Pharma Firm Explores RFID for Prefilled Syringes
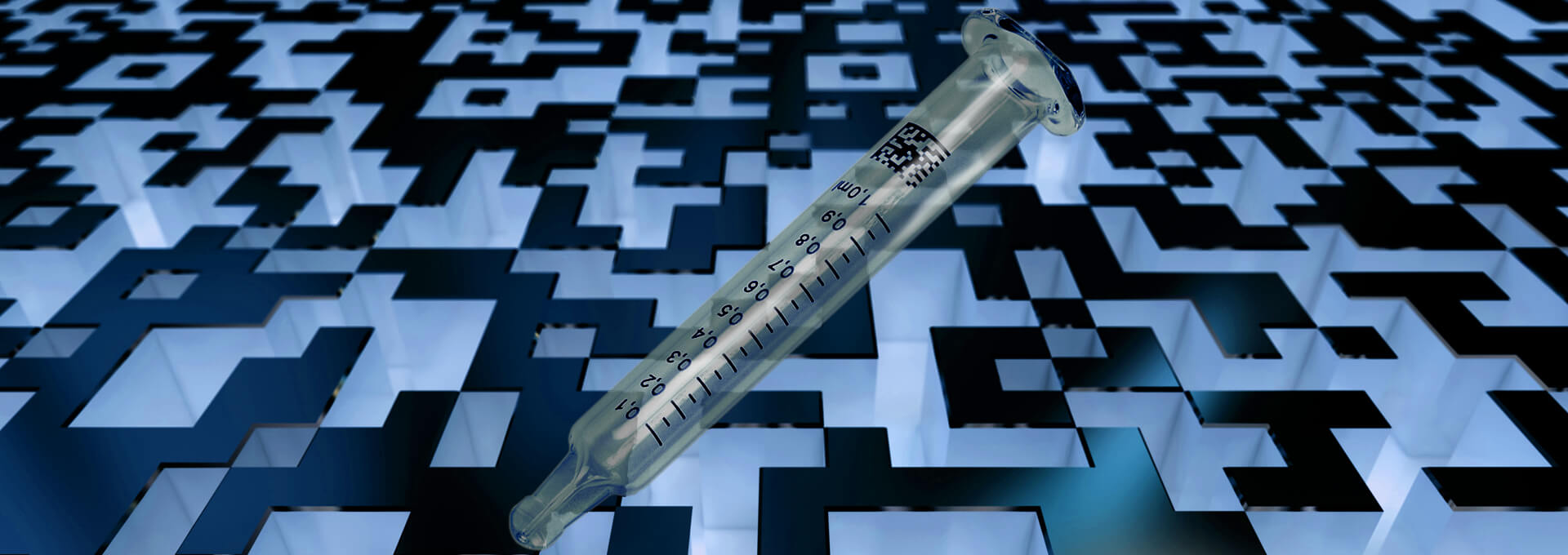
Traceability can be a complex subject due the different process requirements and company needs.
Gabriele Peron, Senior Marketing Advisor, Stevanato Group, interviewed Yves Steffen, Head Packaging & Device Commercialization, Novartis, to understand how his company is managing regulatory scrutiny on product traceability within pharmaceutical manufacturing operations. U.S. FDA 21 CFR 610.14 has been revised and requires that the contents of a final container of filled biologic product be tested after completion of labelling.
Peron: What impact do you think the FDA 21 CFR 610.14 will have on the traceability within pharmaceutical manufacturing processes?
Steffen: I believe that traceability on the container level will become very important, and not only to prevent mix-ups during manufacturing, especially when looking at development pipelines and the manufacturing strategies applied in many big pharmaceutical companies. In addition, these solutions can provide additional benefits to improve manufacturing processes and simplify investigation work in case of potential deviations in manufacturing.
Peron: What time frame has been given for full compliance?
Steffen: Compliance is already required, as 21 CFR 610.14 became effective in April 2014. The most common processes and technologies applied to keep compliance up to date, however, will soon meet technical limitations (e.g., colour code ring marking). Therefore, we need to look for alternative more forward looking technologies.
Peron: What other regulatory initiatives are driving the traceability of primary packaging?
Steffen: An updated version of USP <1790> Visual Inspection of Injections was published in Spring 2019. It includes a section that places responsibility on manufacturers to analyze trends in inspection systems. Today, it is not enough to inspect and reject items, but you must also determine the normal reject rate and in case of a deviation (or a trend) to investigate root causes. This must be done on a periodic basis and be based on sound Statistical Process Control principles. In general, data collection and data analysis in normal commercial manufacturing will become more relevant and single container traceability will be a key feature to enable better process controls.
Peron: What do you perceive as the main roadblocks to implementing traceability on primary packaging?
Steffen: Finding a solution that can be implemented with limited efforts in existing commercial manufacturing processes and can be applied as a platform technology within the pharmaceutical industry. Most solutions are complex and cost intensive to implement.
Gabriele Peron served as one of the team members who authored 2019 PDA Traceability of Primary Packaging Survey. The survey can be purchased at the PDA Bookstore.
Peron: Is having a standard or a guidance document covering traceability for the industry beneficial or will each company make its own decisions?
Steffen: From my view this is a must in order to avoid multiple platforms—a baseline guidance should be established to ensure that all manufacturing sites are using the same standards. Establishing a standard will also help to control costs and enable all manufacturers to focus on one technology.
Peron: Are there any successful initiatives that you can highlight or refer to?
Steffen: At Novartis, we believe the most promising solution is RFID technology included in the primary packaging container. We are also aware of some other initiatives in the industry that have potential benefits.
Peron: Looking at the industry trends on traceability, do you believe that the regulators will require more data over time?
Steffen: Yes, at Novartis, we have already experienced regulators asking for more information on the container level (e.g., batch number and material number). Going forward, I could also see that additional data needs to be placed on the container (e.g., temperature monitoring, filling volume etc.). That is why a flexible solution is key to avoid having multiple standards for product traceability and to be ready for any future requirements.
Peron: If so, what in your opinion is the best way to handle the data requirements?
Steffen: For RFID, it is important to agree on a standard writing and reading protocol and on a chip technology that can be used as a platform—it is important that the flexibility is given due to different requirement from each manufacturer. Currently at Novartis, our focus is on integrating RFID functionality on prefilled syringes; going forward, we are considering including an RFID chip to capture internal manufacturing traceability and data collection for vials and cartridges.
Peron: Do you think that existing serialization platforms might be able to offer a solution, and, thus, reduce future data management investments?
Steffen: This is certainly a possibility, but again, there would need to be a standard approach. It would require a range of aligned stakeholders to ensure this can be managed in the right manner for all the manufacturing processes.
Peron: Finally, are there any traceability initiatives or technologies that have caught your attention?
Steffen: From what we at Novartis have seen over the past six years, the most promising solution involves including RFID technology in the primary packaging container. Novartis has placed a priority on investing in the technology to place an RFID chip in the RNS of the prefilled syringe. Planned commercialization for this new product is scheduled for the end of 2020.