The Product Quality Leader Team Part III: Staying Ahead
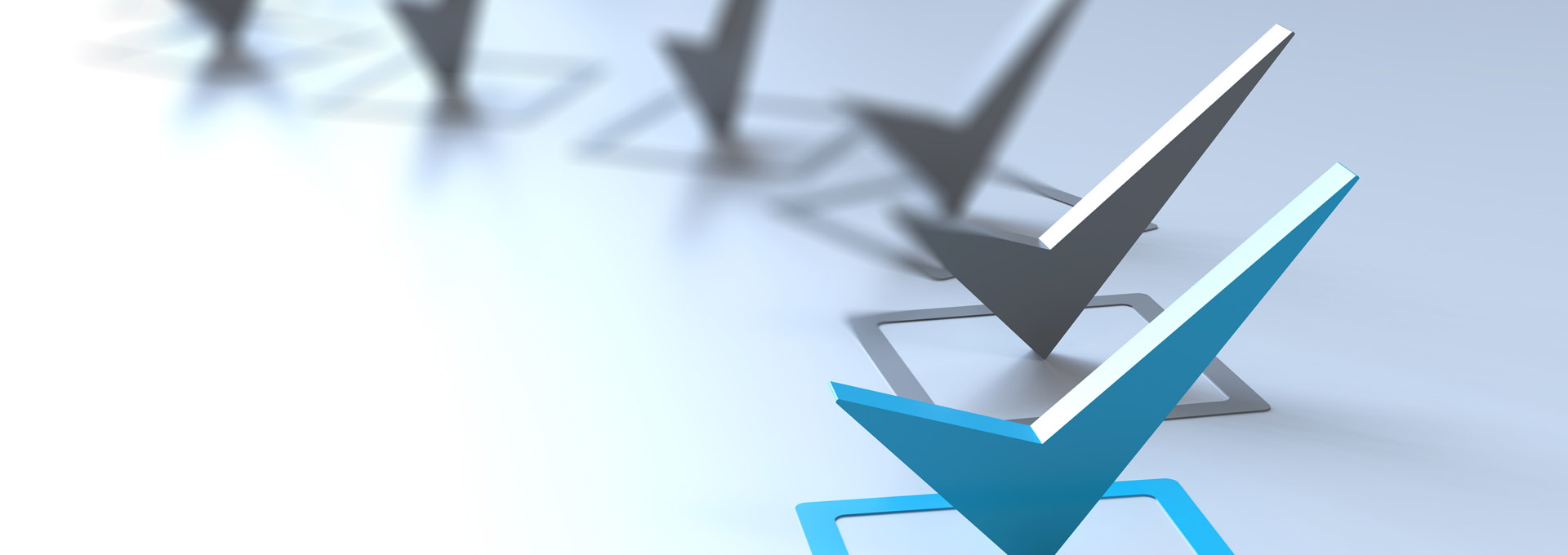
[Author Note: Part III of this series outlining AstraZeneca Biologics’ Product Quality Leader (PQL) explores applying a Gemba Walk to advance the PQL role. Part II looked at the use of a capability/skills matrix to track and advance PQL skillsets and Part I covered the creation of the PQL role.]
The PQL role is established, a team of PQLs built, and a capability/skills matrix developed to help the PQLs succeed and grow. The next step involves expanding their skillsets by applying additional lean concepts that will move PQLs toward continuous improvement and “staying ahead.”
A Gemba Walk is one lean tool used to improve and standardize the critical review processes, the use of which has resulted in more efficient and reliable review outcomes.
First, what is a Gemba Walk? Gemba or “Genba” stems from the Japanese phrase Genchi Genbutsu, meaning “the actual place,” the location where the work occurs. A concept developed by Toyota, a Gemba Walk takes leaders to the heart of the operations bearing a sense of curiosity. They ask questions about processes. They listen and observe. And, in doing so, they find opportunities to support their staff in solving problems. Hence, the Toyota mantra: “go see, ask why, show respect.”
A Gemba Walk is one of the basic tenets of lean management, yet it can be challenging to set up for the quality review function. The department responsible for quality usually does not own, nor is it accountable for, the relevant process or function. Typically, it serves the role of arbiter whose primary objective is to protect and safeguard the patient by assuring compliance with regulations and/or standard procedures.
The team that developed the PQL role at Astra Zeneca recognized that it made more sense to limit the scope of the Gemba Walk solely to the PQL review function. The specification review process was selected because it was deemed critical from the completed PQL capability/skill assessment (see Part II). A Gemba Walk designed for the PQL review process of a typical drug substance/product specification revision is illustrated in Figure 1.
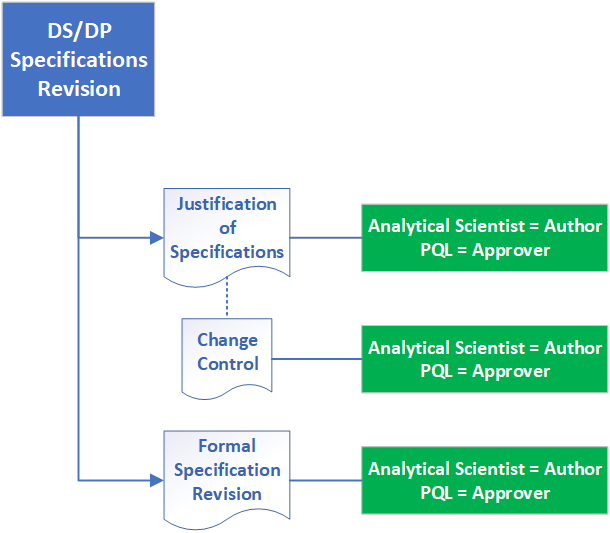
The specification review was a new and intense PQL review task and, overall, a new experience for most PQLs. It examines a critical quality element with potential patient and business impact, which can be revised or reviewed at multiple lifecycle stages for each product. Thus, the criticality of the need to standardize this specific task ranked higher than all other PQL review tasks.
The Gemba Walk was performed by a team, comprising dedicated lean coach and an observer with a high degree of expertise with this review task. This ensured the accuracy and thoroughness of the first review case study. Assessing an actual PQL review process “live,” instead of using a retrospective simulation, was critical to the outcome. The PQL involved was fully trained to execute this critical review process but was not highly proficient at this point, it being a relatively new task.
The PQL had the following documents available at the time of the actual interview:
- AstraZeneca Specification Setting Guidance
- AstraZeneca Standard Procedure for Specifications
- Relevant Justification of Specifications (JOS) form attachments, such as specification committee meeting minutes
- Existing informal “Job Aids,” including a description of the review process steps
- Process flow maps for a high-level specification revision and an initial (detailed) PQL review (neither of which were used in this Gemba Walk)
All documents and information were reviewed from electronic records. The review focused primarily on the JOS form. Because it includes all specification revision information and the relevant content is transcribed unchanged into the master specification form, the JOS form is the main stage of the specification revision process.
A Gemba Walk tracker was used to capture challenges, gaps, or opportunities identified that would achieve a more standardized first-time, complete review cycle. The tracker also included improvement actions which were managed with standard project management tools. At that point, the team of PQLs was fully prepared to present the planned PQL review process improvements to the process owner and other involved parties. By approaching partners in other departments with an emphasis on their benefits, the PQL hoped to more readily obtain their support for suggested changes outside the PQL review.
As a result of the review, the process flow maps for the entire specification process were revised, standard procedures were updated as necessary and a new job aid was written specifically for the PQL review process. An abbreviated version of the new job aid is shown in Figure 2. Any lessons learned from future reviews will be reflected in periodic job aid updates.
Figure 2 (Simplified) Example of a Post-Gemba Job Aid for a PQL Review Task
Clinical Master Specification Review Job Aid | |
---|---|
Description: This guide provides information on how to review AZ Biologics clinical master specifications. | |
Originator: Analytical Source Systems: AZDoc References (in addition to training):
Documents for review:
|
Decision Maker(s): CSSC Advisor(s): CMC Informed: BPD Training Required? Yes
SME(s): CSSC, PQL Team Leader |
PQL Review Guide: When reviewing NEW Master Specifications (MS):
CSSC not required for platform phase I/II
|
|
When Reviewing Master Specification REVISIONS
|
The results and benefits of this focused Gemba Walk for a PQL review task is summarized in Figure 3.
For Product Quality Team | For Stakeholders/Customers |
---|---|
More useable master specification review job aid | Faster approvals |
More consistent and focused review process | Fewer documentation errors |
Fewer review cycles (right the first time) | More suitable and defendable JOS/ Change Control form content |
Throughout all stages of the PQL process, from design to building skills to advancement, most of the feedback from those involved has been positive. Testimonials noted that adding the PQL role has enabled processes to be more flexible while allowing all the pieces of the process to be viewed both individually and as a whole. Because the PQL provides an objective view of a process, there is no fear of voicing concern if a process is unclear or inappropriate. This role has enabled the company to assure that best practices are engaged, ensuring the products that reach the market are safe, effective and available for the patient.