Spotlight on Packaging Regulations and CCI
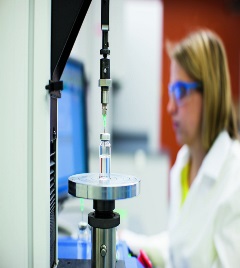
The PDA Letter interviewed West Pharmaceutical’s Director of Container Systems R&D Jay Stephens, PhD, about regulatory issues affecting packaging and container closure integrity testing.
Photo courtesy of West Pharmaceutical Services, Inc.
PDA Letter: What is your advice for how manufacturers and suppliers developing new packaging technologies can address regulatory challenges?
Stephens: The global regulatory landscape changes frequently. Both drug product and delivery system manufacturers must establish a sound and harmonized development process with a reliable quality system to mitigate risks for combination products. Emphasis should start with the end user in mind, establishing a framework that is complete in drug product profiles and key attributes for component development. Mitigations to identified hazards should tie into the effectiveness of controls on both the drug itself, and the system to which it is to be administered.
Another key attribute is to isolate the container closure system for launch as early in the clinical phase as possible. The key is to draw as many parallels between pharmaceutical and component manufacturing as possible. There are synergies for products as captured in 21 CFR 4. Drug product manufacturers and device manufacturers should link elements from the ICH Q8–10 quality guidelines to standards such as ISO 13485 Medical devices – Quality management systems – Requirements for regulatory purposes, ISO 14971 Medical devices — Application of risk management to medical devices and 21 CFR 820. This enables the appropriate launch plan and regulatory assessment to ensure the appropriate design inputs meet the desired outputs for a successful launch.
PDA Letter: What else should manufacturers consider?
Stephens: Selecting the appropriate delivery system for a drug product requires understanding the requirements to keep the drug product stable, the method of delivery to patient and the market landscape to ensure that the appropriate delivery system meets the requirements for drug product approvals. A pharmaceutical company's launch plan is critical to identify early in the drug product development cycle the appropriate components needed to deliver a safe and efficacious medication to the patient which also complies with regulatory requirements for filing purposes.
Drug product requirements should directly impact the preliminary assessment of critical quality attributes of a container closure system. Furthermore, the appropriate verification and validation testing should be performed not only on a component level but also as a system. With the emphasis shifting to combination product testing, an integrated approach to ensure compliance with specific standards is best practice when selecting a supplier to mitigate risk and ensuring successful uptake in the market with the appropriate delivery system.
The author will be attending the 2019 Universe of Pre-filled Syringes and Injection Devices in Gothenburg, Sweden, Oct. 22–23.
PDA Letter: What are some of the current challenges facing vendors developing new syringe technology?
Stephens: While vials are still a preferred container for many injectables, the use of a glass or polymer prefilled syringe offers a variety of benefits, including ease of use, less overfill volume of the drug product to help reduce cost per dose and a more precise dosage to help ensure patient safety. Not all component providers have control over all elements of the appropriate container system for a drug product. Design controls provide a uniform, systematic and iterative model for design and development to ensure that the container system is safe and effective. This is more easily achieved when the manufacturer produces all the components which make up a prefilled syringe system, but this is not always the case.
Glass systems could include components from up to three different suppliers, though this adds complexity to combination products. This is where a robust design verification and validation plan is key to characterizing specific components to use together in a safe and efficacious manner. Verification testing is a true to test for a vendor to address the question of “did I make the product right?” A vigorous engineering confidence test plan can ensure compliance to standards, dimensional verification and comparison to established container systems to demonstrate the effectiveness of a combination product. If a vendor can address the protection, compatibility, safety and performance of a prefilled syringe system, then the appropriate level of confidence can be achieved when recommending their product to a drug product manufacture.
PDA Letter: How can companies ensure container closure integrity?
Stephens: Similar to other sterile products, prefilled syringes must be sterile and free from pyrogens. In general, the regulatory requirements for testing prefilled syringes need to comply with the U.S. and European pharmacopeias, either by probabilistic or deterministic methods. Testing must be compliant with existing test and release criteria for empty containers and those filled with the drug product solution. As such, both drug and device regulations apply to prefilled syringes. In many ways, the prefilled syringe is more complex and intricate in comparison to a traditional vial; they have multiple sealing sites that require integrity.
Regulators are paying more attention to container closure integrity, especially since the release of USP <1207> Sterile Product Packaging—Integrity Evaluation, which endorses deterministic methods for detecting container closure integrity. High voltage leak detection (HVLD) is very well suited to syringe systems. HVLD equipment operates by moving a high-voltage probe along the length of a syringe and a defect results in a visible discharge through the fluid in the syringe system. HVLD can be useful for detecting a defect between the syringe body and plunger.
Another method that is widely used in industry is He Leak detection, which emphasizes the importance of pharmaceutical companies understanding the maximum allowable leak limits of their drug products. As such, direct use of helium leak with a polymer-based system will result in a leak rate above that measured with a glass-based system, that may be misinterpreted as resultant from a nonintegral system but is from Helium permeation. This could be overcome by addressing areas of test method development, such as fixture design and testing environment, to isolate the elastomer/polymer interface to accurately measure container closure integrity. The aforementioned examples illustrate the importance of pharmaceutical companies and suppliers to align on characterizing a particular prefillable syringe system to ensure patient safety and sterility of the drug product contained therein.