Annex 1 to VPHP: The ABCs of Aseptic Processing
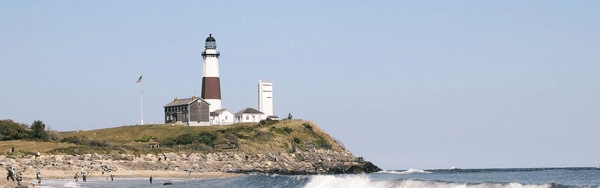
Technological changes are coming to aseptic processing, as acknowledged by regulators and reflected in the recent draft Annex 1 revision. What are some of the latest trends in this area? How can pharma prepare?
Three speakers offered their thoughts on the latest developments in aseptic processing at the PDA New England Chapter dinner meeting, held in Lenox, Mass. on Nov 3. Former PDA Chair Hal Baseman explained how the proposed draft Annex 1 revision will impact aseptic processing technology. Samantha Kay looked at validation of vapor phase hydrogen peroxide (VPHP or VHP) decontamination. Shawn Kinney concluded the talks with a look at the latest in isolator technology.
Annex 1 represents the first new discussion on aseptic processing in a while, Baseman explained in his presentation. The document contains 43 recommendations for risk-based approaches to sterile product manufacturing and control and sets an expectation for the use of quality risk management (QRM) principles. Why is this important? Well, if regulators expect industry to use QRM to justify submissions, then it would follow that QRM could be used to justify new regulations.
The second part of Baseman’s presentation focused on current industry trends. He exclaimed that the rate of change is not fast enough! We are entering an unprecedented era with new therapies; competing demands of affordability, sustainability and public safety; improved manufacturing reliability; and new technology resources such as artificial intelligence and big data.
Baseman outlined key trends affecting our industry:
- Transition from manufacturing processes that are batch-driven, single-shift, intervention-laden, personnel-dependent and environment-constrained to those that are continuous, automated, small-closed-environment, data-driven, data-controlled and standardized.
- Transition from approaches to control that are corrective and reactive to those that are risk-based and preventative.
- Transition to more objective sterility assurance based on data.
- Transition to greater transparency and exchange of ideas across the industry.
- Transition to increased cooperation among manufacturers, suppliers and regulators.
Following Baseman’s presentation, Kay covered VPHP decontamination—a decontamination method growing in popularity. VPHP is a surface biocide requiring contact for successful decontamination. Lack of contact results in inefficient decontamination, a major concern within the industry. Since spore dispersion can be affected by material topography (roughness, grooves, or cavities), one method to predict material compatibility is to inoculate material with 106 Geobacillus stearothermophilus spores and then analyze with a scanning electron microscope.
The following concerns, however, should be heeded with VPHP:
- Some substrates show poor spore dispersion and should be avoided
- Hydrogen peroxide (H2O2) contact may produce deterioration of elasticity, strength or flexibility of different materials
- H2O2 may be absorbed by the package material or contents.
- Kay presented a series of case studies to show how these challenges may be overcome.
Rounding out the discussions, Kinney’s presentation debunked five myths regarding isolator technology. First, isolator systems are not more expensive than cleanrooms. Since only a grade D background is required for operator areas, there is no need for sterile gowning. This lowers the cost of quality greatly due to reduced excursions, deviations, and monitoring of personnel and the environment. Second, VHP’s effect on product is miniscule as no primary containers are exposed to VHP and thorough aeration to 1 ppm VHP or lower is achieved before product exposure. Third, cycle times are not longer. Current cycle times are one to four hours with greater than 6-log reduction of microbes, which is essentially sterile. Fourth, validation is not more difficult. Kinney’s company has successfully validated isolators from three different manufacturers, demonstrating that 650-760 ppm for approximately 30 minutes achieves 6-log reduction of Geobacillus spores.
Fifth and finally, Kinney showed how isolator systems can be flexible. His company has implemented two filling lines: a manual line that uses an isolator and a dual-chamber, restricted-access barrier system (RABS) for filling vials, syringes and cartridges up to 5,000 units each and a semi-automated line which integrates four isolators, three RABS, a depyrogenation oven, a capper and a lyophilizer. Kinney demonstrated that flexibility can be designed into an isolator by manufacturers who cooperate to fabricate and integrate their equipment into the isolator.
All in all, it was a successful event. Before the talks even began, the 58 attendees had the option of touring Berkshire Sterile Manufacturing’s facility. The event concluded with a surprise birthday cake for Kinney, in honor of his special day.
The chapter thanks the three speakers and meeting host Henry Brush along with all the sponsors for making this event possible.
PDA Who's Who
- Hal Baseman, COO, ValSource
- Henry Brush, Vice President, CMC Strategy and Operations, Selecta Biosciences, and Chapter Member-at-Large
- Samantha Kay, Microbiologist, Fedegari Technologies
- Shawn Kinney, PhD, CEO, Berkshire Sterile Manufacturing