A View on the Revised Annex 1 Requirements on Visual Inspection Processes
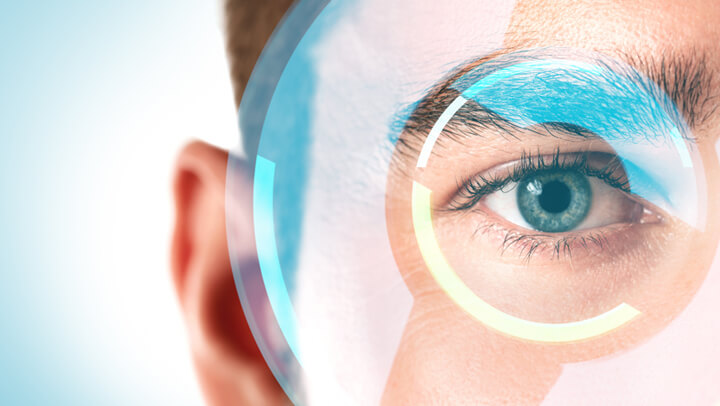
The revised EU GMP Annex 1: Manufacture of Sterile Medicinal Products provides needed details applicable to visual inspection processes while generally aligning with other compendial guidance addressing visual inspection.
The Revision of Annex 1
The BioPhorum visual inspection team has considered the impact of the requirements in the revised Annex 1. However, one paragraph in section 8.32 could lead to confusion and even negatively impact product quality. With this article, we want to review and assess the background of this statement, highlight benefits and potential risks, and propose a harmonized interpretation across the pharmaceutical industry.
In the previous version of Annex 1, paragraph 124 provided guidance for the regular challenge of equipment used in inspection methods alternative to manual inspection, stating, “Filled containers of parenteral products should be inspected individually for extraneous contamination or other defects. When inspection is done visually, it should be done under suitable and controlled conditions of illumination and background. Operators doing the inspection should pass regular eye-sight checks, with spectacles if worn, and be allowed frequent breaks from inspection. Where other methods of inspection are used, the process should be validated, and the performance of the equipment checked at intervals. Results should be recorded.”
For automated inspection, the requirement to check equipment performance at intervals was interpreted as requiring both challenge sets or standards to be run at the beginning of each batch or the beginning and end of the batch and periodic requalification to demonstrate performance. The updated paragraph 8.32 of the revised Annex 1 says, “Where automated methods of inspection are used, the process should be validated to detect known defects (which may impact product quality or safety) and be equal to, or better than, manual inspection methods. The performance of the equipment should be challenged using representative defects prior to start up and at regular intervals throughout the batch.” The final sentence of this paragraph could be interpreted as suggesting the introduction of breaks during batch processing to conduct performance checks, which we think needs further exploration.
The requirement for a functional check at the beginning of the batch serves a specific purpose. By performing a check prior to start up, one can ensure the following:
- The machine functions correctly, inspecting product for presence of pre-programmed defects, identifying those defects, and effectively rejecting them.
- The appropriate machine recipe is loaded, and everything is set up so the inspection process of the batch can be initiated confidently.
The statement in the revised Annex 1 continues by asking for the same challenge tests to be repeated at regular intervals throughout the batch. Specific details about how frequently the inspection should be repeated and why the repetition is required are missing. It does specify, though, that those challenge checks should be performed in a manner representative of the batch, by asking for the checks to be performed “throughout the batch.” The question we have been asking is what purpose could this serve?
We interpret this statement as requiring close monitoring of machine performance to ensure consistent functionality and reliable inspection results, but we feel that re-running challenge tests during batch manufacture is associated with risks.
Automated inspection function tests are designed to confirm machine functionality by accepting conforming products and rejecting non-conforming or defective units. To conduct this functionality check, challenge sets are designed to mimic individual units, representing the real product but incorporating known example defects. These sets need to be carefully controlled when used to check automated visual inspection before the start of a batch to avoid possible mix-up of the set with the final product. Therefore, thorough line clearance and reconciliation of the challenge set prior to starting manufacture is considered essential to prevent unintended mix-ups.
PDA Who's Who
The authors are part of the BioPhorum Visual Inspection collaboration team. The team meets to discuss topics that impact the operational aspects of visual inspection and influence its future direction.
The following subject-matter experts contributed to the development of this opinion article:
- Heidi Fronheiser, Sanofi
- Karishma Gupta, Bayer
- Rafi Mohammad, Bayer
- Valerie Rautureau, Eli Lilly
- Christopher Barnes, Eli Lilly
- Mitsutaka Shirasaki, Roche/Genentech Inc.
- Deborah Hill, BioPhorum
Using this approach to perform additional function checks at multiple intervals during the inspection of a batch might lead to an increased quality risk to the batch due to the increased possibility of mix-up. Additionally, it can impact the patient's timely availability of the final drug product. Assuming the automated inspection machine operates as expected (without stops) when hitting the time point for a regular interval check, the machine would need to be stopped, the line should be cleared of the product, and reconciliation should be performed; only then can the challenge set be introduced and run through the machine to perform the necessary function check. Upon completion of the check, the line must be cleared, and the challenge set needs to be reconciled again. Then, the final product can be re-introduced, and inspection can continue with an additional reconciliation on completion of the batch. While this is all performed under well-controlled conditions and procedures, it is still a manual process. At a potentially high frequency, it could lead to unintended mix-ups between the final product and the challenge set.
Alternative Options?
Performing the functional check before starting batch manufacture confirms the correct machine set-up for the production batch, correct recipe selection, and correct components. In addition, performing the functional check ensures that key parts of the system, like cameras and outfeed gates, are operating as expected. After this initial set-up and during the batch inspection process, automated visual inspection systems continuously self-monitor the critical parameters for the inspection process and will generate an alarm if an issue is detected or if critical parameters, light intensity, camera position, drift out of specification. The continuous system monitoring during operation provides assurance that the functionality demonstrated and challenged at the start of the batch can be assured throughout the batch without the need to stop batch inspection to challenge the automated inspection system with challenge sets.
However, there are occasions where re-running a challenge set during a production batch is appropriate, and the potential benefit of challenges in these situations justifies the risk associated with introducing the challenge set. Procedures should be in place to re-run standards in response to machine failures, unplanned maintenance, and unexpected or prolonged automated visual inspection equipment downtime. In the same way that performing the challenge prior to the batch confirms that the correct recipe was selected and that cameras and other systems are operating as expected, there is technical value in confirming the operation of the equipment after any unplanned event.
We believe that a challenge test should always be performed at the start of each batch and that each manufacturing site should develop an appropriate rationale for challenge testing, which considers batch sizes, manufacturing frequencies, and the impact of atypical situations, and this should define which events should trigger challenging the automated inspection machine during batch inspection. Rather than interpreting the regular intervals to be time-based (e.g., every hour), we consider the requirement described in the updated paragraph 8.32 of the revised Annex 1 for regular monitoring should be driven by specific events, which would be a more appropriate and useful approach.
Conclusion
It is not our intent to create alternative wording or prescribe what everyone should do. Still, it is important to highlight the risks associated with the interpretation of the revised wording. We believe that if the wording's intention leads to stopping batch manufacture from running standards, this will add more risk than it removes and will not ensure the consistency we feel the wording is intended to bring about.