Intrinsic Sterile Connection Devices Results of an Industry Survey
What environmental classification is required when making connections between previously sterilized wetted-path parts as part of the aseptic manufacture of sterile products?
Traditional, "open aseptic" operations require Grade A laminar flow with a Grade B background to protect the flow path from microbial ingress. However, the newly revised EU GMP Annex 1: Manufacture of Sterile Medicinal Products mentions that lower environmental classifications can be acceptable if the connections are made using "intrinsic sterile connection devices." In the text of Annex 1, we see that this term applies to two commonly used types of technologies: sterile tube welders and single-use, mechanical sterile connectors. Although the revised Annex 1 appears to be the first explicit acknowledgment of these technologies in regulations, both intrinsic sterile connection devices have been used in the industry for decades.
This new language regarding intrinsic sterile connection devices raised awareness that there is no comprehensive survey of current industry practices for these devices, particularly concerning what environmental classifications are seen as necessary for their use.
Results of the Survey
The PDA distributed a survey on this topic to sterile pharmaceutical manufacturers via the PDA Interest Groups and obtained 28 unique responses. There were 8 responses that represented the position of global companies, 13 represented the position of a single manufacturing facility and 7 were by consultants responding based on their experience with clients or past employers. A summary of the responses is presented below.
In an attempt to limit responses to those that truly use these technologies for aseptic processing, such as downstream of the final product sterilization step (e.g., downstream of the final filtration process), the survey below was introduced with the following text:
“This survey is for firms that manufacture sterile products and/or sterile product intermediates that are produced aseptically (not sterilized in their final container). It is intended to capture the variety of practices associated with making connections between separate pieces of equipment used in sterile processing and the controls used to ensure sterility is maintained. Please only respond to this survey if you represent a company or facility that manufactures sterile products or intermediates and for consultants of those facilities.”
Q1. Which types of aseptic manufacturing process are used at your firm?
Type 1: Processes where sterilization occurs immediately prior to filling. For these, no more than a dosing vessel and the filling wetted path are within the sterile boundary.
Type 2: Processes where product sterilization occurs upstream of final drug product formulation. The formulation vessel and formulation process are within the sterile boundary.
Type 3: Processes where the product sterilization occurs during downstream drug substance manufacturing. The final drug substance is sterile, and the full drug product formulation and filling process is sterile.
Type 4: Processes where even upstream drug substance manufacture is within the sterile boundary (e.g., pure culture cell expansion and virus propagation for live virus vaccines, with no further downstream sterilization).
Figure 1 Types of Aseptic Manufacturing
Q2. Which methods are used to make connections between the pieces of equipment that form your sterile boundary?
Method 1: Sterile tube welders are used to make connections between already-sterilized systems.
Method 2: Mechanical (single-use) sterile connectors are used to make connections between already-sterilized systems.
Method 3: After open connections are made (e.g., hard piping), the flow path is subsequently sterilized (e.g., steam-in-place).
Method 4: "Open" (not intrinsically sterile) connections are made under Grade A aseptic conditions.
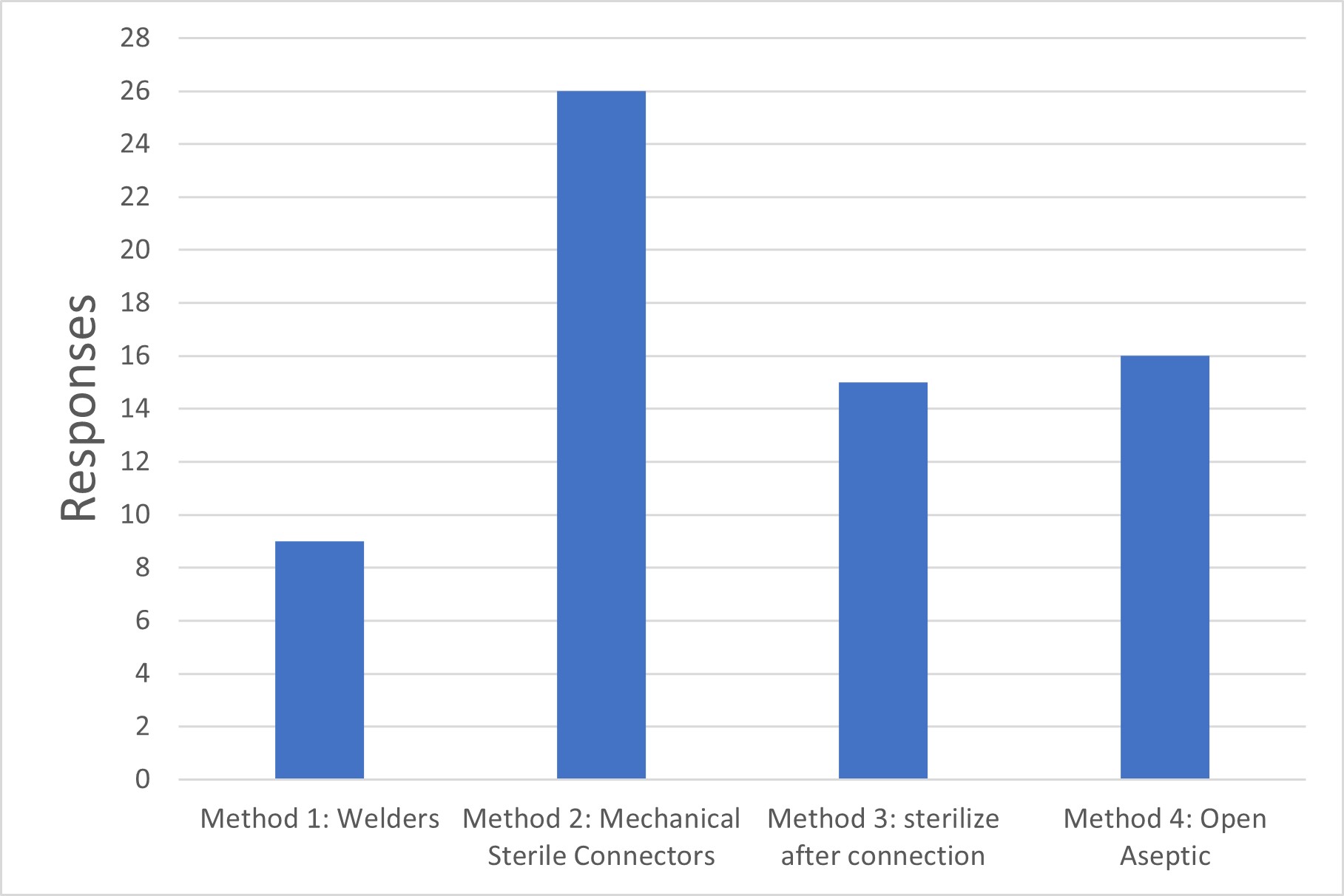
Figure 2 Sterile Connection Methods
Q3. What is the minimum environmental classification in which you use sterile tube welders?
The survey asked for a list of all environmental classifications in which tube welders were utilized. Many respondents answered with multiple grades (e.g., Grades A, B and C). This data was used to calculate the minimum grade used and reported in the survey (Grade C in this example) under the assumption that the minimum classification is deemed acceptable, while occasional use in higher grades is due to the presence of other critical aseptic operations in the same process, which drove the selection of the higher-class environment. Tube welding also happens to be performed in this area. This assumption was confirmed by a subset of survey respondents.
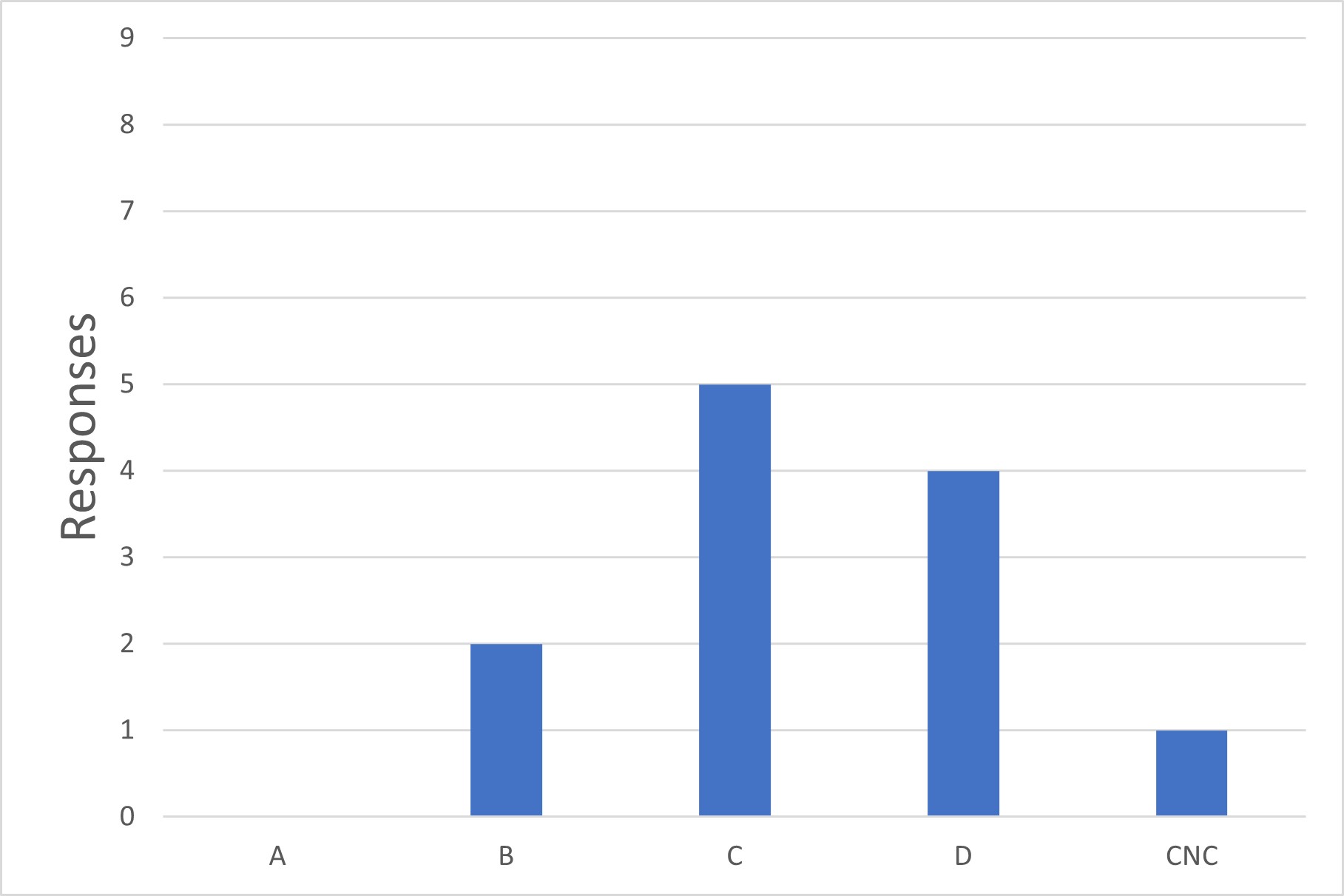
Figure 3 Lowest Grade Used for Tube Welding
Q4. What is the minimum environmental classification in which you use mechanical sterile connectors?
Like question 3, the survey asked for a list of all environmental classifications in which mechanical sterile connectors were used. This data was used to calculate the minimum grade used and reported here.
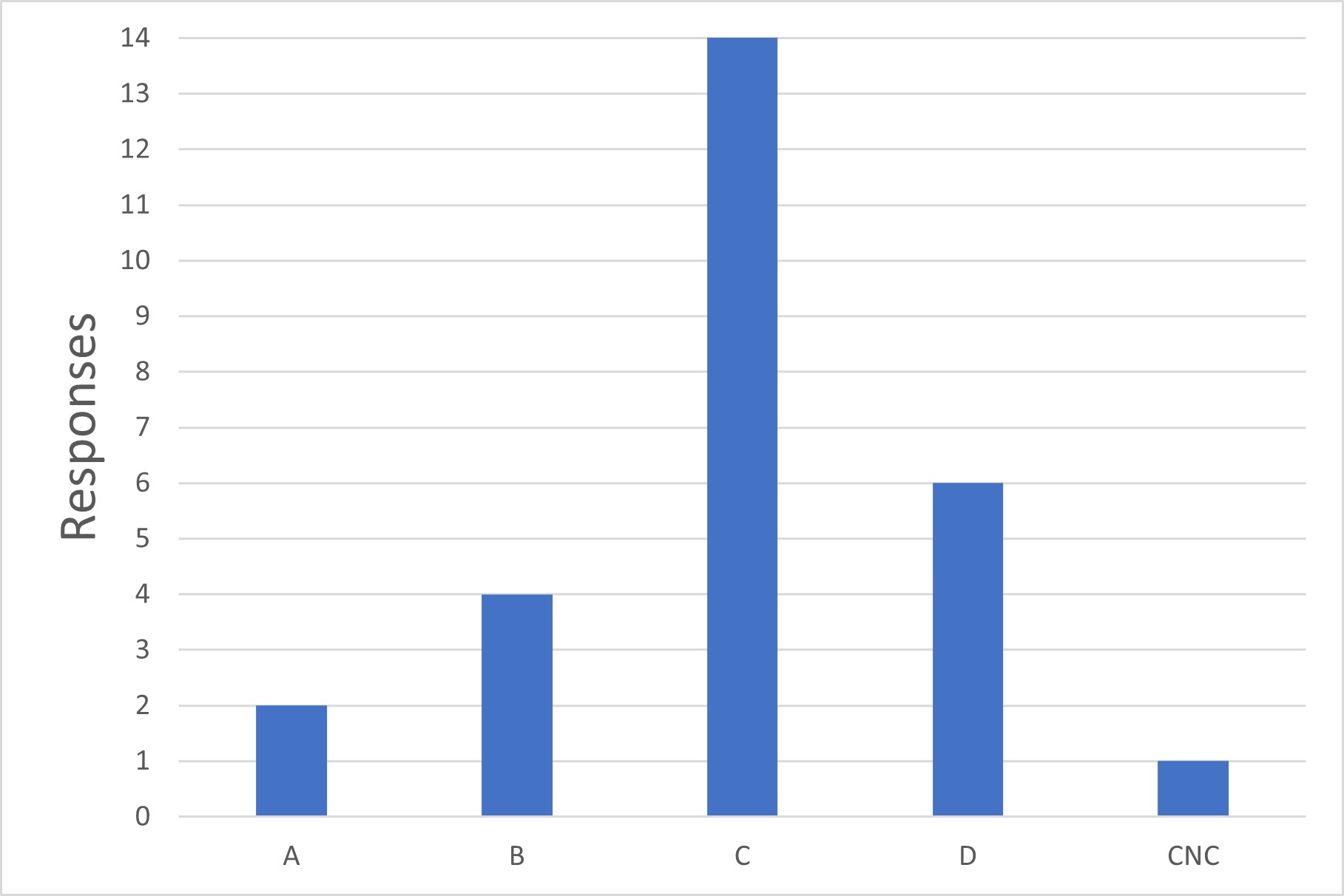
Figure 4 Lowest Grade used for Mechanical Sterile Connectors
Q5. Do you consider that connecting previously sterilized single-use systems with intrinsic sterile connection devices in Grade C or D can still be considered part of a closed system for the purposes of sterile manufacturing?
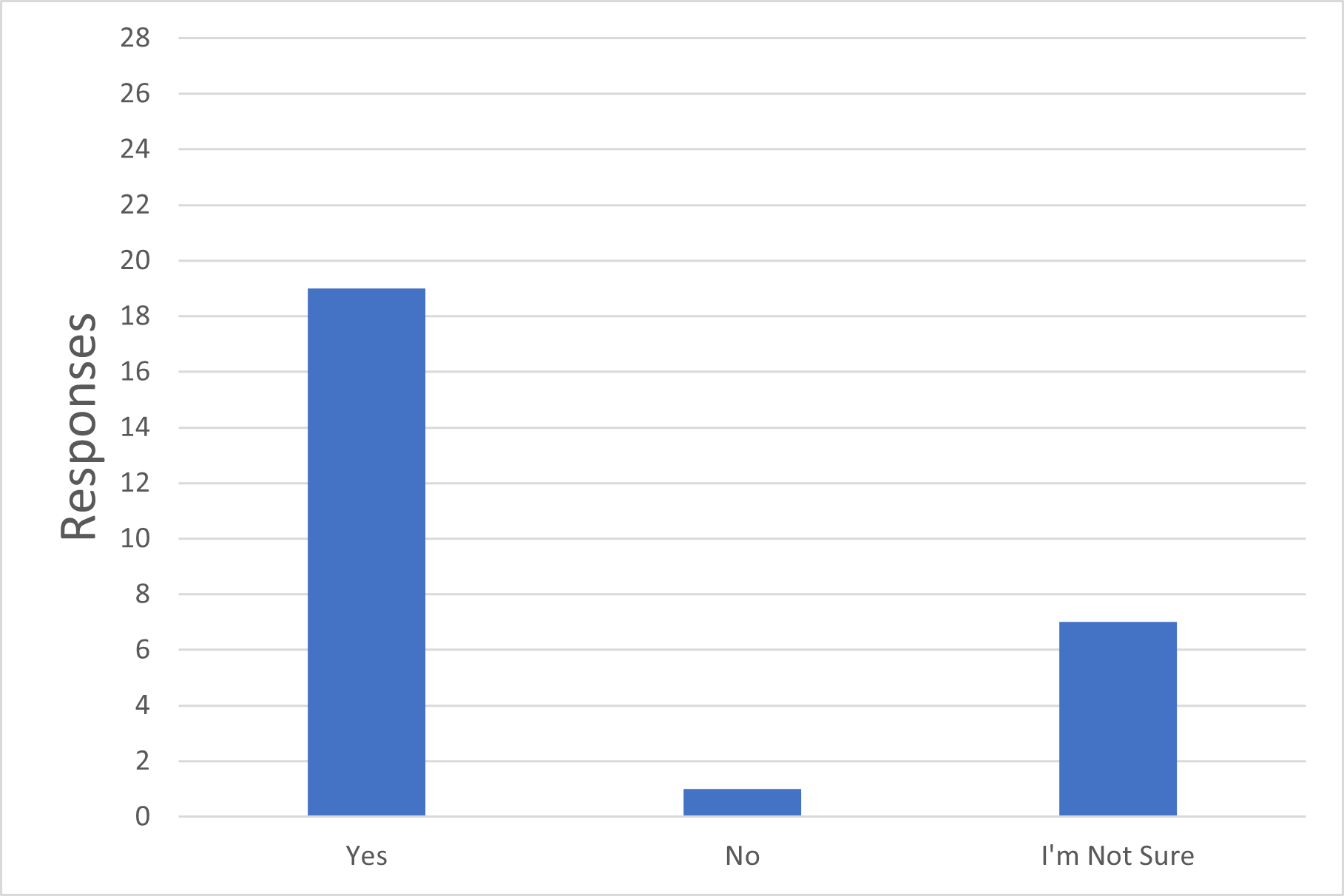
Figure 5 Sterile Connection Devices
Q6. Which of the following reflects your firm’s stance on the two primary categories of intrinsic sterile connection devices?
Statement 1: Tube welders are superior to mechanical sterile connectors with respect to sterility assurance.
Statement 2: Mechanical sterile connectors are superior to tube welders with respect to sterility assurance.
Statement 3: Neither technology (tube welders nor mechanical sterile connectors) is inherently superior to the other.
Statement 4: Not Sure.

Figure 6 Types of Intrinsic Sterile Connector and Its Superiority
Conclusion
It is apparent from the survey results that the majority of industry users of intrinsic sterile connection devices use them in Grade C or lower, even for aseptic processing. This use appears to be acceptable by the revised text of Annex 1. However, the industry still lacks standard guidance on these technologies' details and how they should be validated, controlled, tested and inspected. This illustrates an opportunity for further work. Additionally, there does not appear to be a preference for one technology over the other in Annex 1 (welders versus mechanical connectors). Still, responses to question Q6 indicate some apparent preference in the industry.
Lastly, it is noted that a detailed comparison of the two technologies has not been performed holistically in a thorough manner to consider all the differences and similarities of the technologies. For example, tube-welded connections are much more amenable to post-connection visual inspection than mechanical, sterile connectors, where the connector bodies can hide the critical connection location. Overall, this can be seen as an additional need in the industry to assist in selecting appropriate connection technology.
Feedback and Clarification Responses
- “Tuber welding used for disconnection only.
- Regarding question 5, “Dependent of supplier validation package. Grade C can be considered as acceptable, Grade D cannot.”
- “Our closed systems involving tube welders are outside of the sterile boundary and we do not claim sterility (rather low bioburden), but our experience shows that sterility is achieved.”
- “We have not investigated the tube welding technology. Regarding closed systems, it is important that the product pathway is integral throughout. Quality from suppliers is important - how are these components qualified?”
- “Requirements to supplier very important to have in place at an early stage of implementation. Suppliers change notifications can create delivery, process or quality challenges.”
- “Maintaining the qualified state, routine maintenance and blade management, add additional variables to tube weld sterile connections that do not exist with the single-use connectors. The bigger risk with the sterile connectors is leak management, which can be mitigated by trained operators and tubing supports to minimize stress on the connectors.”
- Regarding question 5, “yes provided that the risk from holes is mitigated for instance by the use of pressure. It also depends on where the sterile connection is in relation to the point of sterilization.”