Think Globally, Work Virtually in the Era of COVID-19: The Future of Biotech Success
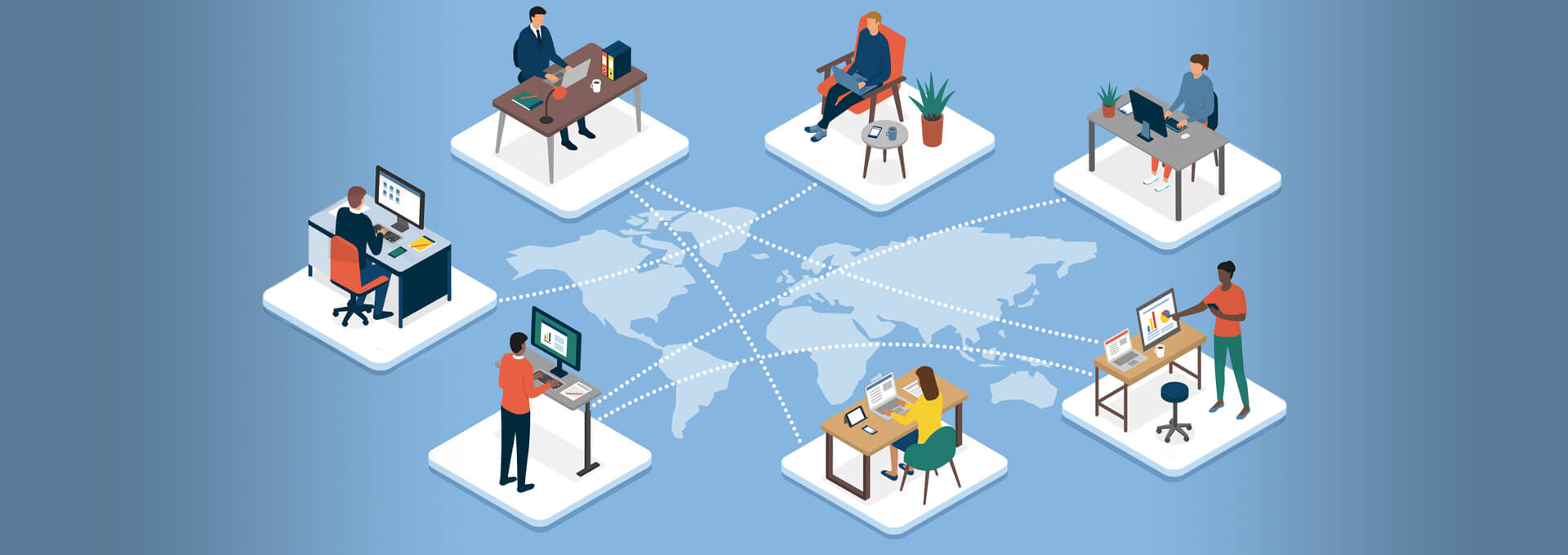
The year 2020 has forced the Biotech industry to work around imposed restrictions on business travel, social distancing, group gatherings, and increased use of personal protective equipment. Even though the concepts of remote, virtual work existed before 2020, it has found a new importance and priority in today’s reality. In order to be able to achieve work objectives without interruptions, the biotech industry, as well as the rest of the business world, have been forced to rethink the concept of remote work and how to adapt to it efficiently.
In the biopharma consulting industry, it used to be a common perception that consultant expertise must be local to the source of need. However, the biotechnology industry is volatile and often resource-limited which makes local, affordable, world-class drug and device expertise difficult to find. Ideally, the expertise comes from seasoned, collaborative and highly specialized individuals who can tailor their advice specifically to the company and product. In an era of all-encompassing communication technologies, why would it matter where the expertise is physically located?
The pool of talented drug and device experts does not have to be limited to one’s immediate geographic area. To support this claim, here are two success stories of virtual teams working together remotely to achieve their target goals.
The first example took place a few years ago and involved two teams on opposite sides of the world. They came together and successfully accomplished a global regulatory filing for a medical device six months ahead of the planned deadline.
A large European pharmaceutical company had acquired a small but innovative Canadian biotech company. There were concerns as to how the Canadian and the European teams would interact because the virtual team was cross-cultural and there was a nine-hour time difference between them. The Canadian team had a very strong clinical and regulatory development skill set, specializing in drug approvals in the US and Canada, while the European team was excellent in overcoming the hurdles of Europe’s EMA. Most of the key team members worked virtually and maintained a positive dynamic by relying on web-based communication tools for their team discussions.
The Canadian and European teams also tag-teamed their workflow. The Europeans would work eight hours on a regulatory submission, while the Canadians would continue working another eight hours after the end of the European workday. In some cases, their colleagues in Asia and Australia continued the work for another eight hours, in order to complete submissions for certain countries in Asia and Australia. This global work process resulted in a faster, successful global product registration for the European company. The product is now approved in over thirty countries.
The second example involves a group of five to six highly experienced pharma subject-matter expert (SME) consultants, located in different parts of North America. They were assembled for a project to assist a product company and contract manufacturer in the U.S. Midwest with pivoting to manufacture a healthcare product for the COVID-19 pandemic.
The project had a strict several-month timeline, and a key objective was to ensure the product is manufactured in compliance with U.S. FDA and Health Canada GMP regulations. The virtual team provided strong leadership and direction for identifying, creating and executing a project plan for success.
Some of the major tasks included:
- Development and remediation of required quality management system processes and GMP documentation
- Deliver a portion of personnel training through virtual means
- Provide some onsite presence by one or two SME’s
- Conduct an engineering review of the manufacturing facility.
A variety of modern communication technologies and e-collaboration tools were utilized to provide continuous contact, convey information to move the project forward, and support the client team. The goal of the project is to assist the client company with obtaining WHO GMP certification, under which the product will be manufactured within compliance.
In both examples, the achieved objectives required reliance, trust and work flexibility between all team members. Another key to a successful virtual team is strong and solid leadership. Furthermore, the use of this kind of team may also involve adopting a different mind-set towards the way team members interact with each other. By using virtual teams, companies no longer must compromise on obtaining quality talent and bringing in new team members becomes more cost-effective.
Nevertheless, there are ongoing challenges posed by remote engagement. A particular challenge is meeting the need for an onsite quality assurance presence. Assurance of GMP quality in industry onsite activities requires physical presence and real human-to-human interactions. How can this objective be met in these new and unprecedented circumstances created by the pandemic? Part of the solution is having a reduced-size onsite team to act as the “eyes and ears,” while also utilizing remote communication tools for real-time support from a larger team.
Unfortunately, there is a perception of industry sluggishness when it comes to adopting electronic and automation systems, leading to higher human labor needs and human error. Aseptic processing and sterile product manufacturing technologies are inherently and traditionally manual labor-intensive operations. They have numerous required control parameters throughout their processes to ensure product quality and safety. There are, however, recent trends of emerging automation technologies for aseptic processing which are slowly gaining traction and frequently described in the PDA Journal of Pharmaceutical Science and Technology and other sources.
Much has been published recently about the necessity and challenges of auditing by remote means. There is gathering evidence of success and strategies for increasing effectiveness within this mode of inspection. However, the loss of communication through non-verbal cues and body language has been an ongoing challenge. Both channels are important parts of auditor’s onsite perception and evaluation.
It is neither likely nor desirable that remote work will fully replace the need for human-to-human interactions. There are many complex challenges and problem-solving situations in aseptic processing and parenteral manufacturing which require in-person meetings and onsite presence. The industry is rising to the unprecedented challenge of our times and the adaptation process is still ongoing. Given that many new and innovative biotechnology products do not make it to market due to deficient development programs, the use of accomplished drug and device development experts are vital. Obtaining drug and device expertise in a virtual environment may be the key to future success in the ever-changing landscape of biotechnology.