Zero Defect – A Competitive Advantage
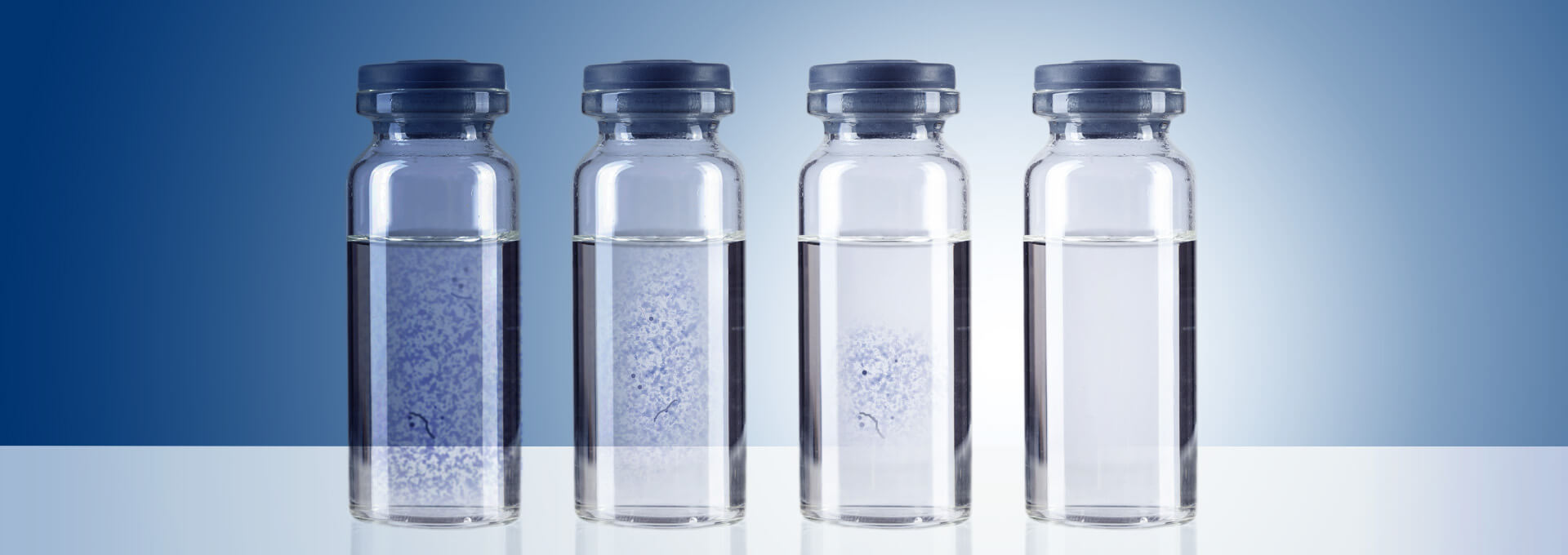
With the recent focus on producing high quality, affordable medicines, the pharmaceutical industry faces pressure to reduce expenses without compromising quality in manufacturing. Quality programs, such as Zero Defect, add value by reducing costs, significantly improving quality and making a predictable supply of medicines available to patients. One area in a pharmaceutical company where this concept can be immediately applied to great benefit is working with raw materials and components (raw materials).
Zero Defect is not a new term in the quality world; it was coined by Philip Crosby in his 1979 book entitled, Quality is Free, and has emerged as a popular, highly regarded concept in quality management. Zero Defect can provide an aspiration for the company to stay competitive.
Zero Defect is a process of continuously evaluating and improving end-to-end processes from the supplier to the company. The objective is to produce the highest quality product while reducing defects to the lowest possible level by using high-quality raw materials. Zero Defect is not a quick fix; rather, it is a collaboration between the company and its suppliers to improve processes.
The challenge for companies is to bring defect-free new products to patients faster and more inexpensively than ever. This has led them to evaluate their internal processes and operating models to find ways to reduce waste by focusing on reducing defects, quality issues in manufacturing and scrap and complaints, and by eliminating avoidable testing, while proactively adopting quality programs. Strong relationships between the company and its suppliers are essential for improving quality in the long run.
This article discusses how the Zero-Defect concept can be applied to improve raw material quality and what it would take to realize the vision of this continuous improvement.
The Context
Some of the quality dimensions in this article can be used as strategic analysis and performance management tools that assist in moving a company closer to its continuous improvement aspiration. In this case, right-first-time (RFT) metrics for all raw-materials quality defects were analyzed for a period of 10 years to determine suppliers’ performance (Figure 1). In addition, the reduction of recurring quality defects was analyzed as a measure of raw material quality improvement over a period of 5 years (Figure 2). Note that these two performance measurements are inversely proportionate and that RFT and recurring defects stabilized at 99.6% and 6 defects.
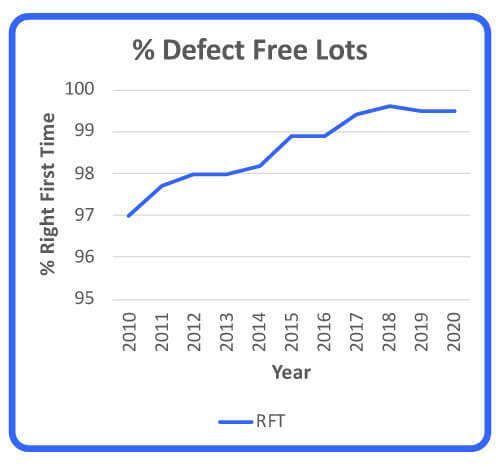
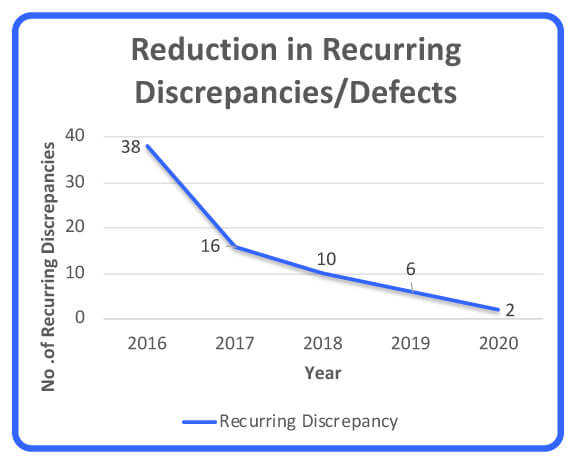
Although difficult to measure, the issue of quality due to raw materials may also be seen at manufacturing sites, leading to disruption in the manufacture of products and potential stock-outs. Hence, collaborating with internal stakeholders also provides opportunities to improve raw material handling and testing processes.
The Why
Most companies take reactive measures to reduce raw material defects, given the time constraints they are under and their general focus on fixing the issues to release products to the market for patients. Instead, companies should proactively identify, evaluate and prevent potential raw material defects. The proactive approach will help the company move from a “cost-driven” to “value-driven” mindset.
For raw material defect reduction, it is essential to have continuous improvement as the objective by increasing the understanding and capabilities of raw material suppliers. As part of the process, it is also important to continue evaluating and optimizing raw material supplier performance by reducing defects. Having a clear objective and taking such measures will unequivocally reduce waste, minimize the cost of quality, and provide a planned, predictable supply of high-quality medicines to the patients.
The What
To evaluate a company’s readiness, all stakeholders must agree on a common definition of Zero Defect.
A company’s objective should be to reduce defects in raw materials delivered by suppliers, ensuring that all lots of materials received from all suppliers meet the agreed-upon specifications/requirements. Striving for Six Sigma performance for critical material attributes (CMAs) by effectively eliminating known defects and preventing potential defects leads to maintaining the highest product quality. While perfection may not be achievable, the quest for it will push quality and improvements to the point that is acceptable under even the most stringent metrics.
Our recommended definition of Zero Defect is the absence of any defects from the suppliers of raw materials, that is:
- Raw materials lots received from the supplier are within the agreed-upon specifications/requirements
- All quality attributes, as listed in specifications, are within and/or below the acceptance criteria (e.g., AQLs, ppm).
The How
Having a cross-functional team brainstorm to collect ideas about how to reach the goal of Zero Defect is a best practice.
The six areas of improvement, shown as the spokes of a wheel in Figure 3, represent quality risk management and potential improvement opportunities for a company. An engrained quality mindset and prioritization principles should also be applied. In addition, considering the cultures of both the company and the supplier is important to the success of such an endeavor. The focus should remain on the critical raw materials.
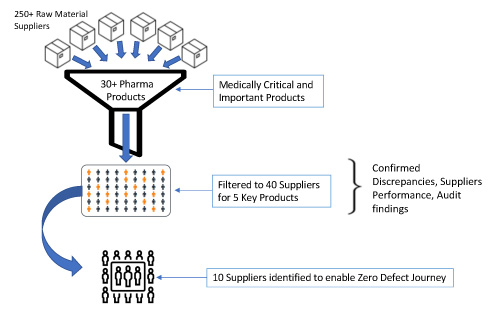
The spokes on the wheel represent critical activities that should be evaluated and improved. Consider reviewing the following elements strategically:
- Prioritization: Use the company’s product portfolio to identify strategic raw material suppliers and prioritize the suppliers by the criticality of the raw materials supplied.
- Usage and Handling: Ensure processes are in place at the company for proper handling of raw materials and are in alignment with the supplier’s recommendation.
- Use of Correct Tools: Ensure that the use of correct measuring tools and test methods at the company are in alignment with the supplier’s recommendations.
- Alignment of Specifications: Align on specifications of raw materials with the supplier, including agreed-upon CMAs.
- Redefining the Receipt Inspection: Ensure that testing and inspection are in alignment with the supplier’s recommendations.
- Continuous Improvement Mindset: Educate suppliers about the company’s raw material requirements and clearly define expectations.
A company should take a deeper dive into the data and prioritize critical materials supplied for strategic products, and then select suppliers based on the historical data of their performance, including defects and defect trends.
Based on experience, Figure 4 illustrates how a company can start with a list of more than 250 suppliers and narrow it down to a manageable number.
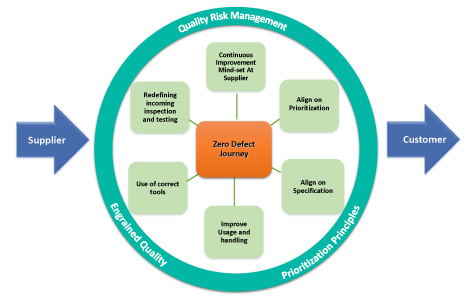
To be highly successful in this process, a company can engage and enlist internal stakeholders, bring suppliers on board, and evaluate the end-to-end process to establish a manageable group of selected suppliers.
Enabling Factors
For Zero Defect to be successful, several enabling factors play an important role:
- Prioritization: Stay focused on prioritization of raw materials and suppliers for strategic products.
- Messaging: Ensure transparent communications to all levels of the company by simple messaging to build allies.
- Visible Management Commitment: Ensure top management shows support for Zero Defect and encourages middle management to carry out the message.
- Governance: Establish governance between the company and the suppliers to maximize commitment.
- Sponsors: Consider having sponsors at the company and at the supplier who have a strong understanding of the raw materials for resolving escalation of disagreements and removing roadblocks.
- Expertise: Engage and empower Six-Sigma experts who fully understand the issues, processes and impact on a company’s products to help carry out raw material improvement.
- Link to Supplier Quality Strategy: Relate reducing defects and decreasing internal customer pain directly to the company’s overall supplier quality strategy.
The Case Study
This case study is presented to provide granularity of the process undertaken to improve the system for selecting, evaluating, and monitoring the supplier of raw materials for the primary packaging of a pharmaceutical manufacturer.
The Problem
Company X was working with a packaging component supplier whose packaging components failed significant dimensional and visual inspections. In addition, the specifications, the inspection and test methods, and the defect criterion had been misinterpreted between the company and its supplier. Consequently, Company X began examining alternatives using the Zero-Defect initiative for primary packaging raw material suppliers by applying the Define, Measure, Analyze, Improve, and Control (DMAIC) process. The emphasis on defining, measuring and analysis ensured that opportunities for improvement would be executed in a way that provided the most positive impact.
The Process
Company X first defined the project:
- Developed a business case and project charter to clearly define expectations of both the internal team and the supplier team
- Selected a project sponsor who was impacted the most
- Selected project core team members
- Limited the team size, adding ad hoc team members as needed
- Mapped the project timeline
- Established a communication plan
- Updated the project charter and timelines as needed
The Company then determined how it would measure the processes and progress made:
- Performed a GEMBA walk for process visualization
- Developed a process flow and reviewed the end-to-end processes for
- Manufacturing
- Quality – inspection and testing
- Shipping – both the internal material flow and supplier chain processes
- Performed deviation and product-complaint analysis
- Reviewed risk assessments and identified critical quality attributes
- Classified defects as critical, major or minor using risk-scoring methods
Company X analyzed the data collected on:
- Agreed-upon specifications for raw materials – inspection and test methods, inspection set-up aligned with USP <790> and a measurement system analysis
- Critical quality attributes
- Sampling strategy – outgoing for the supplier and incoming inspection for Company X
- Raw material shipping process against the agreed-upon requirements
- Supplier’s Zero-Defect program and how it aligned with its customer service program
Based on the information gathered, Company X determined elements that could be improved:
- Defined an implementation plan based on the findings from its analysis
- Implemented corrective and preventive actions (CAPA)
- Reviewed and monitored the improvement activities
- Performed a CAPA effectiveness check
- Adjusted the project timeline as needed
To ascertain that all systems were in control, Company X:
- Performed efficacy monitoring of the incoming material for 12 months
- Recognized that the number of defects had been reduced significantly, demonstrating that the preventive measures the supplier had implemented were highly effective
Conclusion
Pharma companies consider quality a strategic advantage and are aware of their quality niche. In order to stay competitive and uphold their reputations, they must remain focused on improving quality by exploring opportunities and pursuing quality measures in every aspect of production.
In summary, a focus on Zero Defect adds value to the product, significantly improves quality and provides a predictable supply of high-quality medicines to our patients. Continuing on this journey of effecting Zero Defect will support more patient benefits at less cost to society.