating inefficient production loops through streamlined digital workflows. Additionally, the Pharma 4.0 paradigm ensures data integrity and high-level production quality while reducing manufacturing costs. Furthermore, digital toolbox functionalities increase GMP application through predictive analytics, bottleneck elimination, and smarter maintenance strategies.
Finally, digitally centered initiatives lead to better decision-making and improved overall performance. By closely monitoring the manufacturing process, these initiatives reduce everyday stress and uncertainty, increasing stakeholder engagement and ultimately fostering innovative thinking (15).
References
- Innopharma technology [Internet]. [cited 2024 May 23]. To Industry 4.0 and Beyond. Available from: https://www.innopharmatechnology.com/news/to-industry-4.0-and-beyond
- Boel J. DBL Group. 2023 [cited 2024 May 23]. Pharma 4.0: The Future of Pharmaceutical Manufacturing. Available from: https://qbdgroup.com/en/blog/pharma-4-0-the-future-of-pharmaceutical-manufacturing/
- Bridge Automation [Internet]. 2023 [cited 2024 May 23]. Pharma 4.0: How AI and ML are changing the landscape of the biopharmaceutical industry. Available from: https://www.linkedin.com/pulse/pharma-40-how-ai-ml-changing-landscape-biopharmaceutical/
- Heesakkers H, Schmitz S, Kuchenbrod U, Wölbeling C, Zimmer T. ISPE . [cited 2024 May 23]. The ISPE Pharma 4.0 Operating Model’s - Pharma-Specific Maturity Index. Available from: https://ispe.org/pharmaceutical-engineering/may-june-2019/ispe-pharma-40tm-operating-models-pharma-specific-maturity
- The History Of Pharmaceutical Manufacturing: Industry 1.0 to Pharma 4.0 [Internet]. [cited 2024 May 23]. Available from: golighthouse.com/en/knowledge-center/industry-1-pharma-4
- Kidwai A. Polestar. 2021 [cited 2024 May 24]. The Nine Pillars Of Industry 40: Technological Advancements. Available from: https://www.polestarllp.com/blog/what-is-industry-40-and-its-nine-technology-pillars
- Mack J, Lovett D, Mercer E, McEwan M. Pharma 4.0-A Vendor’s Perspective.
- ISPE GAMP® 5: A Risk-Based Approach to Compliant GxP Computerized Systems (Second Edition). 2022.
- Dashpute S V, Pansare JJ, Deore YK, Pansare MJ, Sonawane PJ, Jadhav SP, et al. Artificial Intelligence and Machine Learning in the Pharmaceutical Industry INTRODUCTION. IJPPR [Internet]. 2023 [cited 2024 May 27];28(2):111–31. Available from: https://www.researchgate.net/publication/374914821_Artificial_Intelligence_and_Machine_Learning_in_the_Pharmaceutical_Industry_INTRODUCTION
- Korber [Internet]. [cited 2024 May 27]. How data management and analytics ensure asuccessful tech transfer. Available from: https://www.koerber-pharma.com/en/blog/how-data-management-and-analytics-ensure-a-successful-tech-transfer
- Haddad G. Revolutionizing QRM: The Impact of AI and ML. 2024.
- Misra S. LinkedIn. 2021 [cited 2024 May 27]. AI in Pharma: Emerging Use Cases Across the Value Chain. Available from: linkedin.com/pulse/ai-pharma-emerging-use-cases-across-value-chain-sachin-misra
- Silvertown A. LinkedIn. 2023 [cited 2024 May 27]. Artifical Intelligence in Retail Pharmacy: The Impact and Potential of AI. Available from: linkedin.com/pulse/artifical-intelligence-retail-pharmacy-impact-ai-adam-silvertown-6vqic
- Akmal A, Binti Y, Jayus M. LinkedIn. 2023 [cited 2024 May 27]. The Role of Artificial Intelligence (AI) in Tech Commercialization: Powering the Future of Innovation. Available from: https://www.linkedin.com/pulse/role-artificial-intelligence-ai-tech-powering-future-innovation/
- VimaChem [Internet]. [cited 2024 May 23]. Pharma 4.0 - A practical guide for a successful digital transition. Available from: https://www.vimachem.com/resources/pharma-4-0/