How Ergonomics & Cleaning Reduce Injuries, Contamination in Micro QC Workflows

The repetitive nature of routine laboratory work puts pharmaceutical technicians and scientists at risk for repetitive strain injuries (RSI). Routine activities often include reoccurrence of the same movements over and over, which can take a toll on hands, wrists and shoulders and, ultimately, can lead to serious damage. According to the Occupational Safety and Health Administration (OSHA), RSI in the workplace has resulted in over 300,000 cases as far back as 2015 (1).
RSI is closely related to the ergonomics of operating instrumentation in conducting simple but repetitive laboratory processes (2). According to an article by certified ergonomist Kevin Costello on common disorders of laboratory workers, musculoskeletal movements involving repetition, contact stress, force and awkward posture are the riskiest.
RSI can lead to laboratory-user fatigue and variability that causes poor technique, errors and cross-contamination. The result is retesting that can add up to 14 days for procedures such as quality-control testing. In addition, the societal costs of carpal tunnel syndrome, a key result of RSI, have been estimated at $30,000 per case. This figure does not include indirect costs in lost productivity and quality of life issues that extend to everyday activities (3).
Microbial cross-contamination also can result when laboratory filtration devices, such as manifolds, filter funnels and pumps, are difficult to clean.
Fortunately, there are new filtration designs that are considerably more ergonomic and easier to clean than conventional products.
Reducing RSI: The Secret Is in Product Design
In a pharmaceutical microbiology laboratory, there are many ways to avoid manual-labor stress by working in a more ergonomic manner. Choosing the right tools can make all the difference. Filter funnels are a more efficient option for microbial contamination and quality-control testing, with the funnel and membrane in a ready-to-use, disposable system. The membrane is contained within the funnel for filtration, limiting handling and transfer, which reduces repetitive laboratory motions.
On most of these devices, the funnel top is removed by twisting or other motions that can put stress on wrists and arms. Additionally, twisting the top of the funnel can often tear the delicate membranes beneath, resulting in the need for retesting. When using a filter funnel, the top is removed with a simple squeeze of its sides. Then, the user can easily access the membrane. (Figures 1a, 1b)
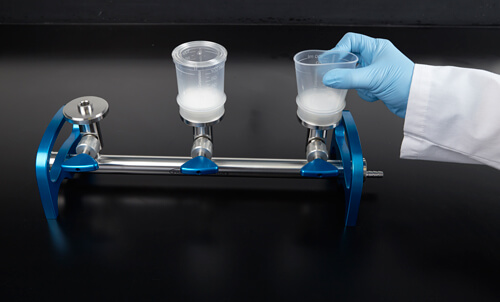
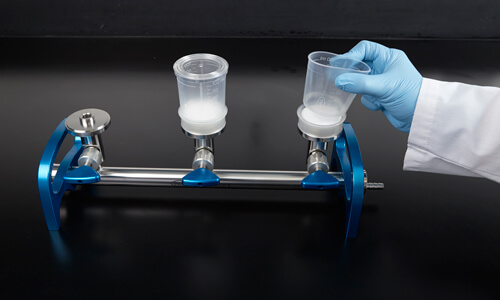
Another step forward in reducing RSI is a newly designed laboratory manifold. (Figure 2)
Manifolds with few parts, no required tools and simple friction fittings can be found for easy disassembly and reassembly. This simplified design can save precious time and reduce RSI risk. (Figure 3)

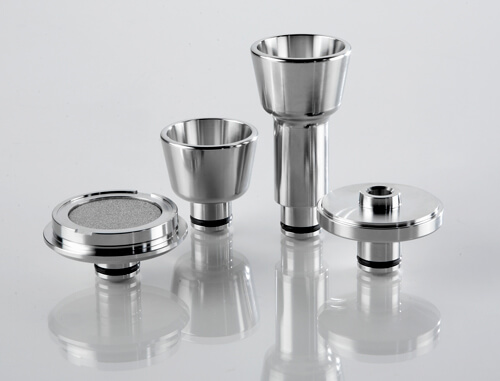
Additionally, since the manifold end cap and hose barb can be set up in either orientation, all the valves are situated at the front of the device. This means there is no need to reach over the top of a filter funnel and maneuver behind a manifold to turn the valves on and off. Both features improve contamination prevention and reduce injury risk. (Figure 4)
Finally, selecting a laboratory manifold with a modular format can be beneficial. It enables processing of up to six samples at one time when two manifolds are connected with a coupling device. Over time, this design can result in less handling and a lower risk of RSI. (Figure 5)
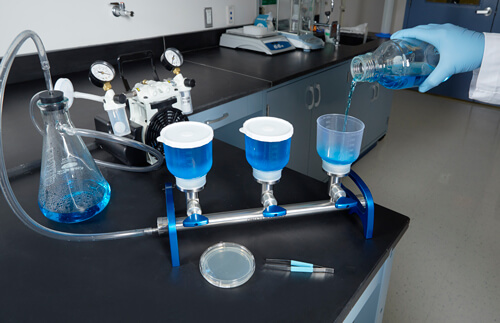
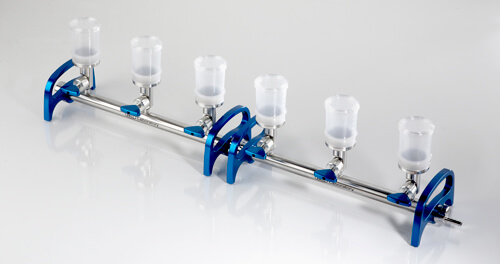
Reducing RSI: Improving Laboratory Techniques
RSI can be further reduced when technicians are well-trained in techniques such as the use of forceps and handling membranes. Proper orientation and handling of forceps is not only important to the technician’s health, but also crucial for good microbial growth.
The figures below show the differences in techniques. In Figure 6a, the hand is in an awkward position, which can cause pain during membrane removal. In Figure 6b, the forceps are held properly, giving the hand more freedom and a more natural and comfortable feel.
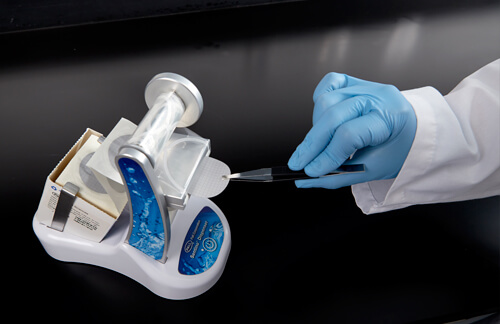
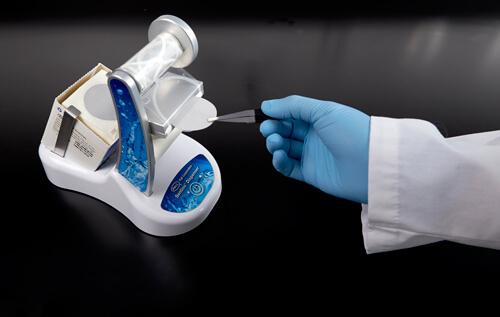
In Figure 7a, the plating technique in the left image is not only awkward, but also increases the risk of creating bubbles on the bottom of the filter membrane. Air bubbles are a concern because when the agar media does not properly touch the membrane, nutrients do not reach the membrane as expected. This can cause improper cell growth that can result in false negatives. Proper technique is demonstrated in Figure 7b.
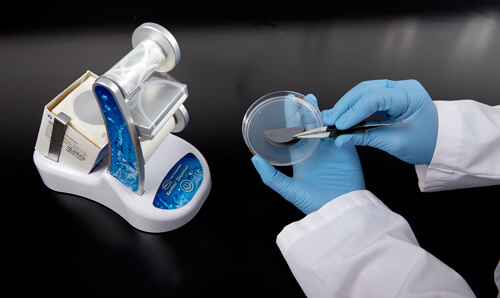
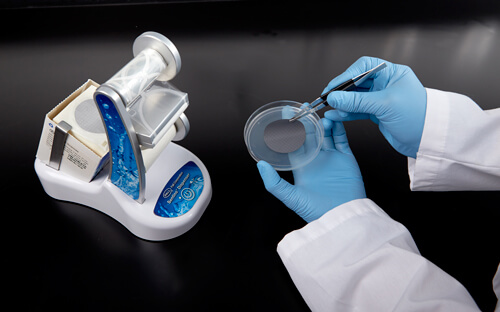
Cleanliness: The Key to Eliminating Cross-Contamination
The cleanliness of the laboratory equipment is the key to eliminating cross-contamination and the resulting delays caused by retesting. Employing manifolds and pumps with easy-to-clean or disposable designs will result in contamination-free devices—a welcome advantage when cleaning is required at least once daily in higher-throughput labs.
Laboratory manifolds offer microbes welcome places to hide. Stainless steel devices with few pieces to disassemble and assemble are a better choice. Their fluid paths should be free of O-rings, and lowered hose outlets will eliminate the back-burping that can require expensive and time-consuming retesting. The manifold should be designed to easily fit in laboratory autoclaves by separating into manageable components.
When purchasing a new microbiology pump, it should have a disposable fluid path that requires no cleaning or disinfection. A disposable pump fluid path, combined with a gamma-irradiated filter funnel option, virtually eliminates the risk of cross-contamination from test equipment.
Disposable filter funnels have a second overpack layer that streamlines cleanroom or hood entry with one wipe-down for multiple, individually packed funnels. The overpack layer reduces gross particulate contamination that can come from cardboard.
Conclusion
When choosing the microbiology filtration to best suit pharmaceutical laboratory needs, the potential for RSI and ease of cleaning are often overlooked. Selecting high-performance products with ergonomics that reduce the risk of long-term injury is very important. The goal is to eliminate the user-fatigue and variability that lead to poor technique, errors and retesting. Reducing microbial cross-contamination and subsequent retesting will save the laboratory time, resources and product development delays.
References
- Nonfatal Occupational Injuries and Illnesses Requiring Days Away from Work, 2015, U.S. Bureau of Labor Statistics News Release, November 10, 2016, https://www.bls.gov/news.release/osh2.nr0.htm.
- Repetitive Strain Injury in the Laboratory – Pipetting Doesn’t Have to Be Painful, Grace Soong, VistaLab Technologies, August 25, 2020, https://vistalab.com/repetitive-strain-injury-in-the-laboratory/.
- Repetitive Strain Injury in the Laboratory, Angelo DePalma, Biocompare, March 29, 2018, https://www.biocompare.com/Bench-Tips/348286-Repetitive-Strain-Injury-in-the-Laboratory/.