Breaking point: Assessing and Addressing the Risk of Auto-Injector Failure

While user-centered design may have been pioneered in the computing industry, its impact is equally significant in the pharmaceutical sector, as demonstrated by the widespread success of the auto-injector.
The Rise of Autoinjectors in Patient Care
These devices, in their various forms, are based on a deep understanding of the requirements and preferences of patients who are in need of injectable therapies. By simplifying the act of self-administration, they allow for medical conditions, including chronic illnesses, to be managed with greater autonomy, reducing the dependency on healthcare professionals (HCP) and the requirement to attend clinical facilities.
A range of studies has underlined these benefits, showing that autoinjectors are viewed more favorably than self-injection with a syringe or intravenous administration by HCPs, with patients citing improved convenience, savings in time and reduced pain (1-3).
These patient-friendly foundations, when allied to the meteoric rise in demand for glucagon-like peptide-1 (GLP-1) therapies to treat type 2 diabetes and obesity, are driving forecasts of a 13.6% compound annual growth rate for the autoinjector market in the decade to 2030 (4).
Complex Design Behind Simple Solutions
While autoinjectors deliver on their clear purpose to ease the injection process, their deliberately ergonomic exterior may hide the fact that these complex devices are the product of a finely tuned and highly sophisticated design, manufacturing and assembly process. When such a device ends up in the hands of a patient, a whole host of critical considerations must be understood, addressed and managed for the product to safely deliver the intended dose.
Glass Syringe Integrity: The Heart of Reliability
Of particular note is the glass primary container integrated within the autoinjector mechanism. Sitting at the heart of the device, this pre-filled syringe (PFS) is responsible for maintaining the integrity of the dose during storage and up to the point of administration. When the device is activated, the syringe components must support the full delivery of the intended dose, accommodating the drug product’s particular viscosity and withstanding the increased levels of mechanical stress generated by the device. Failure to manage these variables has the potential to result in breakage of the PFS, which, while relatively rare, is a scenario that clearly has a negative impact on the patient and could even expose them to harm. From a production perspective, evidence of breakages could also lead to interrogation and interruption of manufacturing processes and, at worst, device recalls.
Investigating the Causes of Breakage
Breakages are most likely caused when pre-existing defects in the primary container are exacerbated by the mechanical impact of activation, particularly where there is additional pressure caused by high-viscosity and/or large-volume drug products. This combination can expand existing sub-critical cracks in the container and, ultimately, cause the syringe within the autoinjector device to break.
Motivated to tackle this risk and to limit the potential for autoinjector failure on activation, Stevanato Group designed and implemented a study in 2022 to explore this phenomenon, analyzing the influence of various glass syringe critical attributes on breakage risk. The objective was to clarify and prioritize possible causes and then address them through design and manufacturing improvements, thereby completing the circle by implementing enhancements to the overall functional robustness and reliability of the autoinjector device.
The study was designed to accurately simulate the impulsive stress conditions that are present during the activation of a typical spring-activated autoinjector. This was achieved by creating a bench unit that replicated the action of the driving rod to apply downward force to a pin in contact with the plunger stopper of a pre-filled syringe (see Figure 1). The movement of the driving rod was triggered by a pneumatic piston and controlled by an electro valve and pressure regulator. Internal pressure measurements were recorded by a sensor contained within the syringe sample. In order to present a ‘worst-case scenario,’ the liquid pressure was tested up to a level of 15Mpa (150 bar), which far exceeds typical pressures observed in everyday autoinjector use (see Figure 2).


Three specific variables were analyzed to assess their correlation with device failure using the test setup shown in Figure 3. The first variable was the shoulder design of the syringe, with two versions investigated - one a more squared shoulder profile and the other a more conical profile. Secondly, the syringes were tested with and without the presence of a 3mm air gap between the plunger and the surface of the liquid. Finally, to evaluate the influence of defects on the glass surface, a controlled flaw was introduced to the container at a limited depth that would not necessarily be identified by common typologies of visual inspection equipment.
A total of 30 samples were tested in each of the variable categories. Each syringe incorporated a 1mL long-staked needle filled with 1mL water for injection. Following exposure to the high-pressure load, instances of breakage were recorded on a Pareto Chart, noting the variables present on each occasion. This elicited clear data on the fact that defects on the external surface of the glass syringe were the main root cause of breakage and, therefore, device failure. Indeed, the presence of surface defects alone was observed in 65% of breakages, making it the only variable to exceed the statistical limit of 28.23%. In contrast, the air gap and shoulder design were not found to influence breakage (see Figure 4).
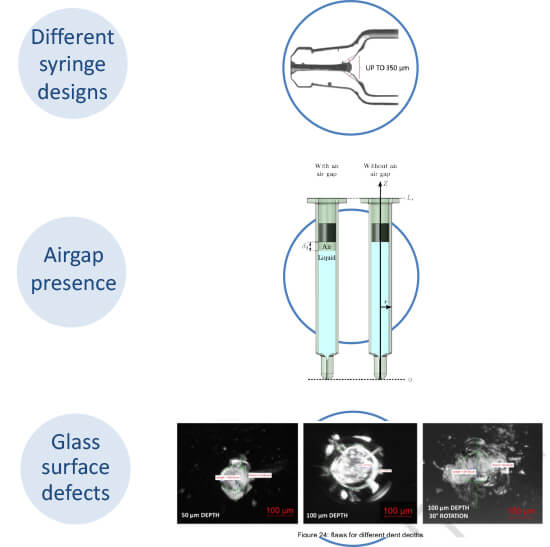
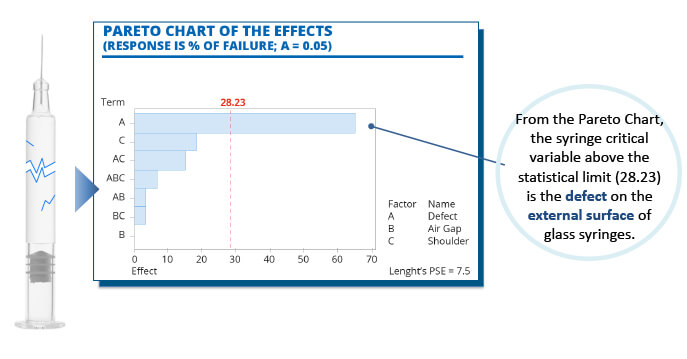
A separate subsequent assessment was also carried out to provide further data on the different shoulder designs, aiming to establish whether any differences in internal pressure were registered for the squared and conical syringe profiles during stress impulse generation. The resulting analysis of the inner pressure data revealed no material difference between the stress generated on the glass for the two designs.
Targeting Defects for Enhanced Reliability
With the finding that microcracks on the glass surface are the major cause of breakage, Stevanato Group’s production specialists were able to initiate strategies to address this issue. Rather than addressing the container’s geometric design, focus was placed on reducing the potential for defects to be introduced within the autoinjector manufacturing process. The approach followed the quality improvement principles of Six Sigma, and the step-by-step process began with the identification of the root causes of flaws before seeking to uncover targeted solutions.
Critical factors confirmed as contributing to the introduction of flaws were glass-to-glass (GTG) and glass-to-metal (GTM) contact, which can be challenging to manage within the forming process. This risk can also become amplified as product demand increases since the drive for higher volumes can result in higher production throughput speeds, requiring more sophisticated handling of containers to avoid damage occurring.
Process Improvements and Results
Having established the requirement to reduce GTG and GTM contact, Stevanato Group’s manufacturing specialists were able to introduce design changes to the forming line to reduce these risks (see Figure 5).
Measures included enhancing forming stations to lower contact forces, upgrading oven syringe holders to avoid GTM contact and softening the pick-and-place function to limit vibrations. In addition, inspection systems were recalibrated to apply greater scrutiny to the integrity of the containers being output by the manufacturing line with the objective of capturing previously hidden flaws.
After implementing the new process measures, Stevanato Group tested the syringes to establish whether the risk of breakage had been reduced. Notably, at standard pressure conditions of 7 bar, no breakage was recorded across 1,280 samples, highlighting the impact of the process changes in enhancing mechanical resistance.
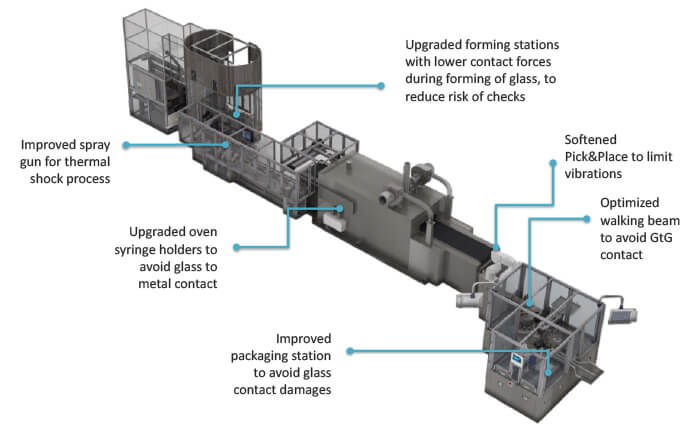
Ensuring Long-Term Device Performance
When transposed to the context of an autoinjector, this proven level of mechanical integrity provides critical assurances of device performance. Even when delivering high-viscosity drug products, reducing micro-defects on the glass container means that stress forces are far less likely to result in breakage. Whether delivering GLP-1 treatments or vaccines, the total cost of ownership is not compromised by sub-quality primary containers presenting a higher failure risk.
Conclusion
Type 1 borosilicate glass containers remain the global standard for their exceptional material properties. However, addressing surface integrity issues is critical to ensuring the reliability of glass syringes under the mechanical stresses of auto-injector activation. Process enhancements, such as improved forming stations, softer handling mechanisms and recalibrated inspections, have successfully mitigated these risks, enabling consistent device performance even with high-viscosity drugs. These advancements deliver a safer, more convenient and effective solution for patients. Furthermore, fostering strong collaborations with syringe suppliers is pivotal for enhancing auto-injector reliability. By integrating device and packaging considerations early in the design phase, these partnerships can help accelerate time-to-market while optimizing overall product performance.
References
- https://link.springer.com/article/10.1007/s40271-017-0276-
- https://www.ncbi.nlm.nih.gov/pmc/articles/PMC3931638/
- https://www.dovepress.com/preference-for-a-prefilled-syringe-or-an-auto-injection-device-for-del-peer-reviewed-fulltext-article-PPA
- Autoinjectors Market Size, Share & Trends [2030] (marketsandmarkets.com)