New ISO Standard Available for Water Systems 7 Major Highlights from the New ISO 22519 Purified Water and Water for Injection Standard
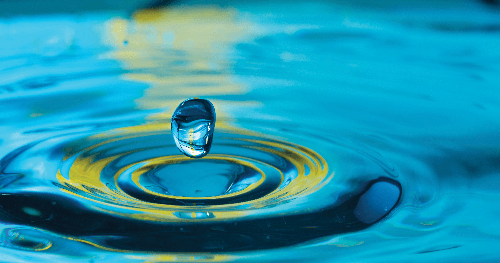
The final water specifications for Purified Water (PW) and Water for Injection (WFI) are given in national and international standards and are well defined and well understood. On the other hand, water systems come in all shapes and sizes; some need daily maintenance and some are grossly inefficient. Some have excellent microbial standards and some require close supervision. Water systems must adapt in response to feed water quality, meet budgetary constraints and keep in accordance with both company policy and cGMP.
Plenty of guidelines and literature are available addressing water systems, but a cut-and-dried standard for producing PW and WFI is not in place. To address this lack of a standard, ISO 22519 Purified Water and Water for Injection Pretreatment and Production Systems is presently in the final stages of approval and expected to publish this month (1).
What is important about this standard? Users for the first time ever can specify water systems that fit their specific needs without being experts in the water system field. Anyone looking for a benchmark can refer to the standard and use it as a point of reference for designing and operating a water system.
One of the main motivations behind the new standard is to improve reliability of water generation process methods and water product while reducing the downtime needed for scheduled and unscheduled maintenance. Microbiological aspects of the pretreatment and production of PW and WFI systems are also now considered and the standard offers action/alert levels. Most modern PW generation systems are based on reverse osmosis membranes. The standard has been written with this in mind, and it provides specifications in reference to reverse osmosis membranes.
Major Areas of Focus for Pharma
There are seven main parts to this standard that manufacturers working with water systems must take into account:
- Stainless steel construction
- Hot water sanitization
- Continuous bioburden reduction after every stage
- Continuous system recirculation
- Detailed categorization of feed water
- System selection table for components
- Advantages and disadvantages of system components/treatment stages
1. Stainless steel construction
In the interest of reliability, cleanability and simplicity, the standard specifies that piping must be stainless steel only. This is understandable, as the standard recognizes hot water sanitization as the only effective method of sanitization. Plastic heat-resistant piping has been discounted as a legitimate construction material since high-quality, heat-resistant polymeric piping with “no bead” welds is hard to reliably achieve. In the interest of keeping the standard simple and foolproof, stainless steel piping is given as the only option.
2. Hot water sanitization
Hot water is one of the most effective sanitization methods. Proper contact with water above 80 °C will easily penetrate biofilm and kill the bacteria within. In addition, the hot water sanitization cycle does not use disinfectants, so there is no need to flush chemicals at the end of the sanitization cycle. Here, systems can be relied upon to heat up, hold at high temperatures and then cool down autonomously without human supervision. In this way, the sanitization cycle is repeatable both in the heat/cool cycle, and, once programed, can perform the routine on a regular schedule without interference.
The standard stipulates that all the sanitization parameters in the system must be controlled and recorded.
3. Continuous bioburden reduction after every stage
The standard states that a full measure of control shall exist and improvement of the main characteristics of the water should occur after every stage. In fact, if bacterial levels in the treatment stages increase as water advances through the system, this demonstrates loss of control.
Bioburden is singled out as the most problematic of all the needed parameters, but it is not the only parameter that must improve.
The final bacteriological performance of a system is an amalgam of initial design, installation standards, day-to-day operation and regular maintenance—all of which has been referenced in the standard.
In addition, the standard covers pretreatment. Here, a great deal of effort has gone into parameters for defining and selecting pretreatments to keep microbial growth within a water system to a minimum. The principal in the standard is that this pretreatment must lead to uncontrolled amounts of bacteria that deposit slime on the reverse osmosis membrane, as this could eventually send permeate microbial levels out of specification. Table 1 shows the ISO 22519 recommendations for water quality after every stage.
The standard recommends continuous bacterial reduction for both PW and WFI systems, yet states that this is is “indispensable” for WFI systems.
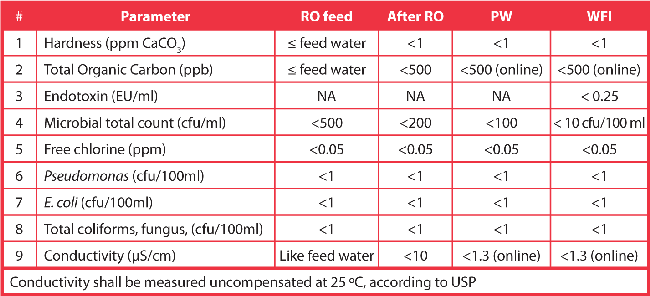
4. Continuous system recirculation
When the PW/WFI tank is full, it is common to stop the production of PW/WFI water and the production system goes into a shutdown. The system will restart when the storage tank level falls below a set point. This practice is frowned upon by the ISO standard; production systems are expected to keep recirculating, even when the PW/WFI storage tank is full.
This principal dovetails with the previous principal of improvement in system parameters as the water passed through the system as, without constant recirculation, this improvement is hard to achieve.
5. Detailed categorization of feed water
In water systems, there is no “one size fits all;” the system must take into account differing feed water parameters. Most feed water parameters are easily ascertained by laboratory analysis. Well-known and tested engineering design rules are used to design equipment that can achieve the essential chemical and bacterial criteria. Problems may result in cases of unstable parameters in the feed water.
In the ISO standard, parameters are given for the four main types of feed waters that have been identified:
- Typical
- High bioburden with high organics
- High hardness
- High silica/high iron/high manganese
Each category has been characterized by the following parameters:
- Total Organic Carbon (TOC)
- pH
- Conductivity
- Total hardness
- Microbial total count
- Total coliforms, pseudomonas, E. coli, fungus
- CO2 level
- Total silica
- Iron
- Manganese
Using this information, a manufacturer can determine an appropriate system configuration.
6. System selection table for components
ISO 22519 includes a recommendation table built around the category of the feed water but also on the needed standard of product water. For instance, if the feed water is typical, the selection table recommends single-pass reverse osmosis for PW product and double-pass reverse osmosis for WFI product.
On the other hand, if the feed water is high in bioburden and/or in organics, the standard recommends double-pass reverse osmosis for both the PW and WFI systems.
The table also details the type of initial filtration needed (multimedia filter, ultrafiltration, disk filter), the type of scale reduction process (electrical scale reduction, softener, antiscalant), which sanitant could or should be added and how it should be removed (UV, active carbon, sodium bisulfate).
If high CO2 is encountered in the feed, the standard also provides recommendations for the best process for removal.
7. Advantages and disadvantages of system components/ treatment stages
Almost six pages of the standard are dedicated to analysis of different water process equipment, delineating advantages and disadvantages. Multimedia filters, pretreatment ultrafiltration, flushed screen/disc filters and chlorination are among the equipment reviewed.
Conclusions
ISO 22519 is the first international standard to be written for water system equipment and operation. This standard will be a yardstick in the hand of inspectors, designers and users, enabling them to evaluate or design a water system. The global scope of the system descriptions that have been selected per incoming water specifications is unique.
Systems that follow the standard’s recommendations will minimize proliferation of biofilm and pathogens and will meet the pharmaceutical market demands of a welldesigned system capable of controlling bioburden from beginning to end.
Any standard on a subject as broad and complicated as water systems for PW and WFI production cannot hope to contain all the possible situations and feed water parameters, however, tools and principals have been set out that will allow the design and evaluation of as many different feed water values as possible.
Reference
- ISO 22519: Purified water and water for injection pretreatment and production systems. June 2019. www.iso.org/standard/73381.html