Visual Inspection Practices of Cleaned Equipment: Part II
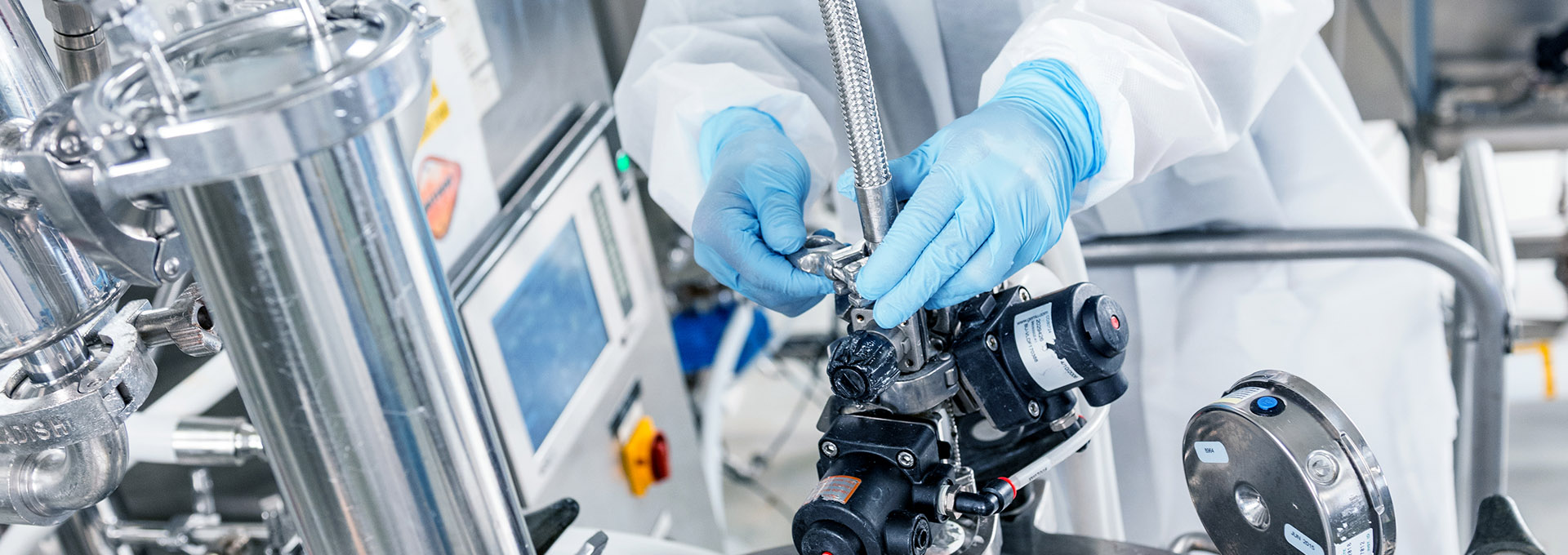
Photo courtesy of Steris
Note: Part I reported results of a Steris survey and discussed how terminology and visual inspection practices for cleaned equipment differed among responding manufacturers.
European manufacturers interpret the criteria for “visually clean” in various ways, based on their experience executing the cleaning process and on their own interpretations of the regulatory requirements (1). Still, a formal visual inspection training and qualification program and instructions should be established to prevent the risk of contamination and to verify that equipment is cleaned based on a manufacturer’s set of controls (2).
Variability in practices between manufacturers is acceptable. Operators, however, must be periodically trained and qualified on when to visually inspect clean equipment and how to distinguish between product residue and surface imperfections that may impact the visually clean criteria. The case study below illustrates why this is important.
Case Study: Inspection Observation on Visual Inspection
Recently, U.S. FDA inspectors delivered an observation to an anonymous biopharmaceutical manufacturer regarding visually clean criteria. During a tour of the company’s shop floor, one of the inspectors checked out the upstream room where two fermenter vessels were located. The vessels are part of a closed system and are cleaned using a fully automated clean-in-place (CIP) system. The CIP cycle of one of the fermenters finished one hour before the inspector entered the upstream room. The inspector looked inside the vessel through the sight glass, observed a few condensation droplets and noticed the surfaces were not shiny. This did not convince the inspector that the vessel was “visually clean” (Figure 1).
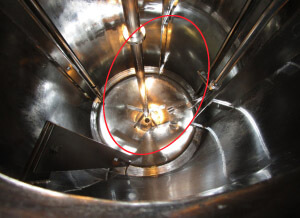
This led to the following observation: “Discoloration was observed in Fermenter (Equipment ID XXXX). This specific issue had not been evaluated by the firm. This fermenter is used for [product name] fermentation.” [Editor's Note: Quotes are from the resulting regulatory document.]
This observation raised a lot of questions and impacted several control strategies. Since it occurred after a cleaning cycle where a systematic (routine) visual inspection was carried out, it affected the cleaning control strategy and the maintenance program in place to ensure that the vessel surfaces were in an acceptable condition. These two programs were not aligned on how to inspect and manage vessels. What could be more practical than a daily visual inspection to confirm an acceptable surface state before confirming the visually clean status?
The biopharmaceutical company was able to justify the presence of droplets after the CIP process was completed as acceptable, mainly because the clean hold-time (CHT) was successfully validated in similar clean conditions. The inspector understood the situation (that the equipment was observed immediately after the CIP process) and accepted the justification.
Regarding the discoloration on the vessel wall, there was also an explanation. Various conditions may generate discoloration of the stainless steel when it is in contact with specific products, chemical agents or thermal effects. This is known as the surface internal weathering effect. The change in the surface may change the visual inspection condition, which may alter an inspector’s (or operator’s) decision on whether the surface is visually clean—even if the manufacturer has a high-quality training and qualification process.
The observation itself is clear: the “discoloration…had not been evaluated” while the equipment was being used on a routine basis to produce biological bulk. It did not, however, refer to a specific requirement.
How did the firm respond to this observation?
- The firm acknowledged that surface discoloration was detected during the FDA inspection and had not been evaluated before the inspection.
- An immediate action was implemented to investigate the discoloration, samples were taken for analysis, and the fermenter was not used.
The investigation demonstrated that decontaminating the vessels using caustic or other chemical agents at high temperatures (greater than 100 °C) stressed the vessel walls and could cause a chemical reaction to appear on stainless steel surfaces. Electropolishing only temporarily restores the surface of the vessels. Indeed, the decontamination and cleaning processes have since then generated discolorations on the internal surfaces of the fermenter.
There is a lesson to be learned from this FDA observation: The scope of the visual inspection by an inspector (e.g., operators or technicians) after a cleaning process should be well defined. The decontamination and the cleaning processes make a lasting impact on the structure of equipment over time. The processes in place for cleaning, decontamination and maintenance must be consistent, aligned and phased. Therefore, the cleaning and maintenance control strategy must be able to address the following challenges:
- How to evaluate and document the “visual imperfections” of the material that constitutes the equipment
- How to adequately define an acceptable dryness level prior to visual inspection
- How to train inspectors (operators, technicians and subject matter experts) to visually clean and to acceptable surface imperfections?
- How to define a surface imperfection that would lead to equipment disqualification
- How to determine if the role of visual inspection should include the control of surface imperfections?
How to Inspect for Visually Clean Status
Most inspectors (operators) throughout the industry have been inspecting and releasing manufacturing equipment based on experience (1,2). Yet, distinguishing product residue and surface imperfections could be difficult for operators.
To address that issue, operators should be trained on equipment constructed of the same materials and in the same situation that presents the target residue(s) they will be expected to visually detect. The training procedure and support to ensure reproducible visual inspection should contain, at least, the following sections:
1. Definition of visually clean criteria
Visually clean, defined as “the absence of visible residue on a surface,” should be properly defined as an acceptance criterion in the procedure.
In addition to descriptions, pictures (Figure 2) of visually clean surfaces in a procedure or training course are the best option. The visual inspection could detect much more than product residue.
Recent studies demonstrated that training the inspector to differentiate between residue on the surface and noncritical surface imperfection or discoloration is important to visually inspecting clean surfaces (2, 3). In some cases, operators could be made aware of the level of discoloration or imperfection that is acceptable on the surfaces, as some consider this surface control as part of the maintenance or engineering program.
The level of acceptable dryness of equipment or the drainability category and conditions could be made part of the definition or could be included in a cleaning risk evaluation.

2. Scope of the visual inspection
Which surfaces must be visually inspected? All equipment surfaces that directly or indirectly contact the product, bulk or intermediate material should be visually inspected. As not all surfaces of a piece of equipment may be visible for visual inspection, the scope could be tailored to the type of equipment. How and what to visually inspect on the surface should be discussed.
3. Surrounding conditions to visually inspect a clean surface
The conditions surrounding the equipment to be visually inspected impacts the ability to properly detect residue, making that environment an important element. The amount of detectable residue (visible reside limit) is product-dependent and needs to be defined on a case-by-case basis or by the grouping approach (2–6).
To confirm the impact of the surrounding conditions on a visual inspection, the following factors should be analyzed:
- Viewing distance: The distance between the surface and the operator. This viewing distance may not be easy to simulate in a laboratory; however, common sense dictates that the greater the distance, the harder the visual inspection may be. The inspector’s visual acuity at a specific distance also plays a role.
- Light levels (approx. from 400 to 1500 Lux in normal cleanrooms): Some coupon studies have indicated that light levels between 200 and 1400 Lux may not alter an inspector’s visual inspection; still, this should be demonstrated via actual situations.
- Viewing angle: The viewing angle between the inspector’s eyes and the surfaces to be visually inspected should also be considered and integrated into the process of visual inspection. Depending on the angles and the light levels, an inspector may see some reflections that would make it difficult to confirm visually clean.
- Secondary light: The use of a flashlight is not recommended when the cleaning validation runs were not inspected with a flashlight. Conditions of inspection must be similar between validation runs and routine cleaning and maintenance.
Understanding the surrounding factors that may alter visual inspection is key to preventing inadequate decisions.
4. Timing of performing visual inspection
A visual inspection should be performed after a completed cleaning operation. At the same time, this is often not part of the documentation and can result in questions about conducting the visual inspection conducted in the event a cleaning cycle is aborted. The procedure should specify how long after the end of the cleaning cycle a visual inspection should be performed. This timing should be determined to ensure the operator is safe when opening a vessel (e.g., the rising step is generally performed at high temperatures). This timing impacts the water or solvent draining process and could prematurely invalidate the inspection.
5. Methodology to visually inspect
A structured methodology to visually inspect clean equipment should be established. For example, a manufacturer could develop a checklist that identifies the various parts of the equipment to be visually inspected in a coherent visual path. In addition to following the method for general visual inspection, some manufacturers have developed checklists identifying specific parts or known worst-case locations that should be visually inspected.
6. Identifying the visible targeted residue(s)
Operators should be introduced to all the elements they may examine during the visual inspection. These elements could include the product residue, surface imperfections, surface damages, residual water and particles, among others.
The operator will inspect the visible surfaces with all their imperfections. They will also be able to detect many other elements or anomalies, starting with defects related to the material, its aging, traces of residual water, particles, and product residues (Figure 3). Therefore, the visual inspection target and acceptance criteria must be clearly defined.
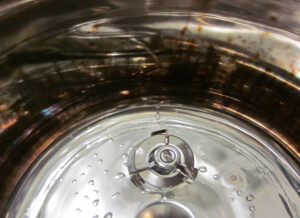
The level of formality in developing these six sections depends on the company’s cleaning risk assessment and control strategies.
Conclusion
Visual inspection is the method of choice to confirm visually clean status. Most inspectors (operators) throughout the industry have been inspecting and releasing manufacturing equipment based on experience (1,3). It could be difficult, however, for operators to distinguish product residue and surface imperfections without proper training and qualification. Consequently, properly training operators and making sure all materials of construction and in similar situation are offered to visually detect the target residue(s) and surfaces imperfection that could impact the visually clean status makes sense. A formal visual inspection training and qualification program as well as instructions should be established. This program should be based on the set of controls the manufacturer uses to verify equipment is clean. Therefore, visual inspection as defined and qualified could be a preliminary control method for a cleaning risk management strategy.
Both authors were involved in drafting the manuscript and approved the final version. The development of this article was sponsored by GlaxoSmithKline Biologicals SA and STERIS. The authors declare the following interest: Walid El Azab is an employee of STERIS, Stephane Cousin is an employee of the GSK group of companies.
References
- El Azab W. and Cousin S., “Visual Inspection Practices of Cleaned Equipment: Part I,” accessed April 2020: https://www.pda.org/pda-letter-portal/home/full-article/visual-inspection-practices-of-cleaned-equipment-part-i
- Walsh, A., et al., “Justification & Qualification of Visual Inspection for Cleaning Validation in a Low-Risk, Multiproduct Facility.” Pharmaceutical Online (Aug. 3, 2018) https://www.pharmaceuticalonline.com/doc/justification-qualification-of-visual-inspection-for-cleaning-validation-in-a-low-risk-multiproduct-facility-0001
- Desai, P. and Walsh, A. “Validation of Visual Inspection as an Analytical Method for Cleaning Validation.” Pharmaceutical Online (Sept. 11, 2017) https://www.pharmaceuticalonline.com/doc/validation-of-visual-inspection-as-an-analytical-method-for-cleaning-validation-0001
- Forsyth, R.J., et al. “Visible-Residue Limit for Cleaning Validation and its Potential Application in a Pharmaceutical Research Facility.” Pharmaceutical Technology 28 (Oct. 2004): 58–72 https://pdfs.semanticscholar.org/ea64/d01db84d3b8a5a62f1c824abf8484af363dd.pdf
- “Application of Visible-Residue Limit for Cleaning Validation.” Pharmaceutical Technology 29 (Oct. 2, 2005) http://www.pharmtech.com/application-visible-residue-limit-cleaning-validation?id=&pageID=1&sk=&date=
- “Determination of Surface Visible Residue Limits on Pharmaceutical Plant Equipment,” Pharmaceutical Technology (Feb. 2, 2013) 37 http://www.pharmtech.com/determination-surface-visible-residue-limits-pharmaceutical-plant-equipment?id=&pageID=1&sk=&date=