Identifying the Right Particle Counter for Your Application
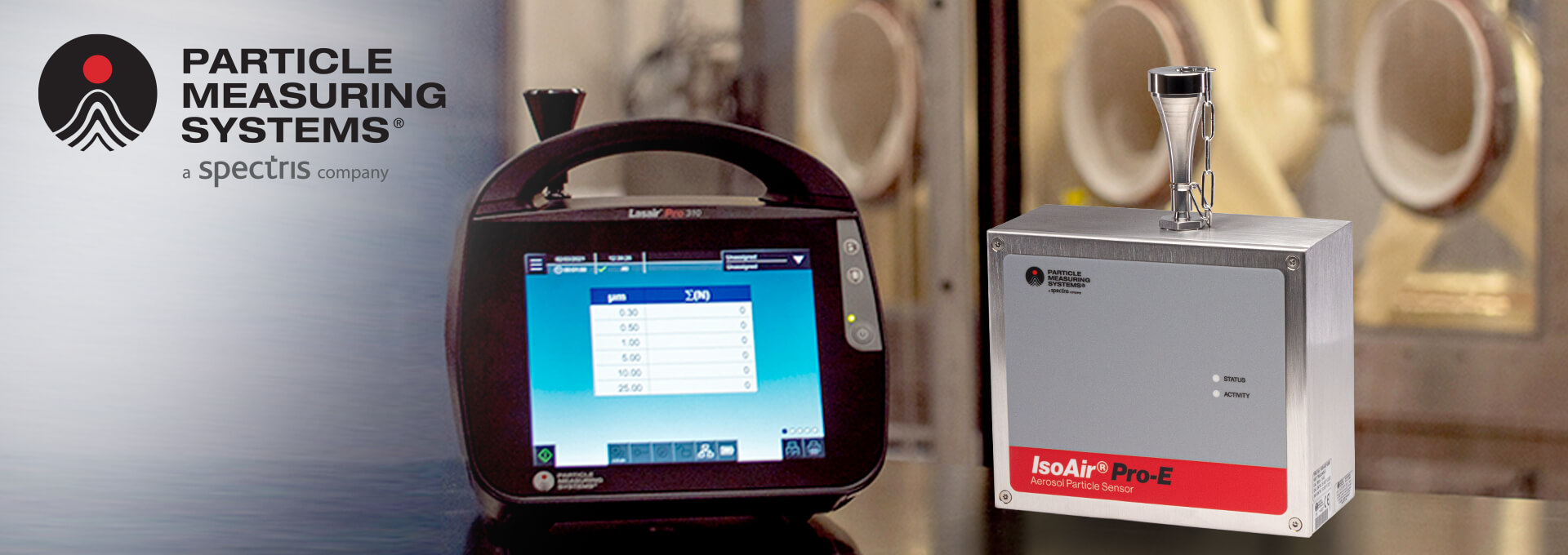
Read below for requirements and solutions for your particle counting application.
Particle Counter Criteria for Classification
The range of particles sizes considered for application in the ISO 14644-1 classification table is: 0.1 µm, 0.2 µm, 0.3 µm, 0.5 µm, 1.0 µm and 5.0µm. However, particles do not exist singularly within these specific size bands, but range at all sizes throughout the considered range (0.1µm to ≥5.0µm), and beyond; there are particles smaller than 0.1µm and greater than 5µm. The understanding of these particles in consideration (classification range) gives a set of data that can be used to determine a level of cleanliness within a specified zone, and the criteria that allows for cleanroom, or clean air devices, to be designed to (filtration efficiency, air flow rate, air exchange rates, occupation, construction materials, etc.) and particle sources.
Within this range there are two primary types of particle counters that can be used to determine cleanroom classification to ISO146441-1:
- Portable Particle counter (e.g.: Lasair Pro)
- Several size channels available within the range required
- Smallest channel (sensitivity) based on application, 0.1µm, 0.3µm or 0.5µm
- Sample flow rate of 1 CFM (1 cubic foot/minute = 28.3 liters/min) or greater
- Mains/battery operated
- Mobile either by hand or cart
- Built in printer
- Local display
- Learn more about the new Lasair Pro
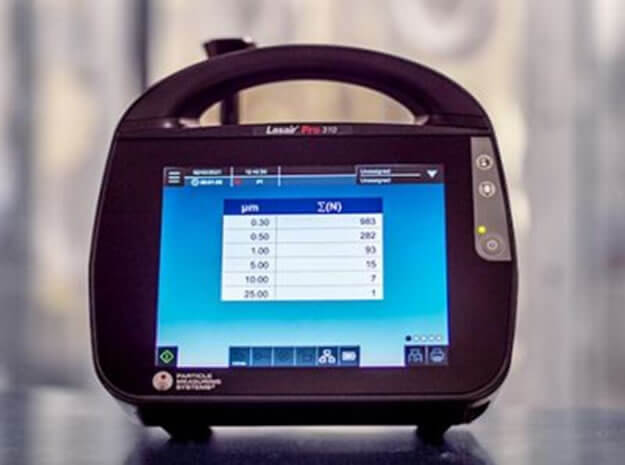
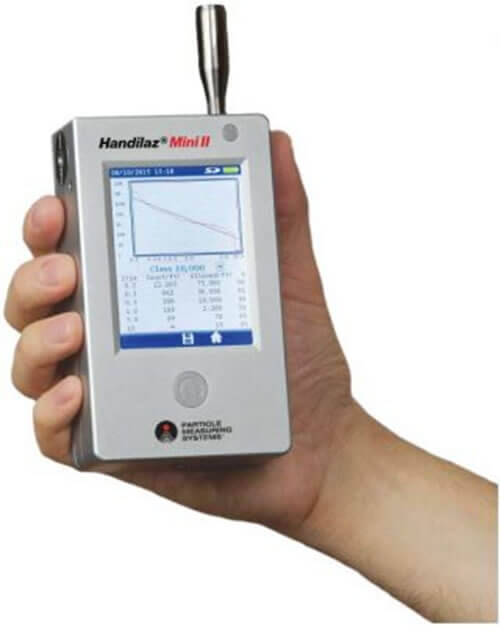
- Hand-held particle counter (e.g.: HandiLaz Mini II)
- Few size channels available within the range required
- Smallest channel based on application, 0.2µm, 0.3µm or 0.5µm
- Low sample flow rate of 0.1 CFM (2.83 liters/min)
- Battery operated
- Lightweight and mobile
- Local display
- Sample volume required for statistical significance
- A minimum number of particles are required to determine a classification state
- Low concentrations of particles require large sample volumes, and/or sequential sampling
- Total test time
- Particle counter sample at a fixed volumetric flow rate
- Minimum sample volumes determine the time required at each location
- Higher flowrates will reduce test duration
- Sample tubing requirements
- There are maximum recommended limitations for tubing used on instruments based on flowrate and sedimentation of particles
The use of either instrument type, for classification is typically a balance between:
Particle Counter Criteria for Process Environmental Monitoring (e.g.: IsoAir Pro E or IsoAir Pro Plus)
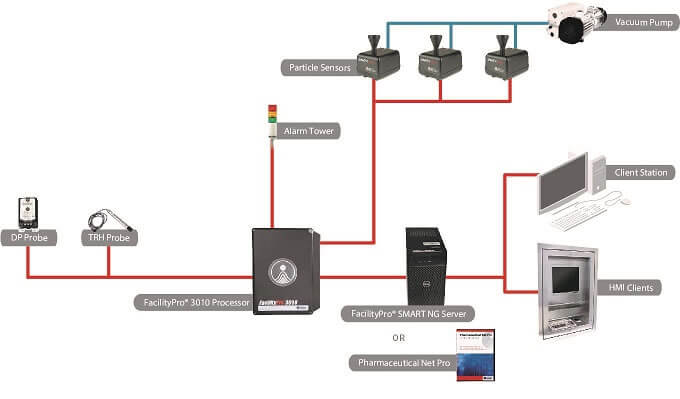
Choice of instrumentation for Monitoring an environment is differentiated from certification, with respect to sample location, as sample points are established and revisited on a frequent interval, based on a Risk Assessment of each location. There are two primary methods for monitoring an environment
- Portable-instrument monitoring
- Insitu-instrument monitoring system
Portable Instrument Monitoring (e.g.: Lasair Pro)
Instrumentation used for portable-instrument monitoring follows similar criteria as that used for room certification, as a series of sample locations require testing on an interval which allows for operators to transit between locations. LSAPC choice for monitoring instrumentation consideration include:
- Particle counter sensitivity – The smallest considered size of particle required to demonstrate control over a process or clean zone.
- Number of particle size channels – The number of available channels required to demonstrate compliance, or control, of an environment.
- Flow rate – The room cleanliness class determines the number of particles at each size, enough sample volume is required to determine sufficient number of particles such that trend data can be established.
Insitu-Instrument Monitoring System (e.g.: IsoAir Pro E/Plus or Airnet II)
Instrumentation used in insitu-monitoring systems can use portable instruments in a static location and data trended over time, alternatively system specific particle counters are used. System based LSACP devices, tend to have reduced supporting functionality, as the sensor reports to a central computer system, display and printing is not typically required. Other design aspects to ensure suitable transit and analysis of a sample include sensor location and mounting, sensor location relative to sample point and tubing criteria (described above).
Types of instrument used in insitu-instrument monitoring include:
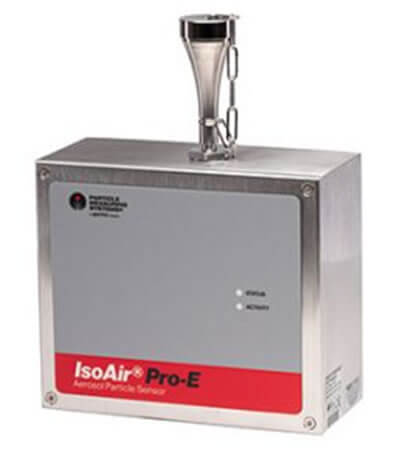
- Dedicated sensor with integrated pump. (e.g.: IsoAir Pro E or Pro Plus)
- These instruments have an internal sample pump, like a portable instrument, connection to a monitoring software system is by secure data exchange format, such that the source of data can be attributed to a specific location, and/or device. Flow rate is nominally 28.3LPM or 2.83 LPM, choice of either sensor is based upon contamination level and sample tubing length.
- Dedicated sensor with external vacuum supply (e.g.: Airnet II particle sensors)
- These sensors have a small footprint and can be easily integrated into smaller spaces. Flow rate is nominally 28.3LPM or 2.83 LPM, choice of either sensor is based upon contamination level and sample tubing length.
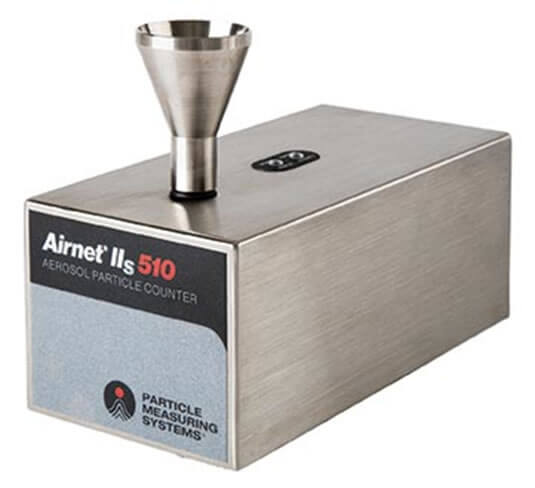