Big Data is Here to Stay
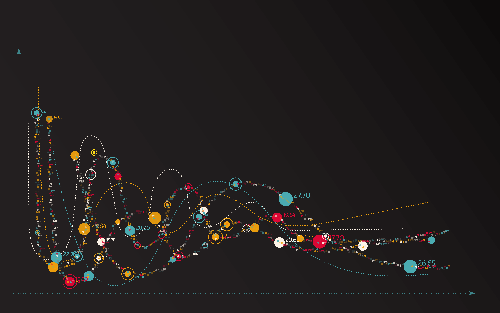
2018 PDA Manufacturing Intelligence Workshop Commands a Crowd
Implementing big data within pharmaceutical manufacturing will require extensive collaboration. Fortunately, a 2018 PDA workshop suggests this is possible.
Last March, the 2018 PDA Manufacturing Intelligence Workshop explored efforts to advance the use of big data in manufacturing and supply chain management. Approximately, 100 participants attended this workshop, which immediately followed the conclusion of the 2018 PDA Annual Meeting.
PDA’s Manufacturing Intelligence Task Force helped coordinate the 2018 PDA Manufacturing Intelligence Workshop.
This task force falls under the PDA Manufacturing Science and Operations ProgramSM (MSOP).
The workshop provided thought-provoking keynote speakers from Amgen, Siemens, Disney and Biogen, introduced some background information on big data and reviewed the goals of PDA’s big data task force. Breakout sessions focused on three areas: the Manufacturing Information Model (MIM), big data analytics for process robustness and challenges to implementing big data in a regulated industry. Each of these three sessions included group activities to help PDA’s Manufacturing Intelligence Task Force develop strategies to grow big data knowledge within parenteral manufacturing.
Manufacturing Information Model
In this track, participants acknowledged that the move to Industry 4.0 requires managing large amounts of manufacturing data, confirming the need for this body of work as a backbone of PDA’s Manufacturing Intelligence Task Force.
A standard, open-source MIM will allow the industry to make manufacturing data findable, accessible, interoperable and reusable over extended periods of time and throughout the organization.
Standard open-source information models have been developed in many industries, such as the construction and process industries. In the pharma industry, the Allotrope Foundation develops data standards for scientific laboratory data.
The Manufacturing Intelligence Task Force has identified the need for an MIM for pharmaceutical manufacturers similar to other industries’ information models. Such an MIM would provide a standard information architecture for manufacturing data. It would use standard terminology and be productagnostic. An MIM enables insights to be drawn across multiple locations (internal and external suppliers) and provides faster insights from manufacturing data.
Brainstorming during the session resulted in a robust list of business use cases where an MIM would bring value. Participants agreed that increased process understanding leads to process robustness and greater yield, stability and reduction in cycle time.
This track also highlighted the challenges of implementing an MIM that included data challenges—enabling context for historical data, ownership and governance, common data definitions and sponsorship and validation.
Potential next steps identified included communication of "data lake" best practices along with alignment on a fit-for-purpose validation approach.
Big Data and Process Robustness
In this track, 25 participants from various pharmaceutical companies, consulting firms and technology firms focused on what process data to compile, which process data can be used, and how process data should be used for monitoring and improvements. The session consisted of a case study and group exercise followed by discussion.
A case study on the evolution of a large molecule process monitoring program was presented. Merck has adopted the Pipeline Pilot software to analyze large-scale manufacturing data and report real-time process performance across its network and product portfolio.
As a group exercise, participants identified and collected the process robustness parameters from each of the unit operations within a typical biopharmaceutical drug substance and drug product manufacturing process. The group universally agreed on the need to gather and analyze all the data to improve process understanding and robustness. Yet participants expressed a concern that there remains lack of a clear understanding on how global regulatory agencies consider the use of big data for continuous improvement.
The track concluded with the consensus that industry needs to continue to gain a better understanding of the challenges of using big data to enable process robustness. All agreed that a position paper providing case studies and best practices in process robustness improvement for the industry would be a valuable document.
Big Data Meets Regulated Industry
When it comes to Industry 4.0 in a regulated environment, how should companies respond? In the third breakout session, participants reviewed the collective obstacles facing pharma in the new Industry 4.0 paradigm. These include lack of robust data governance, data lifecycle challenges and associated regulatory expectations.
The track then delved more deeply into Industry 4.0 concepts with a use case on applying data analytics in biomanufacturing. Key takeaways from the discussion included:
- Decision-making should be married to the data
- If the data paradigm shifts, the quality paradigm must shift as well
- Industry should look to experience from process and product monitoring to serve as examples
The track concluded with a lively debate on whether a data lake needs to be validated. Participants brought multiple views from the areas of manufacturing, business, IT and quality, such as, the data lifecycle needs to be clarified, and there is no one-size-fits-all solution when it comes to the validation approach, as it depends on use of that data. Clarity is needed on roles (balancing control and ownership in the most efficient way). And there is a lack of common practice when GMP and non-GMP data is mixed.
[Editor's Note: Learn more about big data in an “On the Issue” video featuring coauthor Aaron Goerke.]
Following these interactive breakout sessions, the remainder of the workshop involved participants regrouping to reflect on what they learned from the earlier sessions. This led to a discussion on what additional opportunities exist in the manufacturing intelligence space that are not currently being explored by the PDA task force.
Potential use cases for the application of modern data techniques were also presented. Afterward, attendees were split into ten groups to select one of ten areas in need of deeper exploration. Recommendations were collected using online polling software. Each group spent some time identifying the risks and value propositions associated with each opportunity. At the end, each group was asked to rank the ten opportunities based on the following criteria (1= highest priority/10 = lowest priority):
- Relative value in a cross-company workstream (value proposition)
- Desire to have PDA sponsor a workstream in this area
- Personal interest in participating in a cross-company workstream in that topic area
The clear preference, from the results shown in Table 1, was the Predictive Process Monitoring workstream. In addition to the intrinsic value of this opportunity, in post-workshop discussions, it was realized that this workstream could also take advantage of the work being done by the three existing task forces, combining their output in a way that could significantly impact the industry. Synergies with the other workshop breakouts were clear, and the task force plans to align its next steps across the workstreams as a key output.
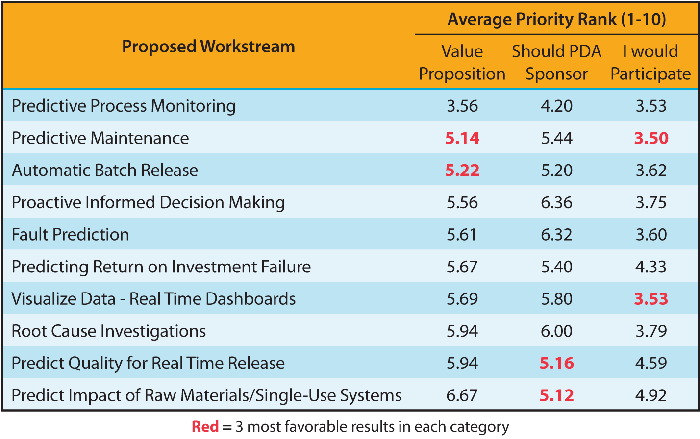
Table 1 Opportunities for a Deeper Dive
In closing, the significant number of participants, their active interest and participation, the robust discussions and identification of specific use cases/outcomes to be further pursued all underscore the timely opportunity presented by the Manufacturing Intelligence Task Force. A roadmap will be published shortly with specific information on where additional team participation is needed most to make this a successful industry-wide collaboration.
Want to help direct the future of manufacturing? PDA’s Manufacturing Intelligence Task Force seeks volunteers from other pharma companies to offer their input. If interested, email PDA’s Volunteer Coordinator.