Viscous Product No Match for New CCI Tech MicroCurrent HVLD Might Ensure Better Container Closure Integrity for New Product Formulations
New product types and packaging configurations, such as highly viscous formulations, pose a significant threat to traditional leak-testing methods, challenging current practices for container closure integrity testing (CCI). In light of this, a series of feasibility studies was conducted to challenge traditional leak-testing methods. Using real-world positive control methods conducted to detect defects occurring in the manufacturing process, MicroCurrent High Voltage Leak Detection (HVLD) proved a significantly better test for highly viscous low conductivity products. The studies showed that Micro- Current HVLD can achieve a reliable leak detection limit even all the way down to critical leak sizes.
Liquid properties are critical in testing for CCI. For HVLD test methods, liquid conductivity can impact test method performance. MicroCurrent HVLD has been recognized as a technology that can leak-test a wide range of product conductivities and chemical characteristics. This is practical for leveraging test method development on products with different liquid conductivities. If a manufacturer is producing 1mL syringes, they may be filling the syringes with different types of parenteral product. MicroCurrent HVLD can also be used to develop test methods for such a broad range of liquid conductivities (Figure 1). Once a method is validated on a range of product conductivities, the resulting broad range of method development can be leveraged as a bracket to validate the test method for other parenteral products within that conductivity range.
Test method development for CCI requires challenging the test method with known good samples and positive controls (leakers). Positive controls can be made using laser-drilled defects; these can then be accurately measured to test specifications.Typical defects from the manufacturing process generally do not manifest as a fine pinhole in the glass—cracks are the more common defect. Traditional vision methods may not detect crack defects in complex geometries or hidden portions of the container. Crack defects that better reflect real world circumstances can be created using a process involving rapid thermal fluctuation. To challenge MicroCurrent HVLD technology, researchers scratched the glass surface, heated the glass and applied a droplet of cool water to the scratch site to create cracks.
The culmination of the studies established the sensitivity and range of product conductivity that can be tested with MicroCurrent HVLD. Crack style positive control samples were created in both vials and syringes. The cracks were certified using the helium leak test method and showed defect flow rates to below the one micrometer diameter defect size. The results produced reliable detection of micro leaks down to helium leak rates of 0.25 10-5 mbar·l/sec (equivalent to a 0.15 micrometer pinhole) placing the MicroCurrent HVLD test method at the forefront of CCI test sensitivity.
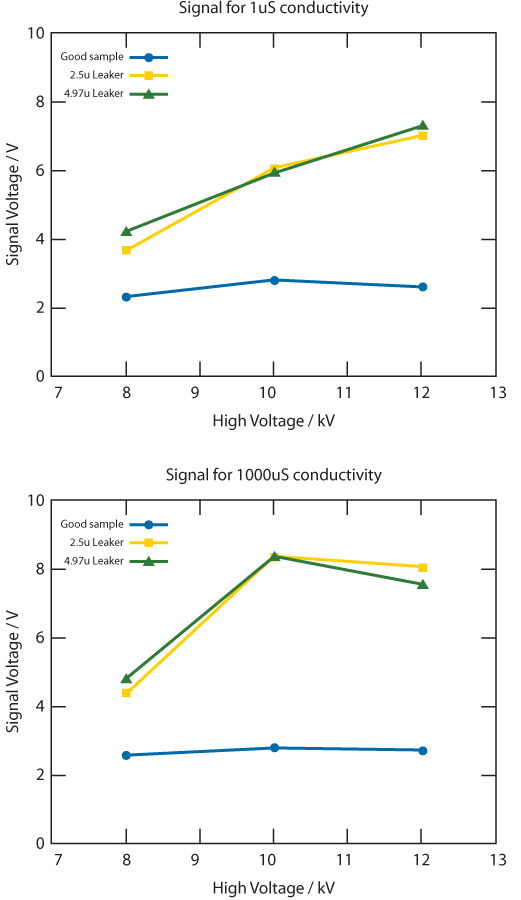
Sensitivity of a test method is crucial to providing greater assurance against the risk of microbial ingress. The results using a range of products and defect types accurately determined CCI across the full range of sample sets. While the sensitivity of a method is crucial, the reliability of a test method is at the very foundation of the container closure integrity testing.
These studies suggest that MicroCurrent HVLD technology could help ensure container closure integrity of new types of drug products with viscous formulations. No matter how innovative the drug product or packaging, container closure integrity will remain a critical part of ensuring the sterile barrier.
[Editor’s Note: Additional figures and images can be found in the online version of this article.]