The Product Quality Leader Team Part I: Building the PQL Role

Since launching the Product Quality Leader (PQL) role in 2018, AstraZeneca has seen success by leveraging the role to ensure greater quality assurance of the company’s biologics operations in only a year.
In addition to greater quality assurance, the PQL role also serves as a development path to build up the leadership skills of emerging quality leaders within the company who have also provided fresh ideas for the role as well.
What is the Product Quality Leader Role?
The Product Quality Leader (PQL) is an independent representative who provides effective and efficient feedback and oversight regarding quality issues between the CMC team and functional quality groups. The position requires a technically competent quality professional who has experience in leadership, management, decision-making, strategic planning and organizational effectiveness and comfortable in working within a matrix organization. This function is intended to build quality into the product and provide global ownership of the manufacturing behind specific products.
The PQL provides functional expertise and guidance to their assigned team, communicating project needs to quality functional areas (e.g., external quality, quality assurance, lot release) and developing the overall product quality strategy for the CMC team. Figure 1 illustrates the basic relationship of CMC team representatives within their functions and within the CMC team.
Some of the responsibilities of the PQL include:
- Representing the quality function at clinical CMC team
- Engaging with all quality stakeholders impacted by product team strategies
- Approving product specifications and justification reports
- Approving comparability protocols and reports
- Owning combination product specifications
- Approving process performance qualification control strategy document
- Reviewing regulatory submissions to ensure a consistent “story”
- Managing CMC change log
- Advise on product impact for nonconformance events and product complaints
- Engage in external and influential activities, as available
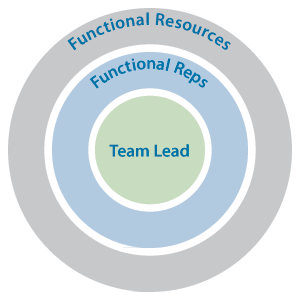
The First Steps
As a newly established function, the team overseeing the role promoted it internally as a career-growth opportunity, encouraging newer and somewhat less-experienced staff to apply. This resulted in a flood of applications. Applicants with scientific knowledge, openness to working within a team, good communication skills and strong organizational effectiveness skills who were also identified as being “developable” were recognized as those most likely to thrive in the PQL role.
At the same time, AstraZeneca actively promoted the PQL program to the entire company, strongly encouraging that some existing roles and responsibilities within the overall quality department transition to the PQL role. To ensure the success of the PQL program, the team overseeing it provided regular updates on its development and any resulting changes to quality operations. Communications also focused on the new “footprint” for stakeholder/partner-agreed review and approval tasks.
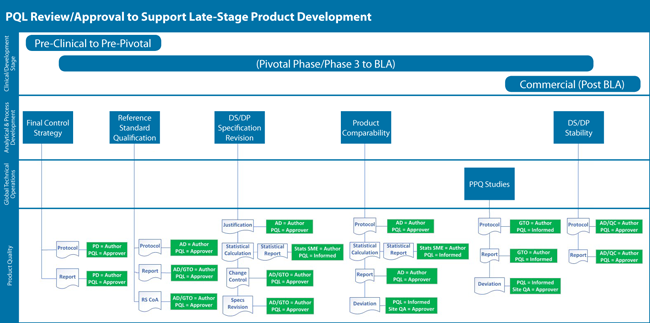
For instance, review tasks for the new PQL function were mapped out for each major product development stage. A simplified example, illustrated by Figure 2, shows some of the major CMC tasks during late-stage development that are reviewed/approved by the PQL. The tasks (blue boxes) are associated with each accountable functional group along with the types of documents identified that the PQL function reviews and approves.
To standardize the PQL review process and achieve consistent outcomes, detailed process maps were developed. Additionally, job aids from the shared review/approval experience covering all relevant lessons learned were included with the process maps. This helpful information was made readily available to all PQLs via a shared-access database; each of the CMC teams have access to this information as well. By ensuring this information is directly visible to all CMC team members, organizational effectiveness improved.
The success of the project also required collaboration among various quality groups to establish the required changes. Some PQL members drafted a roles-and-responsibilities matrix and provided initial suggestions to other quality staff. Multiple meetings with individual functions were required to resolve differences; the final draft matrix was then reviewed by all quality functions before being published in a shared-access database.
Figure 3 illustrates a simplified matrix table. For example, while the product expiry date assignment (EDA) is the approval responsibility of the PQL, an out-of-specification (OOS) investigation is conducted and approved by site Quality Assurance (QA), with the PQL functions in a consulting role, analyzing for any potential effects to product quality. A sufficient level of clarity and granularity was needed for new or changed review/approval roles so responsibilities could be properly assigned. This was deemed crucial to making the transition process as transparent and painless as possible. Ultimately, it provided an established foundation for improved future operational effectiveness—one of the many benefits of the PQL function.
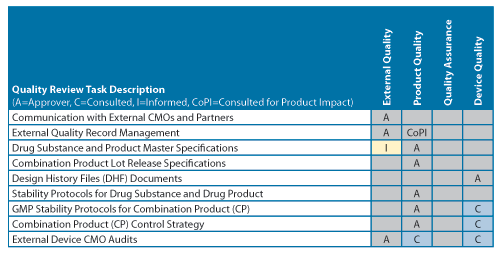
One year after starting this program, the PQL role has proven to be a successful way to ensure quality within the biologics function at AstraZeneca. The involvement of emerging quality leaders have also enhanced the role by continually refiningit.
[Editor's Note: Part II of this article will look at a team building exercise based on lean principles that involved a team consisting of all the PQLs.]