The Urgency for Robotization and Automation Augmenting robotics for the manufacturing of parenteral drugs
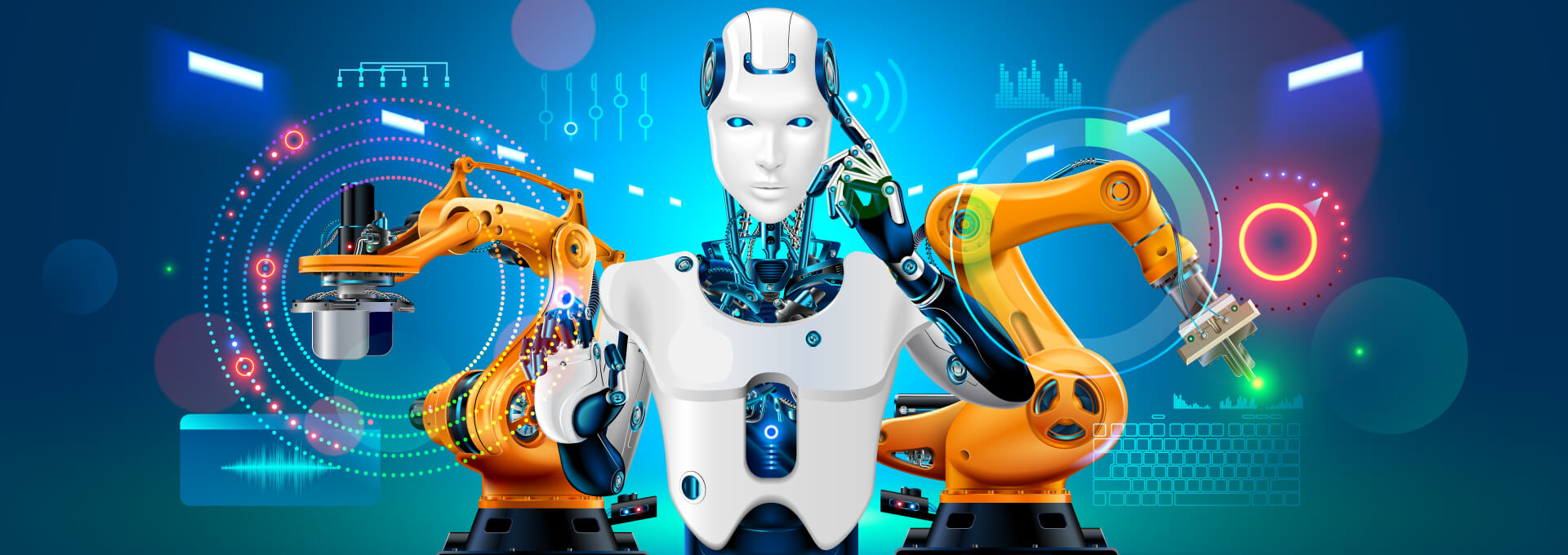
With an investment rate of approximately 14% (pre-pandemic data) in the development of new drugs, the pharmaceutical industry is one of the sectors with the greatest dedication to research and development (R&D). The Organization for Economic Cooperation and Development (OECD) is topped by the aeronautics and space industries (18%) and electronics and optics (17%), which are well above the average for the entire industry (6 per 100) (OECD, 2017). These statistics align with the evolution of parenteral drugs, and they are continually increasing their presence in a highly demanding market. Nonetheless, the expected return on investment in new drugs stands at 1.8%, the lowest point in the last 10 years, and the development costs of a new molecule have increased by 67% in this same period, according to a Deloitte study carried out in 2019 (Steedman and Taylor, 2019). The greater specificity of drugs aimed at a smaller number of patients, followed by the growing competition, are among the reasons for the increase in these costs.
Faced with this situation where margins are decreasing year after year and given the structural complexity of the global framework in the biopharmaceutical industry, a new reality that describes the need to be more efficient using knowledge acquisition should be considered. Furthermore, the latest events experienced because of the recent health emergency forced the pharmaceutical industry to reconsider the current operational dynamics. It is not just about cost reduction or process improvement, but about covering a global need in emergencies with sufficient guarantees.
Augmenting robotization and automation within the industry
Considering long life cycles in the development of new drugs and an increasingly low return on investments, the robotization and automation process (in the broadest sense) constitute the fundamental elements to ensure global supply under the current challenges. Increasing the production of traditional drugs with a global reach and achieving the production of personalized medicines, where precision at the genetic level is required on industrial scales, are the two axes around which the new configuration of pharmaceutical manufacturing revolves. In addition, the large-scale manufacturing of drugs is delegated to CMOs, who must coordinate different products and sponsors using the same equipment. The complexity and variability inherent in manufacturing processes make it increasingly difficult to manage manual operations, adding additional risk factors to an already complex process.
From a patient-centered perspective, the quality, safety, efficacy, availability and access to medicines are crucial elements in the medicine life cycle. The robotization and automation of manufacturing systems are perfect allies to ensure operations are carried out repeatedly, minimizing the impact of variability that is introduced by manual tasks. Due to the different perspectives regarding the benefits provided by robotics and automation, the following questions arise:
- What is the current degree of automation in the pharmaceutical industry?
- Is it enough or can it be increased?
- What are the challenges associated with automating existing systems?
- Is the obsolescence of production lines a handicap for their automation?
- What role does digitization play as a requirement for proper automation?
- Can current automated systems be managed, qualified and validated using the same methodologies created in the 1980s? Should we think otherwise?
Until now, robotization and automation have always been considered within the domain of engineering and linked to mechanical systems. With the appearance of 4.0 technologies, where the information space becomes practically unlimited and computing resources are inexpensive and highly available, artificial intelligence becomes an area with a great impact on the improvement and efficiency of manufacturing processes. The evolution of the robotized and highly automated industry is not just a replica of the robotized arms or sensorized lines with mechanical interactions deployed throughout the last two decades. The transformation of the robotics and automation concept in the industry is pointing in the direction of augmented robotics direction where a network of multiple systems is integrating automated mechanisms and generating more value than the sum of all their contributions. Therefore, the network can self-regulate all the elements involved in the operations, including materials, production processes and human interaction, establishing the quality, efficiency and safety of the drugs as the main priorities.
Moreover, the network of robots and automated systems can recommend those actions that make the interaction more efficient with the full facility. Data sharing is one of the principles. However, smart mechanisms based on artificial intelligence are augmenting robotic capabilities, embedding human cognition to solve unexpected problems and not only those that have been used to train the network.
How about the digital twin concept?
Because the interaction with parenteral drug substances is extremely critical, the digital twin concept is gaining strength in the context of robotization under these manufacturing conditions. A digital twin allows us to obtain knowledge in real time through interaction with the physical world and the implementation of several integrated technologies to increase the robotization of complex systems. Moreover, the Internet of Things, the cloud and artificial intelligence are orchestrated to obtain a virtual representation of reality that must be interpreted and analyzed in real time as the real-time digital counterpart of a physical object or process. When the information flows in both directions and the interaction between the virtual and physical worlds occurs in an equal and simultaneous way, the systems can be managed indifferently from the physical or virtual world. This feature gives the digital twin the ideal capabilities to automate critical processes under sterile manufacturing conditions. The new generation of robots and process automation systems is based on the mechanical extension that articulates physical movement. Under the new paradigm of autonomous and adaptive control, digital twins are defined as intelligent management mechanisms that operate through the mechanical extensions of robotics and classical engineering. Its best fuel is digital information.
Given the configuration of robotization and automation in which articulated mechanics is assumed to be commodity and the added value is achieved through human emulation, a new way of automating plant knowledge in critical decision-making is outlined. The concept of adaptiveness is closely linked to the complexity and unexpected changes that appear in any industrial process. Classic robots and automation systems continually repeat a pattern, but by incorporating new technological elements, they are capable of learning and responding to new situations. Hence, in this way, a new horizon is opened for pharmaceutical manufacturing that allows the implementation of more controlled and safer systems, thus responding to an incessantly changing and global need for the benefit of patients.
References
- OECD. (2017). The next production revolution: implications for governments and business. Organisation for Economic Co-operation and Development OECD.
- Steedman, M., Taylor, K., Properzi, F., Ronte, H., & Haughey, J. (2019). Intelligent biopharma: forging the links across the value chain. Deloitte University EMEA, Belgium,