Inspection Resources Hot Topic during 'Ask the Regulators' at PDA/FDA JRC
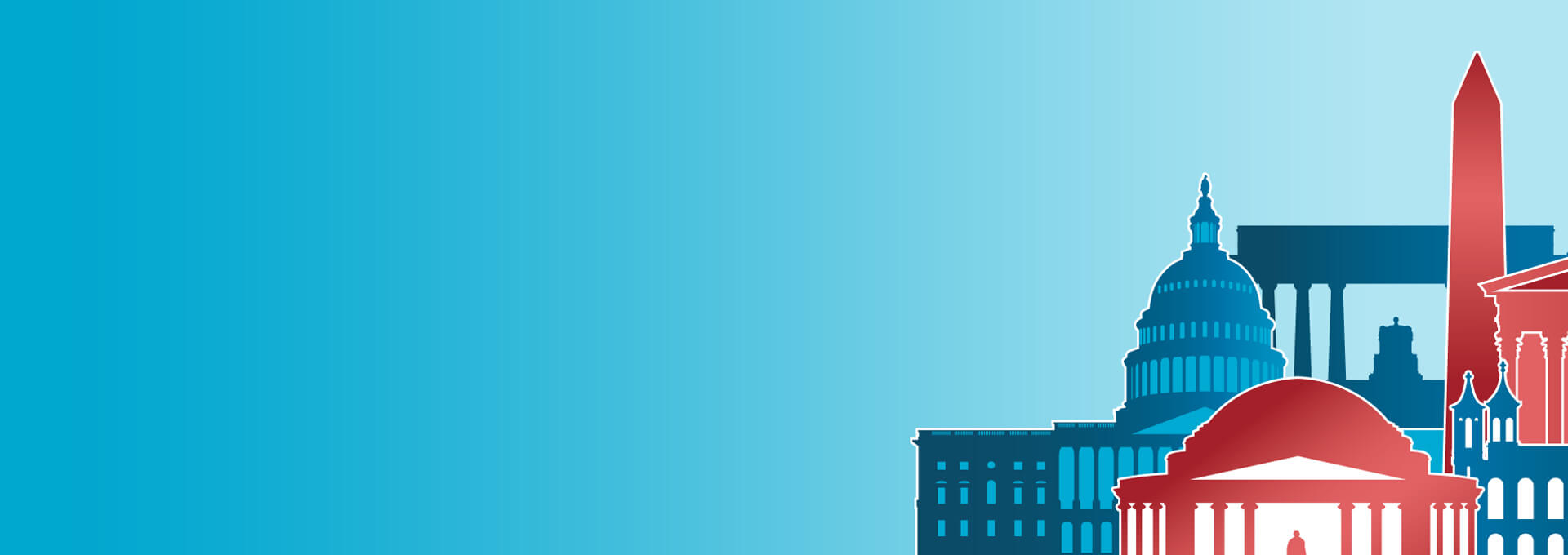
The 2021 PDA/FDA Joint Regulatory Conference, Sept. 27 – 29, was the most successful virtual conference PDA has sponsored since the beginning of the COVID-19 pandemic in March 2020. Over 500 members of the PDA community joined the three-day event from their home or work offices to listen to expert talks by U.S. FDA officials and industry professionals.
The marquee speakers for this year’s event were:
- Alonza E. Cruse, U.S. FDA
- Francis RW Godwin, U.S. FDA
- CDR Tara Gooen Bizjak, U.S. FDA
- Peter J. Hotez, Baylor College of Medicine
- Peter W. Marks, MD, PhD, U.S. FDA
- Judith McMeekin, PharmD, U.S. FDA
- Melissa J. Mendoza, U.S. FDA
- Melissa S. Seymour, Biogen
As always, the “Ask the Regulators: Inspection-Based” session was popular and, on the virtual platform, all attendees had a seat (unless they chose to stand at their desk). Usually, attendance at this session overflows into the hallway!
The inspections panel discussion was moderated by FDA’s Mai X. Huynh, Supervisory Chemist, Center for Veterinary Medicine (CVM), and David L. Chesney, Principal and General Manager, DL Chesney Consulting, LLC.
Questions were directed to the following FDA officials:
- Sandra A. Boyd, Consumer Safety Officer, ORA
- CDR Tara Gooen Bizjak, Director, Manufacturing Quality Guidance and Policy Staff, CDER
- Rachel C. Harrington, Senior Advisor, ORA
- Laura S. Huffman, Senior Policy Advisor, CVM
- Quallyna N. Porte, Branch Chief, CDER
- Richmond Yip, Supervisory Consumer Safety Officer, ORA
Of great interest to participants was how the Agency is handling inspections during the pandemic. When it comes to foreign inspections, always a hot topic of discussion, FDA pointed to its “Resiliency Roadmap” as the chief guide in determining which foreign sites to inspect. Of the factors outlined for consideration in choosing where to inspect, inspector safety is a top priority.
During the pandemic, triaging inspections is even more important across the Centers. Mutual Recognition Agreements (MRA) with EMA and the United Kingdom have proven to be effective tools for CDER/CBER, but are not applicable to CVM. Huffman noted that CVM “is very eager” for the U.S.-EU and U.S.-UK MRAs, which are still in the assessment phases, to be effective soon.
ORA discussed further the impact of the pandemic on field inspections. “Mission-Critical” inspections took priority during the pandemic. According to the Resiliency Plan, 821 such inspections occurred between March 2020 and March 2021, including 29 foreign inspections. ORA’s priority shifts next to for-cause, prior-approval and then, surveillance inspections.
The ORA representatives said that management of the safety of FDA staff and a firm’s employees during an inspection was a key focus. ORA asks companies to communicate with inspectors prior to the site visit so they can anticipate all the measures and protocols up front to better understand what the environment will be.
When asked about preparations for remote inspections, ORA’s representatives outlined several steps:
- Check internet connection to ensure the signal is adequate (a PICs meeting in 2020 noted limited faulty connections are a problem).
- Ensure all electronic documents and records are accessible to inspectors (e.g., encryption/passwords deactivated).
- Before sending records, listen to the FDA inspector and use the proper gateway, i.e., email, box.com or another. If the firm has concerns about the gateway, discuss it with the investigator so FDA can come up with an alternative solution.
- Specifically stated in guidance: Documents submitted during inspection should be in English, but the facility can provide a translator during the inspection.
- Enable FDA’s remote-viewing and verification, particularly when records are in an electronic system; use PDFs when possible.
CVM noted that remote inspection alternatives are most appropriate when an inspection record has already been established and there is an existing GMP history, especially for high-risk manufacturing operations. CVM has used record requests in lieu of a site visit to support submissions.
ORA was specifically asked about common data-integrity gaps in recent FDA observations. In their reply, they noted that 34% of warning letters in the last five years contained charges of unreliable data.
FDA is also starting to see another problem on top of unreliable data found during inspection and submitted remotely: a lack of DI governance programs. The ORA officials said FDA still encounters firms that do not have a data governance plan to ensure that data across facilities are being appropriately handled and core principals are being met.
With respect to helping facilitate inspections of data, they noted two things:
- Electronic data and review of electronic chromatograms. FDA investigators are “getting better at reviewing the e-data.” When submitting the packet, investigators will need assurance that the same sample was not tested at another time. To evaluate and sort through all the data, investigators will want “some sort of reconciliation of samples.”
- Documenting investigations contemporaneously, especially when using software to track. If looking at an investigation from three months earlier, FDA should see more than the investigation was initiated and this is what it was about. Maybe the information is on someone’s notepad, but shouldn’t be uploaded at the very end. Companies must “stay on top of” investigations so the FDA can follow it.
When responding to inspection findings, ORA’s reps said they encourage firms to provide responses in a structured format. Often, firms do not look at issues identified during the inspection “holistically” in order to properly define the scope of remediation. The inspection “only captures a snapshot” of problems. As such, “firms should really look at that systemic point of view.”
When it comes to using consultants to solve problems, FDA advises firms to “make sure they have the background needed and provide them all the information so they can do a good review.”
One questioner asked about the handling of high absenteeism. The FDA representatives stressed the importance of planning ahead. Companies should identify what constitutes high absenteeism and decide when to activate or deactivate an emergency plan, which should be developed in advance. They should also prioritize medically necessary products over others and determine which activities can be delayed or modified in frequency or substituted. A key to ensuring success is the documentation of all actions taken. FDA’s guidance on the subject gives recommendations on how to bring a facility back to normal operations. The FDAers noted that there are many different factors and is a crucial question that a company must consider.
Another questioner asked for FDA’s thoughts on taking quality assurance out of deviation review when there is no quality impact. The panel was unanimous against supporting this idea. They noted that there have been cases where a firm thought a deviation did not impact quality initially, but then found later there actually was an impact. These things are “not easy to determine up front…some seem simple and straightforward but, once initiated, the deviation investigation can turn up things.”
Companies are advised to look at the regulations that spell out Quality’s responsibilities. CFR 211.22 states that the Quality Unit has the responsibility and authority to conduct investigations. CFR 211.192 says that, at the time of batch release, Quality has to ensure all deviations are investigated.
The panel further stressed that Quality must be from the top down—a “part of the organization.” FDA’s warning letters emphasize the critical role of executive management in oversight.
FDA understands that mistakes happen; companies, therefore, must be transparent about them. Strong quality management systems are key. They pointed to the data-driven work by PDA and St. Gallen on quality culture as valuable to the industry. The panel recognized much “improvement” in the industry over the last five years.
There were many other questions and answers during the session. Next year, PDA looks forward to hosting this popular session in person next year.